Producatori de consumabile de sudura. Investiții și profit din producția de electrozi. Tehnologie și echipamente pentru producția de electrozi
Un electrod de sudare este o tijă metalică sau nemetalică realizată dintr-un material conductiv de electricitate, care este proiectat să furnizeze curent piesei de sudat. Electrozii de sudare se folosesc ca sudura manuala diverse oțeluri carbon și aliaje și sunt împărțite în două tipuri principale: consumabile și neconsumabile. Electrozi neconsumabile sunt realizate din materiale refractare (de exemplu, wolfram, cărbune electrotehnic sau grafit sintetic) conform GOST 23949-80 „Electrozi de sudură tungsten, neconsumabile”.
În fabrici s-au înființat ateliere de reparații folosind tehnici și instrucțiuni de sudare și sudare, cu accent pe pregătirea sudorilor. Locul principal al companiei era echipa de pe stradă. Biroul studio organizat aici a deținut o gamă largă de lucrari de sudare, a elaborat publicații teoretice și a oferit consiliere părților interesate. Profilul de producție s-a mirat de bogăția sa. Pe lângă pistoletele și pistoletele cu gaz și pistoletul, s-au creat mașini pentru tăiere automată și semiautomată, mașini solide și portabile pentru producerea acetilenei, compresoare și pompe pentru transfer oxigen, stații de sudură staționare și portabile, electrozi, pulberi de sudură și paste, chiar și un aparat cu gaz pentru tratare.
În prezent, există peste două sute de mărci diferite de electrozi. Locul predominant este ocupat de electrozi consumabili pentru manual sudare cu arc care sunt realizate din sarma de sudura. Acesta din urmă conform GOST 2246-70 poate fi carbon, aliat și puternic aliat. În timpul procesului de producție, pe tija metalică se aplică un strat de acoperire de protecție prin presare sub presiune, al cărui rol este de a trata metalurgic bazinul de sudură, de a-l proteja de acțiunea atmosferică și de a asigura o ardere mai stabilă a arcului.
Un album cu acest design, produs în fabrică, s-a bucurat de mare interes în toată Europa. Asociația a devenit membru permanent al Comisiei Internaționale pentru Acetilenă și Oxigen. Zaloga a încercat să supraviețuiască ocupației, iar cea mai mare parte a atenției s-a concentrat pe contracararea distrugerii centralei de către ocupant.
Odată cu sfârșitul războiului, era timpul pentru reorganizare. Independență față de toate ramurile și instituțiile suburbane. A început producția de regulatoare, torțe, generatoare de acetilenă, electrozi și pulberi de sudură. Cererea de echipamente de sudura a crescut sistematic.
Pe lângă clasificarea de mai sus, electrozii sunt împărțiți în mai multe clase principale: electrozi pentru sudarea oțelurilor aliate rezistente la căldură, electrozi pentru sudarea oțelurilor înalt aliate cu proprietăți speciale, electrozi pentru sudare oteluri de structura folosind sudarea cu arc, electrozi pentru sudarea metalelor, electrozi pentru sudarea metalelor neferoase, electrozi pentru sudarea fontei. De asemenea, electrozii de sudare sunt împărțiți în clase, în funcție de tipul de acoperire: A (electrozi acoperiți cu acid care conțin oxizi de fier, siliciu și mangan), B (acoperire de bază, care are carbonat de calciu și fluorură de calciu în înveliș), C (acoperire cu celuloză). Principalele componente ale acoperirii celulozice sunt făina și alți constituenți organici. Aceste componente sunt adăugate învelișului special pentru a crea protecție împotriva gazelor în timpul sudării. Există, de asemenea, electrozi de clasă P cu acoperire rutilă(plus o cantitate mare de substanțe organice și minerale suplimentare, care garantează o stropire ușoară a metalului și oferă protecție împotriva gazelor în timpul procesului de sudare). În cele din urmă, electrozii sunt împărțiți în patru tipuri în funcție de pozițiile de sudare admise: toate pozițiile posibile; toate pozițiile posibile, cu excepția verticală de sus în jos; jos, orizontal și vertical de sus în jos, precum și poziția de jos.
De atunci, a fost implicat în producția principalului echipament de sudură si fitinguri pt gaze tehnice. Pentru implementarea acestui program au fost extinse biroul de construcții și biroul tehnic. Dezvoltarea rapidă a sudării ca știință a necesitat introducerea continuă a schimbărilor în produsele fabricate sau dezvoltarea altora noi, ținând cont de cele mai recente progrese structurale și tehnologice. Dezvoltare mașini automate controlat magnetic și fotoelectric.
Reductoarele și arzătoarele sunt complet modernizate. Extinderea în continuare a Biroului de Construcții cu ateliere mecanice și electronice și o sală de prototipuri a permis dezvoltarea propriilor noastre modele de mașini de tăiat automate de dimensiuni mici. Perun rămâne un producător polonez de echipamente de sudare.
Deci gama de produse pe care le puteți fabrica este foarte largă. Fabricarea electrozilor poate fi o idee grozavă pentru a începe propria afacere. Pentru a organiza o astfel de producție este nevoie de un mini-atelier și de echipamente minime. În ciuda faptului că o astfel de afacere are o anumită specializare îngustă, este considerată foarte profitabilă și promițătoare. Electrozii de sudare au o cerere constantă, ceea ce se explică prin creșterea volumului de construcție a instalațiilor care utilizează structuri din beton armat. Acest produs și-a găsit aplicația în multe alte domenii în care este necesară sudarea elementelor metalice. Un avantaj suplimentar al acestui tip de afaceri constă în specificul mărfurilor produse: electrozii aparțin grupului de consumabile, astfel încât stocurile lor sunt reînnoite în mod regulat. Rentabilitatea ridicată și costurile de producție relativ scăzute cu rambursarea sa rapidă - toate acestea fac afacerea de producție electrozi de sudare atractiv pentru antreprenorii care tocmai aleg o direcție pentru munca lor.
Marca a apărut pe piață. O strategie bună de dezvoltare a companiei, încăpățânarea și norocul îi aduc un succes deplin. Se deschid noi oportunități de dezvoltare. Produce o gamă largă de electrozi de sudare în diverse aplicații, diametre și lungimi pentru a satisface așteptările clienților și pieței.
Acestea sunt selectate în funcție de cerințe detaliate. Fiecare furnizor este supus unor controale stricte de calitate. Înainte ca un anumit lot să ajungă la linia de producție, acesta este verificat și rezultatul este verificat cu atenție în raport cu specificațiile tehnologice ale produsului. Oțelul este obținut din fabrică de către furnizori certificați, iar procesul de verificare pentru fiecare dintre aceștia este foarte inteligent și necesită proceduri stricte. Doar o abordare atât de riguroasă garantează nivelul de calitate așteptat. În cazul oțelului, înainte de a intra în procesul de producție, acesta compoziție chimică verificat în fiecare caz.
Francize profitabile
Investiții de la 200.000 de ruble.
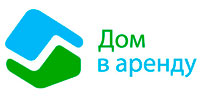
Pentru producția de electrozi pentru sudare, așa cum sa menționat mai sus, este necesară o linie specială. Procesul de fabricare a electrozilor de sudare cu ajutorul acestuia pare a fi destul de simplu. Sârma de oțel este folosită ca materie primă, care este derulată, îndreptată, tăiată în semifabricate egale cu lungimea electrozilor viitori. Majoritatea acestor operațiuni sunt efectuate automat. Muncitorul alimentează mașina doar cu bobina de sârmă. Apoi, semifabricatele tăiate din sârmă sunt curățate cu grijă cu șmirghel, drept urmare stratul superior de metal este îndepărtat de pe ele. După această procedură, firul capătă o suprafață aspră și curată, ceea ce asigură o bună aderență la materialul de acoperire. În etapa următoare, pe suprafața curățată a firului se aplică o soluție specială. Toate componentele din această soluție sunt în stare de pulbere: aceasta este singura modalitate de a evita apariția unor formațiuni neomogene pe electrozi și de a obține o aderență mai bună la suprafața metalică a tijei. Componenta principală a soluției este creta, care, împreună cu alți aditivi speciali, suferă măcinarea în două etape. În prima etapă, este pur și simplu zdrobită în bucăți destul de mari. Și măcinarea până la o stare de pulbere se efectuează deja în a doua etapă. Apoi masa zdrobită rezultată este cernută pe site pentru a separa particulele mari. Masa de acoperire poate fi aplicată pe tije în două moduri principale - prin scufundare (sau scufundare) și sertizare. Prima metodă este utilizată numai atunci când soluția de acoperire nu poate fi aplicată prin tehnologia de presare, deoarece este mai laborioasă și nu atât de economică și, prin urmare, mai scumpă. Când se utilizează tehnologia de scufundare, se prepară mai întâi o soluție. Pentru a face acest lucru, componentele uscate sunt amestecate cu un adeziv special, care se bazează pe sticlă lichidă. Semifabricatele de sârmă în poziție verticală sunt scufundate într-o baie cu o soluție și ținute în ea până când se formează un strat subțire de soluție pe suprafața firului. Electrozii sunt apoi scoși cu grijă din baie și lăsați să se usuce.
Procesul de pregătire în masă este complet automatizat. Acest lucru face posibilă garantarea unei compoziții chimice constante și, prin urmare, o bună calitate a acoperirii. Testarea și controlul strict, de la materia primă până la produsul final, oferă companiei asigurarea că electrozii care ajung la destinatar sunt de cea mai înaltă calitate.
Produsele sunt foarte populare. Pentru informații detaliate despre produse, vă rugăm să contactați reprezentanții noștri tehnici și de vânzări. Proprietățile electrodului copt pentru un anumit proces necesită utilizarea unei paste de electrozi personalizate în funcție de condițiile mediului de lucru.
În acest caz, consumul de soluție se dovedește a fi mare, iar productivitatea este semnificativ mai mică decât atunci când se folosește sertizarea. Dar presarea va necesita echipamente speciale - prese cu presiune ridicată până la 500-700 atmosfere. Soluția folosită în această metodă ar trebui să fie mai groasă și mai vâscoasă. Acest proces este complet automatizat: pentru a aplica pasta pe electrozi, piesele de prelucrat sunt plasate la un anumit interval de timp în cilindrul de presare. Acolo, tijele sunt împinse prin orificiile cilindrului cu o viteză de 300-500 de unități pe minut. La ieșire, acestea sunt deja acoperite cu un strat uniform de pastă de acoperire. Înainte de alimentarea benzii transportoare, unul dintre capetele electrodului de sudură este măcinat astfel încât să poată fi fixat în suport în timpul sudării.
Acest lucru este esențial pentru a asigura funcționarea cu succes. Atât temperaturile, cât și tensiunile termice pot fi calculate dinamic. Carl Wilhelm Söderberg a fost prima persoană care a avut ideea unui sistem de electrozi autonom, realizat din pastă pe bază de carbon. La acea vreme, industria folosea electrozi de grafit și precoapți scumpi și mai puțin disponibili. Astăzi, aproape 100 de ani mai târziu, este încă cel mai frecvent utilizat sistem de electrozi în cuptoarele cu arc submarin pentru feroaliaje, topire și topire a zgurii.
Pentru producerea electrozilor de sudare în volume industriale vor fi necesare echipamente speciale. Lista sa include instalația de măcinat și măcinat, dozatorul și mixerul de grăsime, presă de brichetare, presă de acoperire, mașină de curățat suprafața electrozilor, dispozitiv de marcat cu electrozi, cuptoare de uscare, mașină de îndreptat, echipamente automate pentru ambalarea produselor finite.
Când electrodul este epuizat în procesele cuptorului, pasta adăugată se topește și se coace într-un electrod solid și conductor de electricitate. Astfel, avem un electrod continuu care poate face munca de transfer de energie către vatra cuptorului, unde materia primă este încălzită suficient pentru a îndeplini temperaturile necesare procesului. Astfel de electrozi mari pot fi dificil de gestionat, iar electrozii mari sunt, de asemenea, mai pretențioși când vine vorba de pasta de electrozi folosită în electrozi. Având în vedere nevoia constantă de a îmbunătăți funcționarea cuptorului, acest lucru este necesar pentru un control îmbunătățit al electrozilor.
Acoperirea este un proces foarte responsabil, a cărui calitate determină posibilitatea de reglare a procesului de sudare și calitatea metalului depus. Stratul de pastă de pe firul electrodului este de la 1 la 1,6 mm. Acoperirea poate fi de până la 30% din greutatea totală a electrodului de sudare. Este format din mai multe elemente principale. Elementele din primul grup - care formează zgură - includ feldspatul, concentratul de titan, minereul de mangan etc. Ele protejează metalul lichid de expunerea la aer, prevenind reacțiile nedorite. Al doilea grup de componente sunt gazoase (diverse elemente organice, cum ar fi turba sau amidonul), care protejează metalul topit de efectele oxigenului și azotului. Compoziția acoperirii include și elemente dezoxidante (feromangan), care leagă oxigenul și îmbunătățesc metalul depus; componente de stabilizare (cretă), ajutând la ionizarea spațiului de arc; pulberi de oțel care măresc productivitatea sudării, permit economisirea feroaliajelor și a sârmei de electrod și îmbunătățesc performanța arcului și, în final, aditivii de aliere (grafit și diverse feroaliaje), care sunt incluși în metal sub formă de componente care îi îmbunătățesc proprietățile.
Până în prezent, dispozitivele și circuitele au fost fabricate în zone localizate ale fabricii din cauza distribuției limitate a materialului electronic organic. Aici, demonstrăm sinteza și aplicarea unui oligomer conjugat care poate fi livrat în fiecare parte a țesutului vascular al plantei și traversează venele în apoplastul frunzei.
Demonstrăm fire conductoare longitudinale și supercondensatori de-a lungul tijei. Am demonstrat recent unități cu funcționalitate electronică extinsă. Cu toate acestea, această funcționalitate electronică a fost realizată doar în regiuni localizate, în timp ce noile materiale electronice care ar putea fi distribuite în fiecare parte a fabricii ar oferi versatilitate în fabricarea dispozitivelor și circuitelor și ar crea oportunități pentru noi concepte de dispozitive. Structura plantei acționează ca un șablon fizic, în timp ce mecanismul de răspuns biochimic al plantei acționează ca un catalizator pentru polimerizare.
Francize profitabile
Electrozii de sudare de înaltă calitate se disting prin adâncimea necesară de fuziune (penetrare) a produselor sudate, conținutul scăzut de hidrogen în sudare, separarea bună a zgurii de sudură, stropirea ușoară a scânteilor, prezentarea bună a sudurii și prevenirea formarea de microfisuri în sudură.
Linia de producție de electrozi include o unitate de acoperire a electrozilor. Acesta, la rândul său, include unități precum un alimentator de bare, o presă electrică de acoperire și o mașină de curățat. Costul mediu al unei linii de producție de electrozi este de 1,5 milioane de ruble. Adăugați la această sumă costurile de transport și punerea în funcțiune (altul plus cel puțin 150-200 de mii de ruble). Doi oameni sunt suficienți pentru a lucra pe o astfel de linie. Încă un muncitor va fi necesar pentru ambalare. Costuri suplimentare - achiziționarea de materii prime pentru primul lot de mărfuri și ambalaje. Electrozi de sudura ambalati in cutii de cinci kilograme. Numărul de electrozi dintr-un pachet depinde de diametrul electrodului. Materiile prime și ambalajele vor costa încă 250 de mii de ruble. Costul mediu al electrozilor standard cu un diametru de 3 mm este de aproximativ 400 de ruble per pachet de 5 kg. Prin urmare, costul mediu pentru 1 kg de electrozi este de 80 de ruble. Prețul cu ridicata este de aproximativ 50-55 de ruble pe kilogram. Productivitatea liniei cu o sarcină medie este de 500 kg de produse pe zi, cu o sarcină completă - până la 800 kg pe zi. Rentabilitatea afacerii pentru producția de electrozi de sudare este de 27%. Pentru a crește profitabilitatea, este posibilă și organizarea în paralel a producției de cuie din resturi de sârmă rămase după tăierea semifabricatelor pentru electrozi de sudare. Pentru a face acest lucru, va trebui să achiziționați o mașină de fixat în cuie.
În plus, oligomerul poate traversa venele și poate intra în spațiul apopal din frunze. În cele din urmă, folosind arhitectura naturală a plantei, producem supercondensatori de-a lungul tulpinii. Rezultatele noastre sunt preludii la sistemele de putere de sine stătătoare integrate în instalații și distribuirea sistemelor interconectate de senzori și actuatori pentru a controla și optimiza instalațiile. În ciclul energetic global, plantele convertesc timpuriu energia primară de la soare în energie chimică.
De regulă, o astfel de producție funcționează în două schimburi. Profitul net al întreprinderii cu astfel de date va fi de peste 200 de mii de ruble pe lună.
Cu toate acestea, pentru a obține acest profit, este necesar nu numai să fabricați produse, ci și să le vindeți. Canalele de distribuție depind de volumele dumneavoastră de producție. Puteți vinde electrozi de sudură prin magazine individuale de construcții, lanțuri de retail, companii angro, piețe, companii și baze de construcții, structuri metalice etc. Cu cât volumele dvs. de producție sunt mai mari, cu atât transporturile dvs. ar trebui să fie mai mari. Lucrând în primul rând cu angrosisti, îți vei vinde produsele la prețuri mai mici decât dacă vinzi în cantități mici, dar în același timp vei economisi la ambalaje și vei putea crește volumele de producție. Concurența pe acest segment este estimată la mare. Dar dacă poți oferi partenerilor tăi produse de calitate la prețuri accesibile și, cel mai important, poți asigura livrări la timp și neîntrerupte, atunci nu vor fi probleme cu vânzările.
Pentru omenire, plantele sunt apreciate și ca sursă de căldură, substanțe chimice, fibre și materiale în vrac și sunt utilizate într-o gamă largă de aplicații de consum, sociale, tehnologice și industriale. În mod tradițional, silvicultură și agricultura folosesc cantități mari de îngrășăminte pentru a îmbunătăți creșterea plantelor, productivitatea și producția. Implementarea îngrășămintelor și a genelor de plante modificate în agricultură poate fi foarte restrictivă, deoarece substanțele chimice și speciile nedorite se pot „scurge” în – și pot polua – natură.
Francize profitabile
Mai exista o varianta de deschidere a unei astfel de productii cu investitii mult mai mici. Adevărat, profitul în acest caz va fi, de asemenea, semnificativ mai mic. Electrozii de sudare pot fi fabricați, de asemenea, folosind o tehnologie mai simplificată, fără utilizarea unor echipamente costisitoare. Acest lucru va necesita anumite materii prime: un fir cu un diametru de 3 mm (electrozii cu acest diametru sunt considerați cei mai populari), cretă zdrobită până la o stare de pulbere și sticlă lichidă. Secvența operațiilor este aproximativ aceeași ca și în cazul producției industriale: sârma este tăiată în bucăți de aproximativ 40 cm lungime fiecare, curățată până la strălucire pentru aderență cu o soluție de lubrifiant. Apoi creta este turnată într-un recipient, unde se toarnă apoi sticlă lichidă. Toată această masă este amestecată până la omogenizare și un semifabricat este coborât în ea. După un timp, piesa de prelucrat este suspendată până când umiditatea s-a evaporat complet. Un cuptor mic poate fi folosit pentru a accelera acest proces. În acest caz, timpul de uscare este redus de la câteva ore la 20-30 de minute. Desigur, aceasta este o versiune foarte simplificată, în care nu va fi posibilă producerea unor volume mari de produse într-un timp scurt. În plus, electrozii fabricați în acest mod manual sunt considerabil inferioare în calitate față de produsele realizate cu echipamente speciale. Pe de altă parte, dacă nu ai avut experiență anterioară în acest domeniu, nu ești sigur că o astfel de afacere va avea succes în regiunea ta, iar produsele sunt la cerere, atunci este logic să încerci mâna cu investiții minime, așa că că mai târziu, dacă experiența se dovedește a fi de succes, deschideți deja producția completă.
Instalațiile sunt mașini regenerabile, la scară largă și de înaltă performanță, care reprezintă o sursă neexploatată pentru producția de materiale avansate, electronice și tehnologii energetice. O strategie pentru dezvoltarea ulterioară a plantelor ca sisteme tehnologice și controlul dinamic al fiziologiei lor ar fi crearea unor sisteme electronice integrate care convertesc selectiv compușii chimici în semnale electrice și energie și invers, la rezoluție spațio-temporală mare.
Mulți sudori se întreabă: cum arată tehnologia de producție a electrozilor de sudare? Mulți oameni cred că un astfel de proces este destul de complicat, în timp ce alții invers. Deci, să vedem cum se întâmplă de fapt acest proces.
Tehnologie și echipamente pentru producția de electrozi
La producerea electrozilor se folosesc următoarele materiale: materiale pentru acoperirea electrodului, bulgăre de silicat și sârmă de sudură. Mai mult, bulgărea de sudare poate fi sodiu și potasiu. În plus, materiile prime sunt trimise la fabrică, unde sunt depozitate de muncitori în locuri special îndepărtate. La intrare este obligatoriu să se verifice calitatea materiilor prime, iar dacă materialul trece testul în mod normal, atunci primește permisiunea de utilizare la fabricarea electrozilor de sudură și un certificat. Dacă materia primă nu trece testul, atunci este trimisă la atelierul de producție. Apoi, treceți la acoperirea electrozilor. În producția de electrozi, toate componentele necesare sunt zdrobite în anumite părți, care vor depinde de scopul propus. Pentru a face acest lucru, este necesar să utilizați un concasor cu falci sau role, care asigură o separare de înaltă calitate și fiabilă a pieselor pentru acoperirea viitoare a electrodului de sudură.
Sistemele electronice integrate constau de obicei din contacte, fire, interconexiuni și componente. Din punct de vedere al circuitului, formarea tehnologiei celulelor cu biocombustibil sau a unui sistem de senzori și actuatori încorporați într-o plantă vie va necesita transferul sarcinii electronice pe distanțe mari și stocarea sarcinii la pierderi electrice reduse.
Folosind xileme și regiunile celulare și extracelulare din jur, am construit tranzistori electrochimici organici și circuite digitale simple. Proiectarea moleculară rațională a materialelor oferă o soluție la multe blocaje ale procesului, deoarece materialele pot fi făcute la comandă pentru a îndeplini cerințele specifice de aplicare sau criteriile de performanță. În cele din urmă, folosim proprietățile electrice și de încărcare ale firelor și electrozilor xilemer rezultați pentru a demonstra supercondensatorii de-a lungul tijei.
După finalizarea procesului de zdrobire, acestea sunt cernute printr-o sită care are funcție de vibrație. Apoi materiile prime sunt trimise la secția de dozare, unde se efectuează dozarea componentelor conform rețetei prescrise. Abia după aceea, amestecul finit intră în mixer.
În plus, producția de electrozi trece la fabricarea de tije. Pentru a face acest lucru, luați firul de sudură, care este verificat pentru deteriorări sau solicitări mecanice. fir de sudura livrat la atelier în bobine și trimis la o mașină de desfășurare, apoi are loc derularea și tăierea în bucățile necesare pe lungimea viitorului electrod. Apoi aceste piese sunt trimise la atelierul de acoperire, un bloc de silicat este zdrobit și încărcat într-o autoclavă, care este umplută cu apă. În momentul în care sticla este obținută dintr-un bloc de silicat, aceasta este trimisă într-un bazin special. Și deja din bazin sunt trimise la mixerul de sticlă lichidă. Dacă sticla finită îndeplinește toate cerințele, atunci este transportată într-un rezervor de alimentare, unde amestecul preparat de sticlă lichidă este amestecat. Abia după aceasta este presarea electrozilor sub presiune de la 300 la 650 kgf pe centimetru pătrat.
La două ore după ce trandafirul a fost scufundat în soluția de xilem, fasciculele vasculare expuse au fost mai închise la culoare, indicând începutul procesului de polimerizare. După 24 de ore de scufundare, trandafirul a fost îndepărtat și spălat cu apă. Conductivitatea ridicată a fost menținută chiar și pentru firele de centimetri, ceea ce indică faptul că o conductivitate semnificativă poate fi atinsă pe distanțe extinse de-a lungul firelor de xilem. Luate împreună, aceste interacțiuni au ca rezultat căi de percolare prin cristaliți care susțin conducerea.
Calculele teoretice sunt utilizate pentru a determina lungimea și starea de excitație a oligomerilor prin compararea proprietăților fotofizice calculate cu observațiile experimentale. Aceste tranziții se saturează către lungimi de undă mai mari la 481 nm pentru absorbția optică și 597 nm pentru emisie, pe măsură ce lungimea lanțului polimeric crește la dodecamer și mai departe.
Producția de electrozi după presare este verificată pentru calitate și defecte, iar aceștia încep curățarea capetelor. Electrozii sunt trimiși pentru etichetare și ambalare. Iar deșeurile generate ajung la procesarea și producerea următoarelor loturi.
De asemenea, producția de electrozi de tip grafit, pe care îi fac din cocs de petrol cu conținut scăzut de cenușă, și resturi de electrozi nu ocolește. Gudronul de cărbune este folosit ca element de legare. Materialele solide sunt mai întâi zdrobite, apoi calcinate, zdrobite, dispersate conform fracțiilor desemnate, dozate și amestecate cu lianți. Din masa electrodului rezultată, electrozii verzi sunt stoarși pe o presă orizontală puternică, care sunt uscați, arși și supuși prelucrarii și grafitizării. Grafitizarea se efectuează la o temperatură de 2900 timp de 100 de ore și nu numai electrozii sunt utilizați ca încălzitor, ci și umplere cu carbon. În urma unei astfel de operații, se realizează structura cristalină a grafitului, impuritatea se evaporă și se restabilește. Rezistența electrică și duritatea scade și ele. În ceea ce privește nivelul ridicat de intensitate energetică, acesta este considerat primul motiv al prețului ridicat al electrozilor.
În plus, observăm semnale de protoni între 8 și 9 ppm din regiunea aromatică, indicând situsuri de protoni labile care susțin reacția de polimerizare prin reducerea conținutului de oxigen al xilemului plantei. Acest rezultat indică faptul că planta eliberează una sau mai multe substanțe chimice care catalizează polimerizarea, crescând viteza de reacție dincolo de ceea ce este stimulat de oxidarea aerului. Polimerizarea îmbunătățită poate fi observată și de-a lungul secțiunilor de țesut vegetal localizate în jurul cortexului și țesutului vascular al floemului.
Video detaliat despre producție - cum se face:
Și, de asemenea, cum arată o producție mică în China:
Pentru a reduce consumul de electrozi, aceștia sunt impregnați cu diverse substanțe pentru a oferi protecție împotriva manifestării oxidării. Consumul total de electrozi este format din următoarele afișaje: pulverizare în arc - 15 - 25; fragmente și cenușă - 10-20% și oxidare la suprafață - 55 -75. Dacă debitul ajunge la 70 la sută și este dat în momentul topirii sarcinii solide și a timpului de rupere, atunci pentru a reduce oxidarea electrozilor trebuie luați în considerare următorii factori.
Va trebui să asigurați etanșeitatea cuptorului, cel mai adesea în punctele de intrare prin acoperiș, să utilizați un strat de protecție, să îmbunătățiți calitatea electrodului, să reduceți lungimea părții încălzite datorită locației acceptabile a acoperișului cuptorului. . Și, de asemenea, limitați temperatura suprafeței electrozilor în limite acceptabile.
Dacă în producția de electrozi se folosesc cuptoare cu arc de rezistență, atunci este posibil să se utilizeze electrozi de cupru cu vârfuri de grafit.