Как сваривать ровным углом детали сваркой. Технология ручной дуговой сварки Ч.3 Техника ручной дуговой сварки
Ни для кого не секрет, что во время сварки металла выполняется движение электродов. Эти движения зачастую называют колебательными . Существует множество технологических подходов к выполнению сварочных работ металла. Электроду в процессе сварки, независимо от применяемого способа, сообщается движение в трёх разных направлениях .
Первое движение называют поступательным, при котором движение идёт по оси электрода. Зависимо от скорости плавления , поступательное движение поддерживает постоянную длину дуги , которая не должна выходить за пределы 0.5-1.2 диаметра электрода. Длина дуги зависит от марки электрода и условий сварки. Формирование шва ухудшается при уменьшении длины дуги, а также возникает вероятность короткого замыкания (сокращенно КЗ). Увеличение же дуги является причиной повышения разбрызгивания металла электрода и снижения качества сварного шва по форме и его свойствам (механическим).
Вторым движением является смещение электрода вдоль оси с целью образования шва. Диаметр электрода, сила тока(постоянным или переменным) и скорость плавления электрода определяют скорость движения электрода. В случае отсутствия поперечных смещений электрода, шов получается узкий (ниточный), ширина которого равна приблизительно 1.5 диаметра применяемого электрода. Данный шов используют при сварке тонких металлических листов.
Последним движением является смещение электрода поперек для корректировки ширины шва и глубины плавления металла. Данные колебательные движения предполагают высокую квалификацию сварщика и его навыков, а также определяются характеристиками свариваемого материала, положением и размером шва. Ширина шва, при использовании поперечных колебательных движений варьируется в пределах 1.5-5 диаметра используемого электрода.
Грамотное и технически правильное перемещение электрода – главная задача и условие для получения качественного шва при выполнении сварочных работ. Важна определённая методика выполнения колебательных движений электрода, а также рациональность его перемещения. Для выполнения качественного шва существует несколько общих способов , применяемых в любых ситуациях, с помощью которых сварщик выполняет движения во время сварки . Это движения «ёлочкой» (а), углом (б), «движение по спирали» (в), «движение полумесяцем» (г). Рис.1
При сварке вертикального углового сварочного шва наиболее удобно показать все способы колебательных движений электрода , к тому же это очень часто применяемая операция в сварке изделий из проката. При этом мы опустим все вопросы, связанные с разделкой кромок и подготовкой поверхностей перед сваркой.
С применением колебательных движений электрода полумесяцем или по спирали, изначально наплавляют электродом полочку на кромки, а после мелкими порциями без пропусков и разрывов наплавляют металл, рекомендуется выполнять сварку непрерывно. Дальнейшая сварка металла производится постепенно со смещением электрода выше, за собой оставляя, готовый сварочный шов. Другая схема колебательного движения при сварке – углом, предусматривает колебательные движения электрода с применением попеременного смещения вверх-вниз, без разрывов наплавливают на кромки металл с равномерным перемещением электрода вверх.
Методика «ёлочкой » характеризуется движением электрода вверх, затем вправо , после этого по короткой траектории спускают вниз влево. Желательно чтобы капля металла застывала при каждом отдельном этапе сварки между кромками. После, ушедший электрод двигают вверх влево и опять спускают из точки подъёма, но теперь вниз вправо. Такими постепенными движениями с непрерывными отдельными порциями, и выполняется шов сварки.
Правильное поддержание дуги и ее перемещение является залогом качественной сварки. Слишком длинная дуга способствует окислению и азотированию расплавленного металла, разбрызгивает его капли и создает пористую структуру шва. Красивый, ровный и качественный шов получается при правильном выборе дуги и равномерном ее перемещении, которое может происходить в трех основных направлениях.
Поступательное движение сварочной дуги происходит по оси электрода. При помощи этого движения поддерживается необходимая длина дуги, которая зависит от скорости плавления электрода. По мере плавления электрода, его длина уменьшается, а расстояние между электродом и сварочной ванной - увеличивается. Для того чтобы это не происходило, электрод следует продвинуть вдоль оси, поддерживая постоянную дугу. Очень важно при этом поддерживать синхронность. То есть, электрод продвигается в сторону сварочной ванны синхронно с его укорочением.
Продольное перемещение электрода вдоль оси свариваемого шва формирует так называемый ниточный сварочный валик, толщина которого зависит от толщины электрода и скорости его перемещения. Обычно ширина ниточного сварочного валика бывает на 2 - 3 мм больше диаметра электрода. Собственно говоря, это уже есть сварочный шов, только узкий. Для прочного сварочного соединения этого шва бывает недостаточно. И поэтому по мере перемещения электрода вдоль оси сварочного шва выполняют третье движение, направленное поперек сварочного шва.
Поперечное движение электрода позволяет получить необходимую ширину шва. Его совершают колебательными движениями возвратно-поступательного характера. Ширина поперечных колебаний электрода определяется в каждом случае индивидуально и во многом зависит от свойств свариваемых материалов, размера и положения шва, формы разделки и требований, предъявляемых к сварному соединению. Обычно ширина шва лежит в пределах 1,5 - 5,0 диаметров электрода.
Таким образом все три движения накладываются друг на друга, создавая сложную траекторию перемещения электрода. Практически каждый опытный мастер имеет свои навыки в выборе траектории перемещения электрода, выписывая его концом замысловатые фигуры. Классические траектории движения электрода при ручной дуговой сварке приведены на рис. 1. Но в любом случае траекторию перемещения дуги следует выбирать таким образом, чтобы кромки свариваемых деталей проплавлялись с образованием требуемого количества наплавленного металла и заданной формы шва.
Если шов не будет закончен до того, как длина электрода уменьшится настолько, что требуется его замена, то сварку на время прекращают. После замены электрода следует удалить шлак и возобновить сварку. Для завершения оборванного шва зажигают дугу на расстоянии 12 мм от углубления, образовавшегося на конце шва, называемого кратером. Электрод возвращают к кратеру, чтобы образовать сплав старого и нового электродов, а затем снова начинают перемещать электрод по первоначально выбранной траектории.
![]() |
|
![]() |
![]() |
![]() |
![]() |
![]() |
![]() |
![]() |
![]() |
Схема дуговой сварки
Порядок заполнения шва по сечению и длине определяет способность сварного соединения воспринимать заданные нагрузки, влияет на величину внутренних напряжений и деформаций в массиве шва.
Швы различают: короткие - длина которых не превышает 300 мм, средние - длиной 300 - 100 мм и длинные - свыше 1000 мм. В зависимости от длины шва его заполнение может выполняться по различным схемам сварочного заполнения, которые представлены на рис. 2.
При этом короткие швы заполняют за один проход - от начала шва до его конца. Швы средней длины могут заполняться обратноступенчатым методом или от середины к концам. Для выполнения обратноступенчатого метода заполнения шов разбивают на участки длина которых равна 100 -300 мм. На каждом из этих участков заполнение шва выполняют в направлении, обратном общему направлению сварки.
Если для нормального заполнения шва одного прохода сварочной дуги мало, накладывают многослойные швы. При этом, если число накладываемых слоев равно числу проходов, шов называют многослойным. Если же некоторые слои выполняют за несколько проходов, такие швы называют многослойно-проходными. Схематически такие швы отражены на рис. 3.
С точки зрения производительности труда наиболее целесообразными являются однопроходные швы, которым отдают предпочтение при сварке металлов небольших (до 8-10 мм) толщин с предварительной разделкой кромок.
Но для ответственных конструкций (сосуды, работающие под давлением, несущие конструкции и т.д.) этого бывает мало. Внутренние напряжения, возникающие в процессе сварки, могут вызвать появление трещин в шве или в околошовной зоне из-за недостаточной пластичности шва и большой жесткости основного металла. При сварке изделий с относительно небольшой жесткостью внутренние напряжения вызывают местное или общее коробление (деформации) свариваемой конструкции. Кроме того, при сварке металлов толщиной более 10 мм. появляются объемные напряжения и возрастает опасность появления трещин. В таких случаях принимают целый ряд мер, позволяющих уменьшить напряжения и деформации: применяют сварные швы минимального сечения, сварку многослойными швами, наложение швов «каскадными методами» или «горкой», принудительное охлаждение или подогрев.
При сварке «горкой» сначала у основания разделанных кромок прокладывают первый слой, длина которого должна быть не более 200 - 300 мм. После этого первый слой перекрывают вторым, длина которого на 200 - 300 мм больше первого. Точно так же накладывают третий слой, перекрывая второй на 200 - 300 мм. Таким образом продолжают заполнение до тех пор, пока количество слоев в зоне первого шва не окажется достаточным для заполнения. Следующий слой накладывают в месте окончания первого слоя, перекрывая последний (если позволяет длина шва) на те же 200 - 300 мм. Если первый шов прокладывался не в начале шва, а в его средней части, то горку формируют последовательно в обоих направлениях (рис.2,е). Так, формируя горку, последовательно заполняют весь шов. Преимущество данного метода состоит в том, что зона сварки все время находится в подогретом состоянии, что способствует улучшению физико-механических качеств шва, так как внутренние напряжения получаются минимальными и предупреждается появление трещин.
«Каскадный метод» заполнения шва по существу является той же «горкой», но выполняют его в несколько другой последовательности. Для этого детали соединяют между собой «на прихватках» или в специальных приспособлениях. Прокладывают первый слой, а затем, отступив от первого слоя на расстояние 200 - 300 мм, прокладывают второй слой, захватывая зону первого (рис.2,д). Продолжая в той же последовательности, заполняют весь шов.
Угловые швы (рис. 4) можно выполнять двумя методами, каждый из которых имеет свои преимущества и свои недостатки. При сварке «в угол» допускается больший зазор между деталями (до 3 мм), проще сборка, но техника сварки сложнее. Кроме того, возможны подрезы и наплывы, снижается производительность из-за необходимости за один проход сваривать швы небольшого сечения, катет которых меньше 8 мм. Сварка «в лодочку» допускает большие катеты шва за один проход и поэтому более производительна. Однако такая сварка требует тщательной сборки.
Указанные приемы дуговой сварки рассматривались на нижних положениях шва, выполнение которых наименее трудоемко. На практике часто приходится выполнять горизонтальные швы на вертикальной плоскости, вертикальную и потолочную сварку. Для выполнения этих работ используются те же приемы, что и для швов с нижним положением, но трудоемкость работ и некоторые технологические особенности требуют более детального подхода и изменения некоторых методов.
При сварке таких швов появляется вероятность вытекания расплавленного металла, что приводит к падению капель к незаполненным сваркой местам, потекам расплавленного металла по горизонтальным плоскостям и т.д
Рассматривая суть процессов, происходящих в подобных швах, мы говорили, что удерживать металл в расплавленной ванне могут силы поверхностного натяжения. Для того чтобы эти силы были достаточными, сварщик должен владеть приемами сварки виртуозно. Здесь приходится понижать сварочный ток и применять электроды пониженного сечения. Это в конечном итоге сказывается на производительности, так как приходится увеличивать количество сварочных проходов. Поэтому на практике стараются в дополнение к силам поверхностного натяжения добавить «пленку поверхностного натяжения». Суть данного метода заключается в том, что дугу держат не постоянно, а с определенными промежутками, то есть импульсами.
Для этого дугу постоянно прерывают, зажигая ее с определенными промежутками времени, давая возможность расплавленному металлу частично закристаллизоваться. Именно здесь и проявляется умение сварщика выбрать такие интервалы, когда не успевает образоваться сварочный катет и одновременно металл потерял бы часть своей текучести.
Потолочный шов является самым сложным. Поэтому проводить его непрерывным горением дуги - дело бесперспективное. Сварку выполняют короткими во времени замыканиями дуги на сварочную ванну так, чтобы она не успела остыть, пополняя ее новыми порциями расплавленного металла.
При сварке данным методом следует следить за размером дуги, так как ее удлинение может вызвать нежелательные подрезы. Кроме того, при сварке таких швов создаются неблагоприятные условия для выделения шлаков из расплавленного металла, что может привести к пористости сварного шва.
Вертикальные швы можно варить в двух направлениях - снизу вверх и сверху вниз. И тот и другой метод имеет право на существование, но всегда предпочтительнее сварка на подъем. В этом случае расположенный снизу металл удерживает сварочную ванну, не давая ей растекаться.
При сварке на спуск труднее удерживать сварочную ванну, и поэтому добиться качественного шва гораздо сложнее. Суть такого метода практически не отличается от потолочной сварки, и применяют его тогда, когда сварка на подъем технологически невозможна.
Горизонтальные швы на вертикальной плоскости тоже имеют свои особенности. В данных швах особую сложность представляет удержание сварочной ванны у обеих кромок свариваемых деталей. Для того чтобы облегчить этот процесс, скос нижней кромки не выполняют. В таком случае получается полочка, которая способствует удержанию на месте расплавленной сварочной ванны. Уместен здесь и прием импульсной сварки с кратковременным зажиганием дуги, как и для потолочных швов.
Удаление сварочных шлаков выполняют обрубочным молотком. Для этого, подождав, пока заготовка остынет настолько, что ее можно брать рукой, прижимают крепко к столу и ударами молотка, направленными вдоль шва, удаляют шлак, покрывающий сварочный шов. После этого шов проковывают для снятия внутренних напряжений. Для этого боек молотка разворачивают вдоль шва и выполняют проковку по всей его длине.Завершают очистку жесткой проволочной щеткой, перемещая ее резкими движениями сначала вдоль шва, а потом - поперек, чтобы удалить последние остатки шлака.
![]() |
![]() |
Рис. 6. : При сварке на подъем наблюдается большая глубина проплавления, а также большая высота валика. При сварке на спуск наоборот снижается глубина проплавления и уменьшается высота сварного шва. При этом ширина шва практически не меняется. | Рис. 7. : На рисунке видно, что при сварке углом назад более глубокое проплавление, а при сварке углом вперед увеличивается ширина шва и уменьшается высота валика. |
![]() |
![]() |
Рис. 8. : Положение сварочной ванны при наклонах изделия, дуги или электрода. Сварка на спуск, сварка на подъем, сварка углом вперед. | Рис. 9. Влияние подготовки кромок под сварки при стыковом соединении. |
![]() |
![]() |
Рис. 10. : B - ширина сварного шва; K - катет шва | Рис. 11. : Если при сварке изменять сварочный ток то будут меняться параметры сечения шва. При более низком токе увеличивается глубина проплавления и увеличивается валик сварного шва. |
Техника манипулирования электродом.
Во время сварки электросварщик сообщает концу электрода движение в трех направлениях.
Первое движение
- поступательное, по направлению оси электрода для поддержания необходимой длины дуги l
д, которая должна быть l
д = (0,5 + 1,1)d
э, где d
э - диаметр электрода, мм
.
Длина дуги оказывает большое влияние на качество сварного шва и его форму. Длинной дуге соответствует интенсивное окисление и азотирование расплавленного металла и повышенное его разбрызгивание. При сварке электродами фтористо-кальциевого типа увеличение длины дуги приводит к пористости металла шва.
Второе движение
- вдоль оси валика, для образования сварного шва. Скорость движения электрода зависит от величины тока, диаметра электрода, типа и пространственного положения шва. Правильно выбранная скорость перемещения электрода вдоль оси шва обеспечивает требуемую форму и качество сварного шва. При большой скорости перемещения электрода основной металл не успевает проплавиться, вследствие чего образуется недостаточная глубина проплавления - непровар. Недостаточная скорость перемещения электрода приводит к перегреву и прожогу (сквозное проплавление) металла, а также снижает качество и производительность сварки. Правильно выбранная скорость продольного движения электрода вдоль оси шва позволяет получить его ширину на 2 - 3 мм
больше, чем диаметр электрода.
Сварной шов, образованный в результате первого и второго движений электрода, называют ниточным. Его применяют при сварке металла небольшой толщины, при наплавочных работах и при подварке подрезов.
Третье движение
- колебание концом электрода поперек шва, для образования уширенного валика, который применяется чаще, чем ниточный. Для образования уширенного валика электроду сообщают поперечные колебательные движения, чаще всего с постоянной частотой и амплитудой, совмещенные с поступательным движением электрода вдоль оси шва и оси электрода. Поперечные колебательные движения электрода разнообразны и определяются формой, размерами, положениями шва в пространстве и навыком сварщика. На рис. 40 показаны поперечные колебания, описываемые концом электрода.
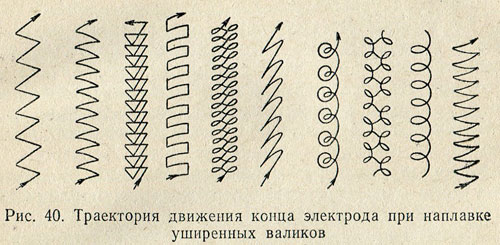
В процессе колебания электрода середину пути проходят быстро, задерживая электрод по краям. Такое изменение скорости колебания электрода обеспечивает лучший провар по краям. Одинаковая ширина валика достигается одинаковыми поперечными колебаниями. Ширина валика при сварке не должна быть более 2 - 3 диаметров электрода.
Обычно сварку выполняют вертикально расположенным электродом или при его наклоне относительно шва, углом вперед или назад (рис. 41).
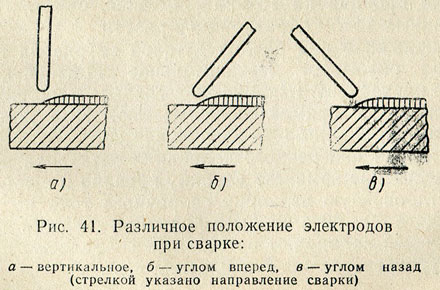
При сварке углом вперед или назад обеспечивается более полный провар и меньшая ширина шва. Углом назад сваривают нахлесточные, угловые и тавровые соединения, а высококвалифицированные сварщики сваривают и стыковые соединения.
Понятие о режиме сварки.
Под режимом сварки понимают совокупность условий протекания процесса сварки. Параметры режима сварки подразделяют на основные и дополнительные. К основным параметрам
режима сварки при ручной сварке относят величину, род и полярность тока, диаметр электрода, напряжение, скорость сварки и величину поперечного колебания конца электрода, а к дополнительным
- величину вылета электрода, состав и толщину покрытия электрода, начальную температуру основного металла, положение электрода в пространстве (вертикальное, наклонное) и положение изделия в процессе сварки.
Глубина провара и ширина шва зависят от всех основных параметров режима сварки.
Увеличение сварочного тока вызывает при неизменной скорости рост глубины проплавления (провара). Это объясняется изменением величины погонной энергии (тепла, приходящегося на единицу длины шва) и частично изменением давления, оказываемого столбом дуги на поверхность сварочной ванны.
Род и полярность тока также влияют на форму и размеры шва. При сварке постоянным током обратной полярности глубина провара на 40 - 50% больше, чем при сварке постоянным током прямой полярности, что объясняется различным количеством теплоты, выделяющейся на аноде и катоде. При сварке переменным током глубина провара на 15 - 20% меньше, чем при сварке постоянным током обратной полярности.
Напряжение при ручной дуговой сварке на глубину провара оказывает незначительное влияние, которым можно пренебречь. Ширина шва связана с напряжением на электродах прямой зависимостью. При увеличении напряжения ширина шва увеличивается.
Величина поперечного колебания электрода позволяет существенно изменять глубину провара и ширину шва. Ориентировочную величину сварочного тока подбирают из расчета 40 - 60 а
на 1 мм
диаметра стержня электрода, который подбирают по толщине свариваемого металла и пространственного положения шва.
Для металла толщиной 2 мм
диаметр электрода должен составлять 2 - 3 мм
, для металла тощиной 8 мм
он должен быть 4 - 5 мм
. Сварку в вертикальном и потолочном положениях целесообразно вести электродами меньших диаметров (до 4 мм
), так как в этом случае легче предупредить стекание вниз металла сварочной ванны (объем сварочной ванны будет меньше).
Способы сварки швов различной протяженности.
Все швы по протяженности разделяют на три группы: от 250 до 300 мм
- короткие швы; от 300 до 1000 мм
- швы средней длины; от 1000 мм
и более - длинные швы. Короткие швы сваривают от начала к концу шва в одном направлении (рис. 42).
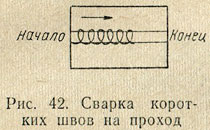
Средние швы сваривают участками (рис. 43 и 44).
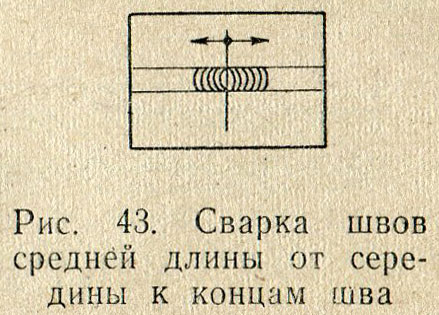
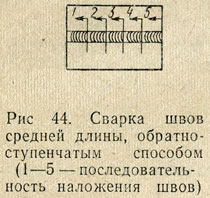
Длину участка выбирают такой, чтобы его можно было сварить целым числом электродов (двумя, тремя и т.д.). Сварку участков начинают в центре шва и ведут от середины к концам или обратноступенчатым способом от одного края к другому.
Длинные швы, широко применяемые в резервуаростроении, судостроении и при изготовлении различных емкостей, чаще всего сваривают вразбивку, обратноступенчатым способом (рис. 45).
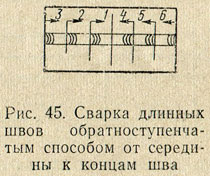
Сварка металла большой толщины. Многослойные швы рекомендуется сваривать методом «горки» или каскадным методом. При сварке «горкой» (рис. 46) на участке длиной 200 - 300 мм накладывают первый слой.
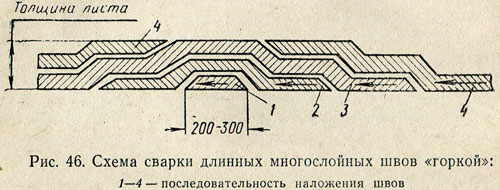
Затем после очистки первого слоя от шлака, окалины и брызг на него накладывают второй слой, по длине в два раза больший, чем первый. Наконец, отступив от начала второго слоя на 200 - 300 мм
, выполняют третий слой. Таким образом выполняют сварку (заполнение разделки) в обе стороны от центральной «горки» короткими швами.
Каскадный метод (рис. 47), являющийся разновидностью сварки «горкой», применяют при сварке листов толщиной более 20 - 25 мм
.
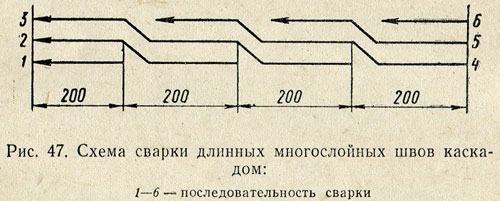
Техника сварки стыковых, тавровых и угловых швов.
Сварку стыковых соединений выполняют с одной или с двух сторон. Для борьбы с прожогами применяют остающиеся или съемные подкладки. Остающиеся подкладки изготовляют из стальных полос толщиной 2 - 4 мм
при ширине 30 - 40 мм
. Съемные подкладки изготовляют из материала, который во время сварки не плавится, т.е. обладает хорошей теплопроводностью и теплоемкостью. Этим требованиям отвечает медь. Съемные подкладки в процессе сварки иногда охлаждают проточной водой. Съемные подкладки можно изготовить также из керамики или графита. Сварка на подкладках имеет следующие преимущества:
сварщик работает более уверенно, не боится прожогов и натеков и может увеличить сварочный ток на 20 - 30%;
исключается необходимость подварки корня шва обратной стороны.
При сварке стыковых соединений с V-образной разделкой кромок в зависимости от толщины свариваемых листов (от 3 до 26 мм
), положения шва в пространстве, диаметра электрода - сварку выполняют в два и более слоев. Выполнение шва начинают со сварки первого слоя, состоящего из одного валика. Дугу возбуждают на краю скоса кромки, а затем, переместив ее к нижней части шва, проваривают края скосов кромок (корень шва). На скосах кромок движение электрода замедляют, чтобы улучшить их провар, а при переходе конца электрода с одной кромки на другую скорость его движения увеличивают для того, чтобы избежать прожога притуплённых кромок.
При сварке первого слоя применяют электроды диаметром 2, 3 или 4 мм
. Электроды большего диаметра не обеспечивают надежный провар корня шва. Перед наложением следующего слоя поверхность предыдущего зачищают от шлака и брызг. Образование шва заканчивают наплавкой усиления высотой 2 - 3 мм
над поверхностью основного металла. После заполнения всего сечения шва со стороны разделки кромок с приданием ему требуемого усиления изделие поворачивают, а затем пневматическим зубилом или воздушно-дуговой строжкой вырубают или выплавляют в корне шва канавку шириной 8 - 10 мм
и глубиной 3 - 4 мм
, которую заваривает за один проход контрольным швом (придавая ему небольшое усиление).
Сварка угловых, тавровых и нахлесточных соединений бывает однослойной и многослойной (однослойная применяется для швов с катетом до 10 мм
). Угловые, тавровые и нахлесточные соединения можно сваривать и без колебаний электрода ниточным и уширенным валиком. Колебания концом электрода производят тогда, когда необходимо наложить шов с большим катетом. При сварке таких сварных соединений возможно образованне непровара в одной из сторон, а также непровар угла и подрез верхней и нижней кромок. Лучше всего сварку угловых, тавровых и нахлесточных соединений вести в положении «в лодочку» (рис. 48,а). При сварке в угол (рис. 48,6) или с оплавлением верхней кромки (рис. 48, в) процесс сварки целесообразнее вести наклонным электродом (углом назад).
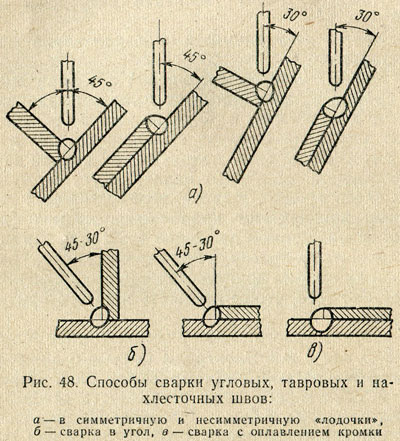
Особенности сварки вертикальных, горизонтальных и потолочных швов. Вертикальные швы сваривают двумя способами: снизу вверх и сверху вниз. При сварке снизу вверх (рис. 49, а) дугу возбуждают в нижней точке шва и после образования ванночки расплавленного металла электрод отводят немного вверх и в сторону. Дуга при этом должна быть направлена на основной металл. Расплавленный металл при отводе электрода вверх затвердевает, образуя подобие полочки, на которую наплавляют и которая удерживает последующие капли металла при движении электрода вверх. Электрод рекомендуется наклонять вверх под углом 45 - 50° к горизонту.
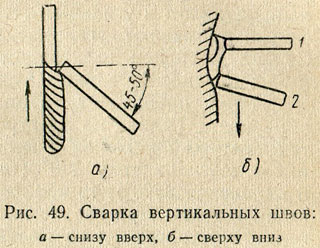
При сварке сверху вниз (рис. 49,6) дугу возбуждают в верхней точке шва и придают электроду сначала перпендикулярное положение 1
, а после образования кратера - наклонное положение 2
. Метод сварки сверху вниз рекомендуется применять в основном лишь для тонкого металла и первых слоев при V - и Х - образной разделке кромок. Сварку вертикальных швов выполнять значительно труднее, чем нижних, так как в первом случае расплавленный металл под действием силы тяжести стремится вытечь из сварочной ванны. Вертикальные швы следует сваривать током, на 10 - 15% меньшим, чем при сварке швов в нижнем положении, и короткой дугой; используемые для вертикальных швов электроды должны иметь «короткие» шлаки.
При сварке стыковых горизонтальных соединений подготовка кромок необходима только для верхней кромки. Дугу возбуждают вначале на нижней горизонтальной кромке, а затем перемещают на скошенную кромку.
Потолочные швы являются наиболее трудными для выполнения, так как расплавленный металл всегда стремится вытечь из сварочной ванны вниз. Незастывший металл удерживается в сварочной ванне силами поверхностного натяжения и давлением дуги. Объем сварочной ванны должен быть минимальным, поэтому сварка возможна только при короткой дуге. Ток должен быть на 15 - 20% меньше, чем при сварке в нижнем положении. Потолочную сварку выполняют сварщики - потолочники, прошедшие специальную подготовку.
Вопросы для самопроверки
1. Какие условия требуются для получения высокого качества сварного шва?
2. Какими параметрами задается режим сварки?
3. Как свариваются швы различной протяженности и толщины?
". Правильная техника сварки является гарантией получения качественного сварного соединения. Правильная техника приходит с опытом работы и определяет квалификацию сварщика.
Электрическая дуга при ручной дуговой сварке
Возбуждение сварочной дуги
Возбуждение дуги может происходить двумя способами. Можно прикоснуться электродом к свариваемому металлу, а потом отвести электрод на расстояние 3-4мм, поддерживая горение образовавшейся дуги.
Можно зажечь дугу, быстрым боковым движением прикоснувшись к свариваемому металлу и затем отвести электрод на расстояние также 3-4мм (это движение подобно тому, как зажигается спичка). Прикосновение электрода к металлу должно быть кратковременным, иначе электрод приваривается к металлу. Отрывать приварившийся электрод следует, резкими движениями поворачивая его в стороны.
Длина электрической дуги
Техника сварки горкой состоит в том, что в середине завариваемого участка на небольшой длине (200-300мм) выполняют сварной шов. Затем накладывают второй шов, который больше первого по длине примерно в два раза. Второй шов должен с двух сторон перекрывать первый шов (схема е) на рисунке). Третий слой, по длине на 200-300мм больше второго и также его перекрывает с двух сторон.
Таким образом, продолжают накладывать новые швы, длиннее предыдущих на 200-300мм и перекрывающих их с обеих сторон до тех пор, пока участок над самым первым швом не будет полностью заварен. После этого сварку выполняют в разные стороны короткими швами. Преимущество данной техники ручной дуговой сварки состоит в том, что зона сварки всегда находится в горячем состоянии и это значительно снижает риск возникновения трещин. каскадом выполняется по аналогичному принципу (схема д)).
В случае сварки низкоуглеродистой стали, каждый слой наплавленного металла имеет толщину 3-5мм, в зависимости от силы сварочного тока. К примеру, при силе сварочного тока 100А, происходит расплавление основного металла на глубину 1мм, а в металле нижнего слоя происходят термические изменения на глубине 1-2мм с формированием мелкозернистой структуры.
При увеличении силы тока до 200А, проплавление металла происходит на глубину до 4мм, а термические превращения в нижних слоях металла происходят на глубине 2-3мм.
Для получения мелкозернистой структуры в корневом шве выполняют его термическую обработку. Для этого выполняют подварочный шов по всей длине соединения напроход электродом, диаметром 3мм при силе сварочного тока 100А. Перед выполнением подварочного шва, корень основного шва зачищают.
Для проведения термической обработки верхних слоёв шва, наносится отжигающий слой, толщина которого составляет 1-2мм. За счёт малой толщины шва достигается большая скорость остывания и мелкозернистая структура. Отжигающий слой наносят электродом диаметром 5мм при силе сварочного тока 200-300А.
Техника окончания шва при ручной дуговой сварки
При окончании выполнения сварного шва, необходимо правильно заварить кратер. Кратер содержит наибольшее количество вредных примесей и является зоной повышенного риска для образования трещин. Учитывая это, не рекомендуется сразу обрывать дугу, быстро отведя электрод в сторону. Лучше всего прекратить движения электрода и медленно удлинять дугу, до её обрыва. При такой технике сварки, электродный металл заполняет кратер.
При сварке низкоуглеродистых сталей возможно отведение кратера в сторону от сварного шва. Но, в случае сварки стали, склонной к формированию закалочных структур, вывод кратера в сторону не допустим из-за повышенной вероятности образования трещин. Если произошёл случайный обрыв дуги, или необходимо сменить электрод, то продолжать процесс сварки следует, возбуждая дугу не над кратером, а перед ним, на ещё не сваренном основном металле. Затем проплавляют металл в кратере и продолжают процесс сварки.
- Угол расположения электрода при сваривании
- Нижнее расположение
- Вертикальное расположение
- Горизонтальное расположение
- Потолочное расположение
Человек, у которого появилось желание научиться сварочному делу, зачастую сталкивается с вопросом о том, какое положение при сварке выбрать. Ведь в зависимости от того, какое было выбрано положение и угол наклона электрода, определяется качество и надежность проделанной работы. Учитывая это, каждый нынешний сварщик-специалист наверняка когда-то задавался этим вопросом.
Сварка – это процесс, который позволяет создавать неразрывные соединения между несколькими элементами.
Сварка – это процесс образования неразъемного соединения с непрерывной структурой (т. е. создание единого цельного металла). Основным источником нагрева металла является сварочная дуга.
Дуга – это длительный устойчивый электрический разряд между двумя электродами в газовой среде, находящимися под напряжением.
Угол расположения электрода при сваривании
Угол наклона и положение электрода при сварке определяют, как быстро металл будет прогреваться. В основном электрод держится под углом в 45-90° к горизонтали. А самым удобным большинство сварщиков считают угол в 75°.
Оптимальное решение в подборе угла наклона основывается на выборе шва, который планируется для изготовления. Чем больше угловая вертикаль, тем глубже будет плавление металла, а шов гораздо меньше будет выпирать. Это происходит из-за того, что дуга производит давление на металлическую ванну и дает ей растекаться по краям. Находясь под наклоном, электрод с помощью силы дуги приподнимает шов и делает его более выпуклым.
Для качественного выполнения работ применяется короткая дуга. Если электрод выставлен перпендикулярно, металлическая ванна образовывается и растекается довольно быстро. Чтобы уменьшить провар на тонкой пластине, кладется ограниченное количество металла для малого шва. Если электрод держать под наклоном, тепло будет уходить из металлоконструкции и позволит уменьшить скорость электросварки для формирования швов. А если его наклон слишком большой, сварочный материал не прогреется, ванна будет узкая, а шов будет выпирать, и вы потеряете управление по краям. Для большинства подогнанных стыковых частей можно поддерживать постоянный угол наклона, чтобы получался плотный шов. Однако в некоторых ситуациях необходимо будет менять положение электрода при сваривании. Чтобы заполнить зазоры, можно будет сделать уклон более сильным, замедляя перенос металла и удерживая размер шва. Потом поднять электрод, чтобы закончить шов. Чтобы сохранять правильное расположение угла, требуется практика. При электросварочных работах нужно поддерживать свободное и расслабленное состояние.
Конструкция, которую планируют соединить методом сваривания, имеет свойство располагаться в разных плоскостях – это зависит от технологических требований выполнения данных работ. От их расположения в пространстве напрямую зависит сварное соединение и направленность шва, что позволяет подобрать специалиста в этой области и выяснить наилучший метод сваривания.
Положение пространственных кромок, которые в первую очередь подготавливаются для последующего соединения в единую конструкцию различных металлических образцов, определяет расположение швов при сварке. Существуют четыре главных положения сварочных работ: нижнее, потолочное, вертикальное и горизонтальное.
Вернуться к оглавлению
Нижнее расположение
Такое положение зачастую применяется в тех случаях, когда подвергаются свариванию простейшие элементы и если качество соединяющего рубца не имеет особого значения. Расположение свариваемых деталей горизонтально, а электрод должен быть в вертикальном положении.
С нижнего положения можно выполнить работу двухстороннего сваривания металлического элемента, толщина которого составляет 8 мм, а также одностороннее, с толщиной, не превышающей 4 мм. Во всех приведенных выше случаях конструкция будет достаточно прочной. Единственными моментами, которые могут оказать влияние на качество, являются:
- выбор диаметра электрода;
- размер и толщина свариваемых деталей, а также зазор между ними;
- сварочный ток и его величина.
В большинстве случаев сварка в нижнем положении является лучшим вариантом для соединения в одну конструкцию различных элементов на производстве.
В процессе расплавления электродный металл под действием естественной силы тяжести переносится в сварочную ванну, расположенную в горизонтальной плоскости. Единственный изъян данного положения – это вероятность возникновения прожогов, в связи с этим необходимо обеспечить максимально полное плавление, чтобы не допустить их появление. Данную задачу способен выполнить сварщик, не имеющий большого опыта в работе и повышенной квалификации. Не учитывая этого незначительного недостатка в нижнем положении, есть смысл отдать предпочтение такому виду и стараться задействовать его на различных этапах проектирования работ по сварке.
Вернуться к оглавлению
Вертикальное расположение
В процессе сваривания вертикального шва ванна плавленого металла под действием силы тяготения стекает вниз. В связи с этим его ведут короткой дугой с целью попадания расплавленных металлических капель в центр шва. При этом сам электрод краткими движениями слегка отводят от ванны, тем самым давая капле застывать. В основном соединения в вертикальном положении осуществляются снизу вверх, в этом случае нижний, уже застывший кратер не даст возможности растекаться металлической ванне.
Угол наклона электрода в данном случае обычно вниз или вверх. Когда сварщик наклоняет его вниз, он получает возможность просматривать, как распределяется металлическая ванна по стыку шва. Если нужно выполнить соединение сверху вниз, электрод необходимо сначала выставить в положение, а когда образуется капля, потихоньку опускать ее ниже, возникает очередной кратер, и капля может удерживаться от потека вниз благодаря более короткой дуге. Лучше всего вертикальный шов сваривать на небольшом токе с диаметром электрода 0,4 см. В этом случае получится малый объем расплавленного металла в шовном кратере.