Трубный сварочный шов. Применение автоматической сварки при строительстве трубопроводов. Сварка профильных труб
>>Неповоротные стыки труб
Сварка неповоротных стыков труб. Технология сварки труб без поворота
Стыки труб с диаметром более 300мм сваривают обратно-ступенчатым способом. Рекомендуемая длина каждого участка составляет 150-300мм. Порядок их сваривания показан на схеме ниже. Цифрами указана последовательность сварки участков по слоям, а стрелками - направление сварки.
Техника сварки неповоротного стыка
Первый слой выполняется с помощью возвратно-поступательного движения электрода с задержкой электрической дуги над ванной с расплавленным металлом. Сила тока выбирается порядка 140-170А, благодаря этому, появляется возможность проплавления кромок стыка и формирования тонкого нитевидного валика, высотой 1-1,5мм на внутренней стороне. В процессе сварки, необходимо следить, чтобы крупные брызги не попадали на свариваемые кромки металла.
Сварку необходимо вести без прожогов в металле. Для этого электрическая дуга должна быть короткой и не следует её удалять от ванны более, чем на 1-2мм. Накладывая каждый последующий слой, необходимо перекрывать начало и конец ранее наложенных слоёв на 20-25мм. Режимы сварки при выполнении второго слоя рекомендуются такие же, какие были при выполнении первого слоя. Электроду, при сварке второго слоя, необходимо сообщать поперечные колебания от края одной кромки к другой
При сварке корневого шва, поверхность каждого слоя может быть вогнутой или выпуклой. Но стоит иметь ввиду, что чрезмерная выпуклость может стать причиной появления непроваров в корне шва (см. рисунок ниже). Особенно опасна чрезмерная выпуклость при выполнении , т.к. зачастую нет возможности .
Для
возможности контроля над зоной сварки в направлении выполнения последнего слоя,
предпоследний слой необходимо сварить так, чтобы его поверхность была 1-1,5мм
ниже свариваемых кромок (см. рисунок справа).
При этом последний слой выполняют с усилением 2-3мм и шириной, на 2-3мм превышающей ширину разделки кромок. Кроме этого, последний слой должен иметь плавный переход от наплавленного металла к основному.
Видео: сварка неповоротного стыка. Замок на сварку
При производстве строительных и ремонтных работ, а также при прокладке коммуникаций рабочим приходится прокладывать километры трубопроводов. Все трубопроводы можно разделить на несколько категорий:
- магистральные трубопроводы;
- трубопроводы, по которым передается горячая вода (пар);
- трубопроводы, по которым передается газ;
- трубопроводы, предназначенные для устройства систем водоснабжения и канализации;
- промышленные и технологические трубопроводы.
К каждому конкретному виду трубопровода предъявляются определенные требования, касающиеся материала, используемого для монтажа труб, а также способа их соединения. Наиболее распространенным способом соединения трубопроводов является сварка. При этом выбор способа и условий, которыми характеризуется сварка стыков трубопроводов, регламентируют существующие правила и нормы Гостехнадзора.
Способы укладки трубопровода.
Сама укладка трубопровода может выполняться двумя способами:
- секционным;
- непрерывным.
При использовании непрерывного способа укладки выполняют постепенное наращивание трубопровода, при этом соединение производится без вращения труб. Секционный способ укладки предполагает сварку отдельных секций трубопровода с вращением труб в промышленных условиях, после чего готовые секции доставляются непосредственно на место прокладки трубопровода, где и соединяются в единое целое уже без вращения труб.
Требования к сварщикам и условиям выполнения сварочных работ.
Сварка стыков трубопроводов является одной из самых важных операций при монтаже трубопровода. К таким видам работ допускаются только высококвалифицированные сварщики, имеющие документ на право выполнения данного типа работ. В том случае, если сварщик только получил такой допуск и не имеет практического опыта или он не работал с трубопроводами в течение нескольких месяцев, перед тем как приступить непосредственно к работе, он должен выполнить контрольную сварку с использованием того же способа сварки, который будет потом применяться в сварочных работах. Кроме того, при выполнении контрольной операции он должен работать приблизительно в тех же условиях, которые будут присутствовать во время рабочего процесса. После выполнения контрольной сварки она тщательно проверяется и, если к сварному шву не возникает никаких претензий, сварщик допускается к выполнению основных работ.
Сварочные работы в полевых условиях разрешается выполнять при температуре воздуха не ниже -20 градусов по Цельсию, а если речь идет о легированных сталях, то температура воздуха при их сварке не должна быть ниже -10 градусов по Цельсию. Дело в том, что при более низкой температуре расплавленный металл сварного шва начинает активно насыщаться газами из окружающего воздуха (в основном, кислородом и водородом), а такие примеси способны сделать металл более пористым, то есть оказать большое влияние на прочность и надежность сварного соединения. Кроме того, при проведении сварки место, где работает сварщик, должно быть хорошо закрыто от ветра, дождя или снега.
Подготовка труб к сварке.
Большое значение для получения качественного сварного соединения имеет подготовка концов труб к сварке. Такая подготовка включает в себя:
- правку подвергающихся сварке концов;
- очистку кромок труб от загрязнений, масла или появившейся на них оксидной пленки;
- сборку труб.
Правка
Правка концов труб представляет собой придание месту стыка абсолютно круглой формы. Дело в том, что во время транспортировки труб их концы могут деформироваться, и в этом случае добиться качественного сварного соединения не представляется возможным.
Для того чтобы выправить концы труб, как правило, применяют различное механическое, гидравлическое или пневматическое оборудование. Например, во многих случаях для правки используют гидравлический домкрат и специальные радиальные колодки, которые вставляются внутрь трубы. При помощи домкрата колодки расширяются и, упираясь в стенки концов труб изнутри, придают им нужную форму.
Очистка
Свариваемые концы труб должны быть идеально чистыми. Способы очистки, в данном случае, выбираются в зависимости от того, какие именно загрязнения наблюдаются. Если, например, необходимо очистить концы труб от масла или органического налета, используют бензин или специальные растворители, обезжиривающие поверхность кромок. А для того чтобы избавиться от ржавчины, в большинстве случаев применяют специальные стальные щетки или абразивные круги.
Сборка
Сборка стыков труб представляет собой совмещение свариваемых концов труб. При этом должно соблюдаться три основных правила:
- поверхности подготавливаемых труб должны полностью совпадать;
- ось трубопровода не должна нарушаться;
- зазор между свариваемыми поверхностями труб должен быть одинаковым по всему диаметру труб.
Такая сборка может производиться и вручную, но стоит отметить, что это достаточно трудоемкий процесс, требующий большого внимания и аккуратности и не всегда дающий нужное качество сборки. Поэтому в большинстве случаев на этом этапе работ применяются специальные приспособления - центраторы, которые могут быть внутренними и наружными.
После того, как все подготовительные операции будут выполнены, сварщик может приступать к основным этапам работы. Что касается применяемых в данном случае способов сварки, то здесь, в зависимости от материала труб, требований к трубопроводу и условий работы, могут применяться различные способы сварки:
- по типу применяемой энергии - дуговая, газовая, плазменная, лучевая;
- по типу защиты - сварка под флюсом или сварка в защитных газах;
- по степени автоматизации - ручная, полуавтоматическая или автоматическая.
Что касается самого распространенного способа сварки, то более чем в половине случаев при сварке магистральных трубопроводов применяется автоматическая дуговая сварка под флюсом.
Общие сведения. При сооружении трубопроводов сварные стыки труб могут быть поворотными, неповоротными и горизонтальными (рис. 99).
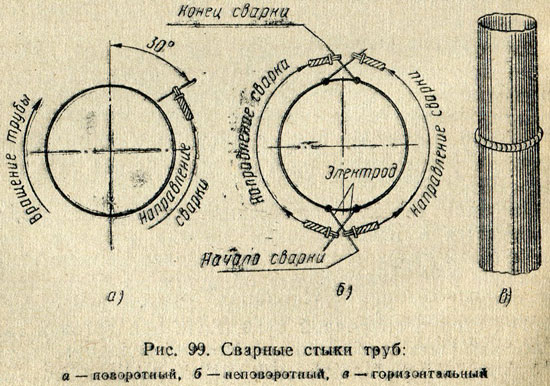
Перед сборкой и сваркой трубы проверяют на соответствие требованиям проекта, по которому сооружается трубопровод, и техническим условиям. Основными требованиями проекта, а также технических условий являются: наличие сертификата на грубы; отсутствие эллипсности труб; отсутствие разностенности труб; соответствие химического состава и механических свойств металла трубы требованиям, указанным в технических условиях или ГОСТах.
При подготовке стыков труб под сварку проверяют перпендикулярность плоскости реза трубы к ее оси, угол раскрытия шва и величину притупления. Угол раскрытия шва должен составлять 60 - 70°, а величина притупления 2 - 2,5 мм
(рис. 100). Фаски снимают с торцов труб механическим способом, газовой резкой или другими способами, обеспечивающими требуемую форму, размеры и качество обрабатываемых кромок.
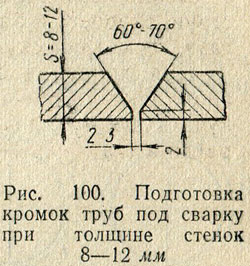
Разностенность толщин стенок свариваемых труб и смещение их кромок не должны превышать 10% от толщины стенки, но быть не более 3 мм
. При стыковке труб должен обеспечиваться равномерный зазор между соединяемыми кромками стыкуемых элементов, равный 2 - 3 мм
.
Перед сборкой кромки стыкуемых труб, а также прилегающие к ним внутренние и наружные поверхности на длине 15 - 20 мм
очищают от масла, окалины, ржавчины и грязи.
Прихватки, являющиеся составной частью сварного шва, выполняют те же сварщики, которые будут сваривать стыки, с применением тех же электродов.
При сварке труб диаметром до 300 мм
прихватка выполняется равномерно по окружности в 4 местах швом высотой 3 - 4 мм
и длиной 50 мм
каждая. При сварке труб диаметром более 300 мм
прихватки располагают равномерно по всей окружности стыка через каждые 250 - 300 мм
.
При монтаже трубопроводов необходимо стремиться к тому, чтобы по возможности больше стыков сваривалось в поворотном положении. Трубы, толщина стенки которых составляет 12 мм
, сваривают в три слоя. Первый слой создает местный провар в корне шва и надежное сплавление кромок. Для этого необходимо, чтобы наплавленный металл образовал внутри трубы узкий ниточный валик высотой 1 - 1,5 мм
, равномерно распределяющийся по всей окружности. Для получения провара без сосулек и грата движение электрода должно быть возвратно-поступательным с непродолжительной задержкой электрода на сварочной ванне, незначительным поперечным колебанием между кромками и образованием небольшого отверстия в вершине угла скоса кромок. Отверстие получается в результате проплавления основного металла дугой. Размер его не должен превышать 1 - 2 мм
больше установленного зазора между трубами.
Сварка поворотных стыков.
Первый слой высотой 3 - 4 мм
сваривают электродами диаметром 2-3-4 мм
. Второй слой наплавляется электродами большего диаметра и при повышенном токе. Первые два слоя можно выполнить одним из следующих способов:
1. Стык делят на четыре участка. Вначале сваривают участки 1 - 2, после чего трубу поворачивают на 180° и заваривают участки 3 и 4 (рис. 101). Затем трубу поворачивают еще на 90° и сваривают участки 5 Я 5,- затем поворачивают трубу на 180° и сваривают участки 7 и 8.
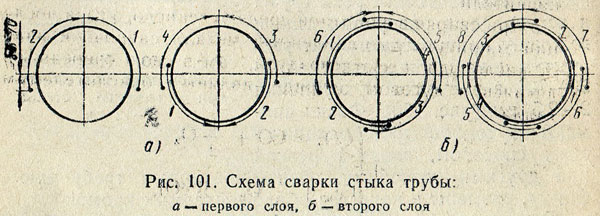
2. Стык делят на четыре участка. Вначале сваривают участки 1 и 2, затем поворачивают трубу на 90° и сваривают участки 3 и 4 (рис. 102). После сварки первого слоя трубу поворачивают на 90° и сваривают участки 5 и 6, затем поворачивают трубу на 90° и сваривают участки 7 и 8:
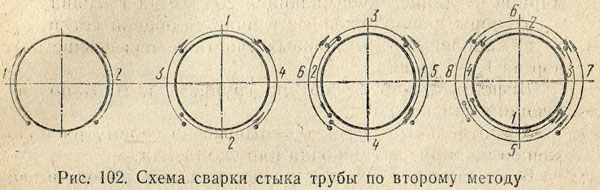
3. Стык делят на несколько участков (при сварке труб диаметром более 500 мм ). Сварку ведут обратно-ступенчатым способом отдельными участками (рис. 103). Длина каждого участка шва (1 - 5) составляет 150 - 300 мм и зависит от диаметра трубы.
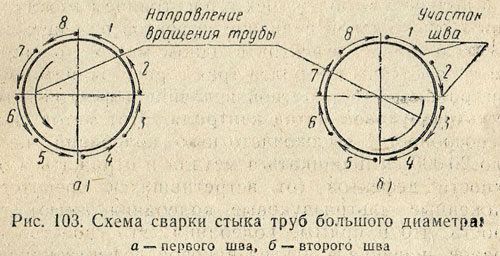
Третий слой во всех рассмотренных выше способах накладывают в одном направлении при вращении трубы. На трубах диаметром до 200 мм можно не делить стык на участки и сваривать его сплошным швом с поворотом трубы в процессе сварки (рис. 104). Второй и третий слои выполняются аналогично первому, но в противоположных направлениях. Во всех случаях необходимо каждый последующий слой перекрывать предыдущим на 10 - 15 мм .
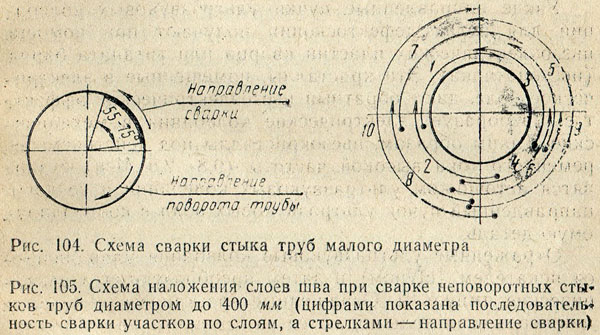
Сварка неповоротных стыков.
Неповоротные стыки труб при толщине стенок до 12 мм
свариваются в три слоя. Высота каждого слоя не должна превышать 4 мм
, а ширина валика должна быть равной двум-трем диаметрам электрода.
Стыки труб диаметром более 300 мм
свариваются обратно-ступенчатым способом. Длина каждого участка должна быть 150 - 300 мм
, порядок их наложения показан на рис. 105.**
*Первый слой образуется при поступательно-возвратном движении электрода с задержкой дуги на сварочной ванне. Величина тока устанавливается в 140 - 170 а
, что позволяет проплавлять кромки стыка с образованием узкого ниточного валика высотой 1 - 1,5 мм
на его внутренней стороне. При этом на свариваемые кромки не должны попадать крупные брызги расплавленного металла и сварка должна быть выполнена без прожогов. Для этого Дугу необходимо держать короткой, а отрывая от ванны, удалять ее не более чем на 1 - 2 мм
. Перекрытие начала и конца смежного слоя должно составлять 20 - 25 мм
.
Режим для сварки второго слоя тот же, что и для сварки первого слоя. Электрод при сварке второго слоя должен иметь поперечные колебания от края одной кромки к краю другой кромки.
При сварке поверхность каждого слоя может быть вогнутой (рис. 106, а) или слегка выпуклой (рис. 106,6). Чрезмерная выпуклость шва особенно при потолочной сварке (рис. 106, в) может быть причиной непровара.
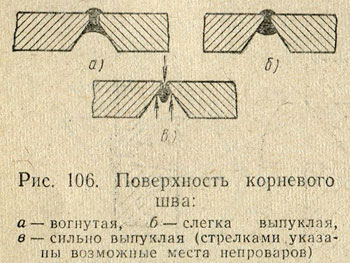
Для облегчения наблюдения за зоной сварки в направлении ведения последнего слоя, предпоследний слой накладывают в области кромок так, чтобы его поверхность была на 1 - 1,5 мм ниже свариваемых кромок (рис. 107). Последний слой выполняют с усилением 2 - 3 мм и шириной на 2 - 3 мм большей, чем ширина разделки кромок. Он должен иметь плавный переход от наплавленного металла к основному.
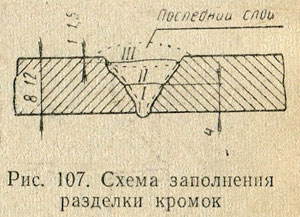
Сварка горизонтальных стыков. При сборке горизонтальных стыков труб нет необходимости полностью снимать кромки нижней трубы, достаточно лишь раскрыть ее на угол 10 - 15°, что улучшает процесс сварки без изменения ее качества (рис. 108, а). При сборке неответственных трубопроводов на нижней трубе фаска совсем не снимается (рис. 108,6).
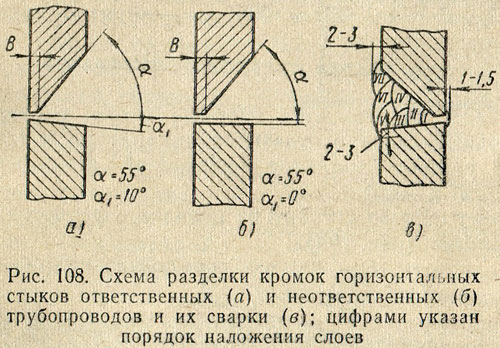
Лучшим методом сварки горизонтальных стыков является сварка отдельными валиками небольшого сечения. Первый валик накладывают в вершине шва (рис. 108, в), электродами диаметром 4 мм
(при токе 160 - 190 а
) при возвратно-поступательном движении электрода с обязательным образованием на внутренней стороне стыка узкого ниточного валика высотой 1 - 1,5 мм
. После первого валика (слоя) зачищают его поверхность. Второй валик накладывают так, чтобы он перекрывал первый при возвратно-поступательном движении электрода и его небольшом колебании от края нижней кромки до края верхней кромки. Сварка выполняется в том же направлении, что и сварка первого слоя (валика). Затем ток увеличивают до 250 - 300 а
и сваривают третий валик электродами диаметром 5 мм
, что повышает производительность сварки. Третий валик накладывают в противоположном направлении, чем сваривался первый шов. Он должен перекрывать 70% ширины второго валика. Четвертый валик укладывают в том же направлении, но располагают в углублении между третьим валиком и верхней кромкой.
При сварке стыка трубы более, чем в три слоя, начиная с третьего слоя, каждый последующий выполняется в противоположном направлении, чем предыдущий, Трубы диаметром до 200 мм
сваривают сплошными швами, а диаметром более 200 мм
- обратно-ступенчатым методом.
Стык трубопровода условно разделяют на 4 примерно одинаковых участка. Сначала сваривают участки 1-2, затем трубу поворачивают на 180° и заваривают участки 3 и 4. Схема этого способа сварки указана на рисунке ниже.
После сварки первого слоя, трубу разворачивают ещё на 90° и выполняют сваривание участков 5 и 6. И потом, после поворота трубы ещё на 180°, выполняют сварку оставшихся участков 7 и 8.
Второй способ сваривания труб с поворотом стыком
Также, как и в первом способе, стык условно делят на 4 примерно равных участка. Сначала сваривают участки 1 и 2, потом поворачивают трубу на 90° и выполняют сварку участков 3 и 4. Схема этого способа показана на рисунке ниже.
После того, как заварен первый слой шва, трубу поворачивают на 90° и сваривают участки 5 и 6, затем снова поворачивают трубу на 90° и сваривают участки 7 и 8.
Третий способ. Сварка поворотных труб большого диаметра
Данный способ сварки применяют для сваривания труб большого диаметра, более 500мм. При таком способе стык разделяют на несколько участков и сварку выполняют обратно-ступенчатым способом. Схема сварки показана ниже.
Третий слой сварного шва, независимо от способа сваривания первых слоёв, выполняют в одном направлении при постоянном повороте трубы.
Видео: сварка поворотных стыков труб
Часть 1. Провариваем корень шва:
Часть 2. Заполнение разделки:
Сварка поворотных стыков с диаметром трубы менее 200мм
Если диаметр соединяемого трубопровода не превышает 200мм, то стык можно не делить на участки, а сваривать его одним сплошным швом, см. рисунок ниже:
При этом второй и третий слой выполняют аналогично первому, но каждый раз, при последующем слое, меняют направление сварки на противоположное. И во всех случаях необходимо перекрывать каждый предыдущий слой последующим на 10-15мм.
Монтаж магистралей любого назначения из трубопроката производится чаще всего с помощью сварочных работ. Причём сварка труб в домашних условиях может производиться двумя способами:
- Дуговым;
- Газосварочным.
При этом оба вида сварки можно поделить на категории:
- Пластическая (сварка давлением);
- Сварка плавлением металла электрода и припоя.
К каждому из методов соединения металла предъявляются определенные требования, которых стоит придерживаться для получения высокого качества сварного шва.
Важно: сварочные работы производят в основном промышленным швом, который соответствует СНиП III-Г.9-62. Соблюдение норм и правил позволяет поучить шов высокого качества. При выполнении работ в основном используют автоматическое или полуавтоматическое оборудование.
Сварка дуговая электрическая
Этот тип соединения трубопровода выполняется при переменном или постоянном токе. Так, если речь идет о сварке труб при использовании постоянного тока, то к свариваемой трубе подсоединяют плюсовой провод, который подключен параллельно к плюсовому полюсу сварочного аппарата. А второй провод подключают к электроду и минусовому полюсу оборудования. Такая сварка называется сваркой с прямой полярностью. Если де провода соединяются в обратном (противоположном) порядке, то такое выполнение работ называют сваркой с обратной полярностью.
Важно: с точки зрения экономической выгоды более удобной считается дуговая сварка при переменном токе. В этом случае происходит меньшее потребление электроэнергии. Кроме того в этом случае обслуживание оборудования является более простым в отличие от ухода за оборудованием постоянного тока.
Сварка труб с помощью электродугового метода применяется по ГОСТ чаще всего для соединения элементов трубопровода, которые имеют внутренний просвет не менее 80 мм и толщину стенок от 3 мм. Электродуговая сварка выгодно отличается также и от газовой сварки тем, что для этой операции предусмотрено меньшее количество расходных материалов, которые в свою очередь имеют меньшую стоимость.
Принцип такого способа соединения заключается в непрерывном горении дуги, которая формируется между электродом и плавящейся кромкой металла. При горении души формируется постоянная температура около 3500 градусов по Цельсию. Благодаря этому металл трубопровода плавится и заполняет собой зазор между двумя элементами свариваемой магистрали.
Важно: при сварке движение электрода происходит сначала по направлению к зазору, потом вдоль него или поперек зазора. В результате получается ровный сварной шов товарного вида.
Стоит знать, что в зависимости от толщины стенок трубопровода зависит глубина (количество слоёв) сварного шва. Согласно ГОСТ сварной шов следует выполнять в такое количество слоёв:
- Для трубы со стенками до 3 мм формируют шов в один слой;
- Для трубопровода со стенками 4-5 мм шов делают в 2 слоя;
- Труба с толщиной стенок 6-9 мм - шов в три слоя;
- Толщина стенок 10-12 мм - шов толщиной в 4 слоя;
- Стенки 13-15 мм - шов в 5 слоев.
Соответствие рабочего места сварщика по ГОСТ
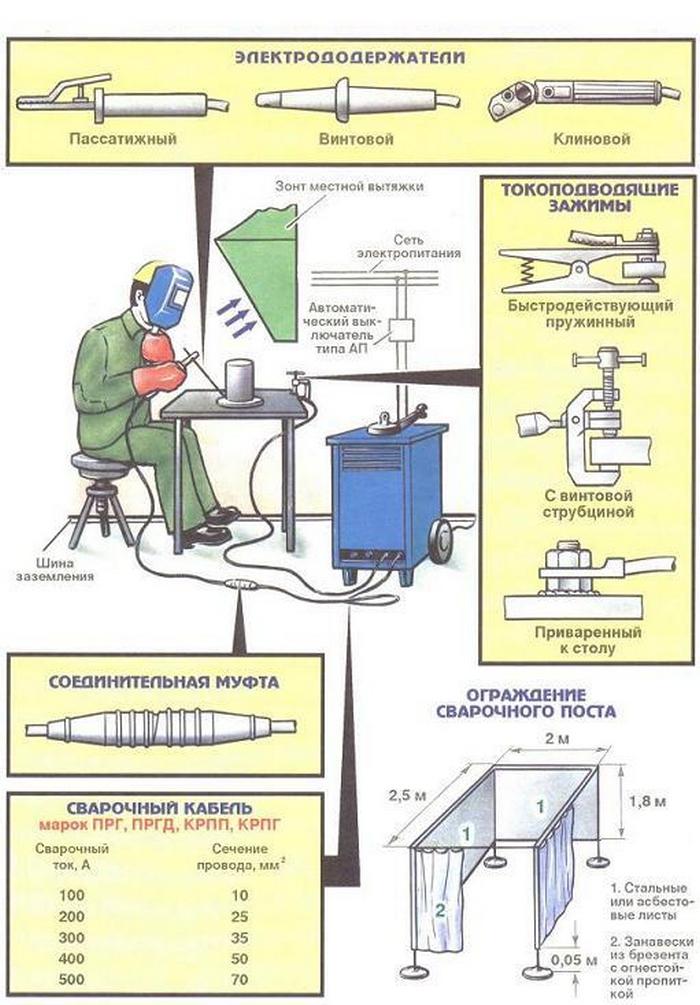
Оператор, выполняющий соединение трубопровода при помощи сварки должен иметь хорошо оборудованное рабочее место. На нём должны находиться все инструменты и комплектующие для выполнения качественной сварки:
- Сам сварочный аппарат;
- Ящики для электродов и огарков;
- Зубило и молоток для снятия шлака со сварочного шва;
- Гибкий сварочный кабель нужного сечения, качественно изолированный.
- Защитный костюм, рукавицы и шлем.
При этом стоит знать, что маска изготавливается из фанеры или специальной фибры, что позволяет защитить лицо и глаза от ультрафиолета, брызг расплавленного металла и инфракрасного излучения. Вес защитной маски составляет около 600 гр. в области глаз оператора располагается светофильтр, покрытый снаружи обычным стеклом. Такая вставка защищает глаза оператора от вредного излучения, образуемого при сварке.
Помимо перечисленных инструментов и костюма сварщик должен иметь электродержатель, который по ГОСТ должен соответствовать таким параметрам:
- Вес - не более 0,5 кг;
- Изоляция от тока;
- Иметь защиту от перегрева в условиях длительного применения;
- Кроме того, хороший электродержатель позволяет менять электроды под любым углов в процессе выполнения работ.
Выбор электродов
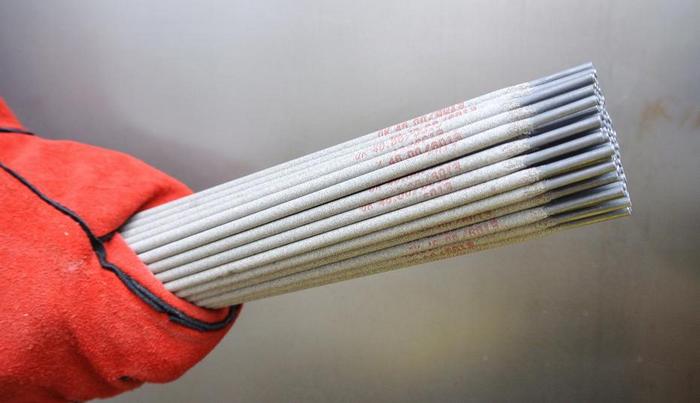
Качество сварки полностью зависит от правильно подобранных электродов. Грамотный выбор электрода позволяет получить надёжный и герметичный шов, отвечающий установленным стандартам.
По типу стали, для которой применим электрод, его можно поделить на такие типы:
- Э42А;
где буква Э означает слово «электрод», а число обозначает временное сопротивление металла трубопровода на разрыв при образовании шва.
Кроме того, стоит знать, что диаметр электрода также подбирается в зависимости от толщины стенок трубы.
Газовая сварка
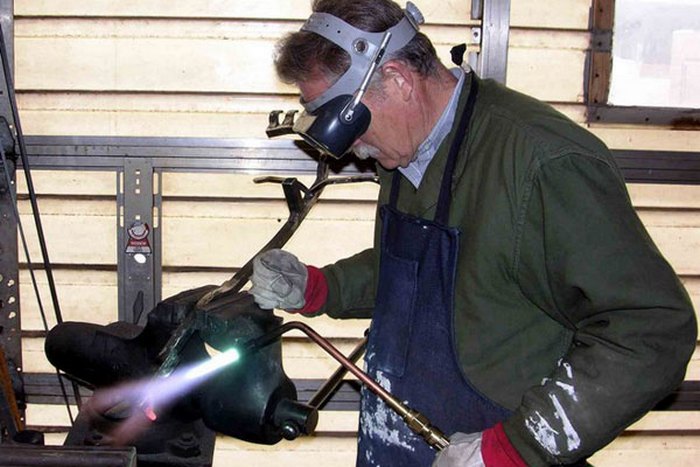
Этот способ соединения трубопровода рекомендовано по ГОСТ применять в том случае, если металл элементов для сварки имеет толщину стенок меньше, чем 3,5 мм и внутренний диаметр до 8 см. Обусловлено это тем, что газовая сварка менее травматична для металла (механическое воздействие на металл) ниже, чем электродуговая сварка. Кроме того, металл, расплавленный в результате газового сварного соединения, имеет меньшую вязкость и коэффициент удлинения.
Принцип выполнения газовой сварки заключается в формировании пламени от смеси кислорода и ацетилена. В результате пламя плавит металл трубопровода и специальной присадки, которая используется для формирования сварного шва.
Важно: стоит знать, что пламя газовой горелки способно прогревать металл на ширину, в 2,5-3 раза больший, чем глубина сварного шва.
Важно: чтобы сварить трубопровод с толщиной стенок от 4 мм и больше, необходимо формировать специальную кромку-фаску для более качественного плавления металла.
Согласно СНиП газовая сварка труб выполняется только в хорошо проветриваемом месте, поскольку испарение газов при сварке негативно действует на здоровье оператора.
Качество сварного шва по ГОСТ
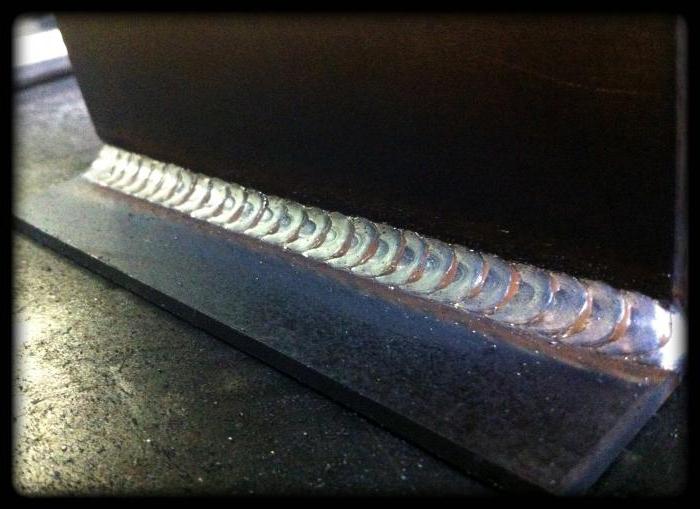
При проведении соединения труб методом сварки любого типа стоит контролировать качество шва. Такой процесс позволяет своевременно выявить дефекты сварных соединений и предотвратить разгерметизацию трубопровода. Контроль, согласно ГОСТ, проводят несколькими способами:
- Визуальный осмотр сварного шва на всех стадиях его формирования. Так, при визуальном осмотре следует выявлять наличие свищей, трещин и прожогов в металле. В случае обнаружения таких дефектов трубопровод переваривают заново, предварительно срезав некондиционный участок.
Важно: участки стыков, проваренные заново и подвергавшиеся исправлению, подлежат обязательным физическим испытаниям.
- Механические испытания сварки труб над сформированным швом и соединением труб. В этом случае сварной шов проверяют на растяжение, загиб, ударную вязкость или растяжение в зависимости от назначения магистрали. Чтобы проводить механические испытания полученного шва оператор во время сварки должен параллельно выполнять сварку пробных стыков. Именно они потом служат образцами для проведения механического контроля.
Важно: подобным методом проверяют качество сварки только на тех магистралях, которые подведомственны организациям Госгортехнадзора. При этом испытания проводятся в соответствии с ГОСТ 6996-54.
- Физический способ контроля сварки труб, подразумевающий использование рентгена, гамма-лучей, ультразвуковых волн и пр. Такие способы испытаний также выполняют только на трубопроводах особого назначения. В этом случае полученные швы подвергают просвечиванию рентген-лучами с целью выявления внутренних трещин, пор, шлака. При этом следует знать, что существую не только промышленные рентген-установки, но и мобильные, для выполнения физического контроля в монтажных условиях. Подобным образом и в этих же целях используют и гамма-лучи. При проникновении через сварной шов луч откладывает свой отпечаток на плёнку с внутренней стороны соединения. И если обнаружены недочеты и дефекты в сварном соединении, то плёнка в этих местах будет более тёмной. Физическая проверка проводится в соответствии с ГОСТ 7512-55. При этом отбраковке подлежат участки трубопровода с такими дефектами в соединении:
- Трещины любой формы и размера;
- Наличие шлака в сварном шве и пор, количество которых превышает 10% толщины стенки трубы;
- Наличие непровара в соединении, если его объем составляет от 15% и более толщины стенки металла.
Важно: исправлять дефекты в сварки труб можно только в том случае, если при диаметре трубы до 100 мм площадь трещины (дефекта) составляет до 20 мм, либо при сечении магистрали больше 100 мм площадь дефекта до 50 мм. В остальных случаях соединение должно быть удалено, а стык заваривается по новой.
- Пневматические и гидравлические испытания.
Важно: в некоторых случаях (в зависимости от назначения трубопровода) сварка труб может проверяться на коррозийность.