Как да разтопите алуминий у дома. Инвестиционно леене. Температури на солидус и ликвидус на алуминиеви сплави.
Топящо се мнозинство алуминиеви сплавине е трудно. Легиращите компоненти, с изключение на магнезий, цинк, а понякога и мед, се въвеждат под формата на лигатури.При топене на малки порции отлети сплави в тигелни пещи, защитни флюси, като правило, не се използват. Задължителна операция е рафиниране от неметални включвания и разтворен водород. Най-трудни за топене са алуминиево-магнезиевите и многокомпонентните термоустойчиви сплави.
При топенето на ковани сплави се обръща специално внимание на почистването на пещта от шлака и плен от предишната стопилка. При преминаване към друга марка сплав, с изключение на преходни стопилки, пещта и смесителите се измиват, за да се отстранят остатъците от старата сплав. Количеството метал за измиване трябва да бъде най-малко една четвърт от капацитета на пещта. Температурата на метала по време на измиване се поддържа на 40-50°C над температурата на леене на сплавта преди измиване. За да се ускори почистването, металът в пещта се разбърква интензивно в продължение на 8-10 минути. За измиване се използва алуминий или претопяване.В случаите, когато металът е напълно източен от пещта, може да се ограничи до измиване с флюси. Топенето на сплав се извършва под флюс
Зарядните материали се зареждат в следната последователност: алуминиеви слитъци, едрогабаритни отпадъци, претопяване, лигатури (чисти метали). Позволено е да се зареждат сухи стърготини и малки по размер скрап в течен метал при температура не по-висока от 730 ° C. Медта се въвежда в стопилката при температура 740-750 °C, силиций - при 700-740 °C с помощта на камбана. Цинкът се зарежда преди магнезия, който обикновено се въвежда преди източването на метала. Максимално допустимото прегряване за отливите сплави е 800-830 "C, а за кованите сплави 750-760 °C.
При разтопяване на въздух алуминият се окислява. Основните окислители са кислородът и водната пара. В зависимост от температурата и налягането на тези газове, както и от кинетичните условия на взаимодействие, в резултат на окисляване на алуминия се образуват алуминиев оксид Al2O3, както и Al2O и AlO. Вероятността за образуване се увеличава с повишаване на температурата и намаляване на парциалното налягане на кислорода в системата. При нормални условия на топене термодинамично стабилната фаза е твърд алуминиев оксид γ-Al2O3, който не се разтваря в алуминия и не образува нискотопими съединения с него. При нагряване до 1200 °C γ-Al2O3 прекристализира в α-Al2O3. По време на окисляването върху повърхността на твърд и течен алуминий се образува плътен, издръжлив оксиден филм с дебелина 0,1–10 µm, в зависимост от температурата и времето на излагане. Когато се достигне тази дебелина, окисляването на практика спира, тъй като дифузията на кислород през филма рязко се забавя.
Процесът на окисляване на течни алуминиеви сплави е много сложен и недостатъчно проучен. Наличните литературни данни показват, че интензитетът на окисляване на компонентите на сплавта е функция от налягането на кислорода, налягането на дисоциация на техните оксиди, концентрацията на компонентите в сплавта, скоростта на дифузия на атомите към кислородните атоми, взаимодействието на оксиди помежду си и др. Кинетиката на окисление се определя от непрекъснатостта, плътността и здравината на оксидните филми. При същата концентрация най-активните елементи се окисляват преди всичко, при което образуването на оксид е свързано с най-голямо намаляване на изобарно-изотермичния потенциал.
Повечето легиращи елементи (мед, силиций, манган) не оказват значително влияние върху процеса на окисление на алуминия и защитните свойства на оксидния филм, тъй като имат съотношение VMem0/mVMe≥1. Оксидният филм върху бинарни алуминиеви сплави с тези елементи при ниската им концентрация се състои от чист γ-Al2O3. При значително съдържание на тези елементи се образуват твърди разтвори на оксиди на легиращи елементи в γ-Al2O3 и съответните шпинели.
Алкалните и алкалоземните метали (калий, натрий, барий, литий, калций, стронций, магнезий), както и цинкът (0,05-0,1%) значително повишават окислимостта на алуминия. Причината за това е рехавата и пореста структура на оксидите на тези елементи. Оксидният филм върху двойните стопилки в този случай е обогатен с оксиди на алкални и алкалоземни метали. За неутрализиране на вредното въздействие на цинка в алуминиеви стопилки се въвежда 0,1-0,15% Mg.
Сплавите от алуминий с магнезий образуват оксиден филм с променлив състав. С ниско съдържание на магнезий от 0,005% (масови) - оксидният филм има структурата γ-Al2O3 и е твърд разтвор на MgO в γ-Al2O3; при съдържание от 0,01-1,0% Mg, оксидният филм се състои от шпинел (MgO*Al2O3) с променлив състав и кристали от магнезиев оксид; при съдържание над 1,5% Mg, оксидният филм се състои почти изцяло от магнезиев оксид.
Берилият и лантанът забавят окисляването на алуминиевите сплави. Добавянето на 0,01% берилий или лантан намалява степента на окисление на Al-Mg сплавите до нивото на окисление на алуминия. Защитният ефект на тези елементи се обяснява с уплътняването на оксидния филм чрез запълване на образуваните пори с оксиди на берилий и лантан.
Флуорът и газообразните флуориди (SiF4, BF3, SF6 и др.), присъстващи в атмосферата на пещта в количество до 0,1% (тегловно), значително намаляват окисляемостта на алуминиевите стопилки. Като се адсорбират върху повърхността на оксидния филм, те намаляват скоростта на проникване на кислород към металната повърхност.
Смесването на стопилката по време на процеса на топене е придружено от нарушаване на целостта на оксидния филм и смесване на фрагментите му в стопилката.Обогатяването на стопилките с оксидни включвания се получава и в резултат на обменни реакции с облицовката на топилните устройства. Най-значително влияние върху степента на замърсяване на стопилките от филми оказва повърхностното окисляване на материалите на първоначалния първичен и вторичен заряд. Отрицателната роля на този фактор се увеличава с намаляването на компактността и увеличаването на специфичната повърхност на материала.
Зарядният оксиден филм също е източник на насищане на стопилката с водород, тъй като 30-60% се състои от Al(OH)3. Химически свързаната влага почти не се отстранява от повърхността на зарядните материали дори при температура от 900 С. Хидроксидът, попадайки в стопилката, силно я насища с водород. Поради тази причина не е желателно да се въвеждат стърготини, дървени стърготини, обрезки, снаждения и други некомпактни отпадъци в шихтата. От особено значение е организацията на съхранение и навременна обработка на отпадъците и връщане на собствено производство, предотвратяване на окисляване и корозия с образуване на хидроксиди. Въвеждането на собствена възвръщаемост в шихтата е свързано и с неизбежното натрупване в сплавите на вреден примес от желязо, който образува сложни твърди интерметални съединения с компонентите на сплавите, които намаляват пластичните свойства и влошават обработката на отливки от рязане.
Наред с оксидите и интерметалните съединения, в стопилката могат да присъстват и други неметални включвания, като карбиди, нитриди и сулфиди. Въпреки това, тяхното количество е малко в сравнение със съдържанието на оксиди. Фазовият състав на неметалните включвания в алуминиевите сплави е разнообразен. В допълнение към алуминиеви оксиди, те могат да съдържат магнезиев оксид (MgO), магнезиев шпинел (MgAl2O4), алуминий, магнезий, титаниеви нитриди (AlN, Mg3N2, TiN), алуминиев карбид (Al4C3), алуминий и титанови бориди (AlB2, TiB2) и др. Основната част от включванията са оксиди.
В зависимост от произхода, неметалните включвания, открити в сплавите, могат да бъдат разделени на две групи: дисперсни включвания и филми.Огромната част от дисперсните включвания е с размер 0,03-0,5 микрона. Те са относително равномерно разпределени в обема на стопилката. Най-вероятната дебелина на оксидните филми е 0,1-1,0 микрона, а дължината е от десети от милиметъра до няколко милиметра. Концентрацията на такива включвания е относително ниска (0,1-1,0 mm2/cm2), а разпределението е изключително неравномерно. Когато стопилките престоят, големи включвания могат да плуват или да се утаят. Въпреки това, поради голямата специфична повърхност на филмите и малката разлика между тяхната плътност и плътността на стопилките, плуването (отлагането) протича бавно, повечето от филмите остават в стопилката и се пренасят в отливката, когато матрицата е пълни. Фино диспергираните суспензии се отделят още по-бавно. Почти всички отиват на кастинг.
По време на топенето алуминият се насища с водород, чието съдържание може да достигне 1,0-1,5 cm3 на 100 g метал. Основният източник на водород е водната пара, чието парциално налягане в атмосферата на пещите за топене на газ може да достигне 8-16 kPa.
Ефектът на легиращите елементи и примесите върху равновесната разтворимост на водорода в алуминия е малко проучен. Известно е, че медта и силиция намаляват разтворимостта на водорода, докато магнезият я увеличава. Разтворимостта на водорода се повишава и от всички хидрообразуващи елементи (титан, цирконий, литий, натрий, калций, барий, стронций и др.) Така една алуминиева сплав с 2,64% Ti може да отдели до 25 cm3 водород на 100 g , и алуминиева сплав с 5 % Zr - 44,5 см3 на 100 г. Алкалните и алкалоземните метали (натрий, литий, калций, барий), които образуват хидриди, най-активно повишават разтворимостта на водорода и алуминия.
Значителна част от водорода, разтворен в сплавите, е газът, въведен от основни сплави и електролитна мед.Например, алуминиево-титаниевата основна сплав, в зависимост от технологията на топене, може да съдържа до 10 cm3 водород на 100 g, а електролитната мед с натрупвания - до 20 см3 на 100 г. Летите сплави съдържат повече примеси и неметални включвания, отколкото кованите сплави. Следователно те са по-податливи на абсорбция на газ.
Кинетиката на процеса на хидрогениране на алуминиеви стопилки е ограничена от масовия пренос на водорода в течния метал, през повърхностния оксиден филм и в газообразна среда. Съставът на сплавта и съдържанието на неметални включвания, които определят пропускливостта на оксидния филм, дифузионната подвижност на водорода и възможността за освобождаването му от стопилката под формата на мехурчета, имат най-значителен ефект върху преноса на маса . Съставът на газообразната среда също оказва значително влияние върху пропускливостта на филма. Дифузионната подвижност на водорода в алуминия се намалява от мед, силиций и особено магнезий, манган и титан. Фино диспергирани неметални включвания, имащи висок адсорбционен капацитет за водород, силно забавят неговата дифузионна подвижност в алуминиеви стопилки.
Филмът от алуминиев оксид има ниска пропускливост за водородни атоми, той забавя реакцията на взаимодействието на стопилката с атмосферната влага. При дебелина на филма 1–10 µm газообменът между метала и атмосферата практически спира. Съставът на сплавта има голямо влияние върху пропускливостта на филма. Всички елементи, които повишават окислимостта на алуминия (магнезий, литий, натрий, стронций, калций), повишават пропускливостта на оксидния филм за водород. Легиращите елементи (мед, цинк, силиций) имат малък ефект върху газообмена. Те донякъде разхлабват оксидния филм и следователно допринасят за по-бързото насищане на сплавите с водород.
Съставът на атмосферата над стопилката значително влияе върху водородната пропускливост на оксидния филм. Пропускливостта на филма се увеличава значително, ако в газовата среда присъстват Cl2, C2Cl6, BF4, SiF4, фреони и други халогениди. Хлоридите, които имат висок афинитет към алуминия, се адсорбират, проникват под оксидния филм и го разрушават в резултат на образуването на газообразен алуминиев хлорид. Флуоридите взаимодействат по-малко активно с алуминия. Взаимодействайки с оксидния филм, те допринасят за дехидратацията на повърхността му и десорбцията на кислородни молекули и атоми. Имайки висок адсорбционен капацитет, флуоридите заемат освободените активни места върху филма и създават оксифлуоридни комплекси от типа Al2O2F2, които спират достъпа на кислород и водна пара до стопилката, правят филма тънък и пропусклив за водород. Течните потоци, съдържащи флуориди, също разрушават оксидния филм и улесняват дегазирането на стопилките.
Разтвореният водород, освободен при кристализацията на стопилките, причинява образуването на газ и порьозност при свиване на газ в отливките. С увеличаване на концентрацията на водород газовата порьозност на отливките се увеличава. Предразположението на алуминиевите сплави към газова порьозност се определя от степента на пренасищане на твърдия разтвор с водород, което се изразява като съотношението Stp=Szh. Степента на пренасищане на твърдия разтвор се увеличава с увеличаване на скоростта на охлаждане.
За всяка сплав има гранични концентрации на водород, под които газовите пори не се образуват в отливките при дадена скорост на охлаждане. Така например, за да се предотврати образуването на газови пори по време на втвърдяването на дебелостенни отливки от сплав от Al - 7% Si, съдържанието на водород в стопилката не трябва да надвишава 0,15 cm3 на 100 g. Ограничаващият водород съдържанието в дуралумините е 0,12-0, 18 cm3 на 100 g в зависимост от интензивността на охлаждане по време на кристализация.
Защитата на алуминиевите стопилки от окисляване и абсорбция на водород се постига чрез топене под флюс в слабо окисляваща атмосфера. Като покривен флюс при топенето на повечето сплави, съдържащи не повече от 2% Mg, се използва смес от натриев и калиев хлорид (45% NaCl и 55% KCl) в количество 1-2% от теглото на шихта. Съставът на флюса съответства на твърд разтвор с минимална точка на топене 660 °C. За тази цел се препоръчва и по-сложен поток (Таблица 12).
За алуминиево-магнезиеви сплави като покривен флюс се използват карналит (MgCl2 * KCl) и смеси от карналит с 40-50% бариев хлорид или 10-15% калциев флуорид. Ако използването на флюс не е възможно, защитата срещу окисляване се извършва чрез въвеждане на берилий (0,03-0,05%). Защитните флюсове се използват широко при топенето на сплави в реверберационни пещи.
За да се предотврати взаимодействието с влагата, се вземат мерки за отстраняването й от облицовката на топилни пещи и устройства за изливане, от рафиниране и модифициране на флюсове; инструментът за топене и изливане се подлага на калциниране и оцветяване, материалите на шихта се нагряват, почистват и изсушават.
Въпреки това, колкото и внимателно да е защитена стопилката, когато се стопи на въздух, тя винаги се оказва замърсена с оксиди, нитриди, карбиди, включвания на шлака и флюс, водород, следователно трябва да се почисти, преди да се излее във форми.
Рафиниране на стопилка
За почистване на алуминиеви сплави от суспендирани неметални включвания и разтворен водород се използват утаяване, продухване с инертни и активни газове, обработка с хлоридни соли и флюси, евакуация, филтриране през мрежести и гранулирани филтри и електропотоково рафиниране.
Като независим процес, утаяването може да се приложи в случаите, когато разликата в плътността е достатъчно голяма и размерът на частиците не е твърде малък. Хо и в тези случаи процесът е бавен, налага се повишена консумациягориво и се оказва неефективно.
Пречистването на стопилки чрез продухване с инертни или активни газове се основава на протичането на два процеса на дифузия на разтворения газ в мехурчета, издухването и плаващото действие на мехурчетата по отношение на включвания и най-малките газови мехурчета. Рафинирането се извършва толкова по-успешно, колкото по-малък е размерът на мехурчетата на издухания газ и толкова по-равномерно е тяхното разпределение в обема на стопилката. В тази връзка методът на обработка на стопилки заслужава специално внимание. инертни газовес помощта на порести керамични вложки. В сравнение с други методи за въвеждане на инертни газове в стопилки, продухването през порести вложки е най-ефективно.
Продухването на стопилки с газове се използва широко в леярните за производство на слитъци. Извършва се в специални облицовани кутии, монтирани по пътя на металното преливане от миксера към матрицата. За рафиниране на алуминиеви стопилки се използват азот, аргон, хелий, хлор и сместа му с азот (90%), пречистени от влага и кислород.
Продухването с азот или аргон се извършва при 720-730 °C. Продължителността на продухването, в зависимост от обема на стопилката, варира от 5-20 минути; консумацията на газ е 0,3-1% от масата на стопилката. Такава обработка позволява да се намали съдържанието на неметални включвания до 1,0-0,5 mm2/cm2 според технологичната проба на V.I. Добаткин и Б.К. Зиновиев, а съдържанието на водород е до 0,2-0,15 cm3 на 100 g метал.
Обработката на стопилки с хлор се извършва в херметични камери или черпаци с капак с отработени газове във вентилационната система. Хлорът се въвежда в стопилката през тръби с дюзи при 710-720 °C. Продължителността на рафинирането при налягане на хлора 108-118 kPa е 10-12 минути; консумация на хлор - 0,2-0,8% от теглото на стопилката. Използването на хлор осигурява по-високо ниво на пречистване в сравнение с техническия азот и аргон. Въпреки това, токсичността на хлора, необходимостта от обработка на стопилки в специални камери и трудностите, свързани с неговото изсушаване, значително ограничават използването на хлориране на стопилки в промишлени условия. Замяната на хлор със смес от хлор и азот (90%) осигурява достатъчно високо ниво на пречистване, но не решава проблемите, свързани с токсичността и изсушаването.
Дегазирането чрез продухване е придружено от загуби на магнезий: при третиране с азот се губят 0,01% магнезий; при третиране с хлор тези загуби се увеличават до 0,2%.
Рафинирането с хлориди се използва широко в фасонното и леярното производство. За целта се използват цинков хлорид, манганов хлорид, хексахлоретан, титанов тетрахлорид и редица други хлориди. Поради хигроскопичността на хлоридите те се подлагат на сушене (MnCl2, C3Cl6) или претопяване (ZnCl2). Технологията на рафинирането с хлориди се състои във въвеждането им в стопилката при непрекъснато разбъркване с камбана до прекратяване на отделянето на газообразни продукти на реакцията. Цинк и манганови хлориди се въвеждат в количество 0,05-0,2% при температура на топене 700-730°С. ° С; хексахлоретан - в количество 0,3-0,7% при 740-750 ° C на няколко стъпки. С понижаване на температурата ефективността на рафинирането намалява поради увеличаване на вискозитета на стопилките; рафинирането при по-високи температури е непрактично, тъй като е свързано с интензивно окисление на стопилката.
Понастоящем в цеховете за фасонно леене за рафиниране се използват широко таблетки от препарата Degaser, състоящ се от хексахлоретан и 10% (тегловно) бариев хлорид, които се въвеждат в стопилката без използване на "камбани". Притежавайки плътност, по-голяма от тази на стопилката, таблетките потъват на дъното на контейнера, осигурявайки обработката на целия обем на стопилката.
Хлоридните соли взаимодействат с алуминия според реакцията: 3MnCl2 + 2Al → 2AlCl3 + 3Mn.
мехурчета алуминиев хлорид, издигайки се към повърхността на стопилката, увличат суспендирани неметални включвания; водородът, разтворен в метала, дифундира в мехурчетата и стопилката се пречиства. След смесване стопилката се оставя да се утаи за 10-45 минути при 720-730°C, за да се отстранят малки газови мехурчета.
Рафинирането с хлориди се извършва в пещи или черпаци с малка специфична повърхност на стопилката. В пещи с нисък слой на топене, рафинирането с хлориди е неефективно. По отношение на нивото на пречистване от неметални включвания и газ, третирането с хлориди е по-ниско от продухването с хлор.
Пречистването на алуминиеви стопилки с флюси се използва при топенето на отливки и ковани сплави. За рафиниране се използват флюси на базата на хлоридни соли на алкални и алкалоземни метали с добавка на флуоридни соли - криолит, флуоров шпат, натриев и калиев флуориди (Таблица 13).
В практиката на топене на повечето алуминиеви ковани сплави за рафиниране се използва флюс № 1.
За почистване на алуминиеви сплави с магнезий се използват флюси на базата на карналит - 80-90% MgCl2 * KCl, 10-20% CaF2, MgF2 или K3AlF6. Върху повърхността на стопилката при 700-750 °C се изсипват предварително разтопени и изсушени флюси в количество 0,5-1% от теглото на метала. След това в продължение на 3-5 минути флюсът се омесва енергично в стопилката, шлаката се отстранява и стопилката се оставя да се утаи за 30-45 минути. След многократно отстраняване на шлаката стопилката се използва за запълване на форми. При обработка на големи обеми метал, потокът се въвежда в дъното на стопилката с помощта на "камбана".
За рафиниране на отляти алуминиеви сплави (силумини) широко се използват флюси № 2 и 13. Те се въвеждат в стопилки в течна форма в количество 0,5-1,5% (тегловни) и енергично се месят. Те допринасят за унищожаването на пяната, образувана при пълненето на черпаците за дозиране, и обогатяват стопилките с натрий.
По време на вакуумирането се получава високо ниво на отделяне на газ.Този метод на почистване се използва главно в модните леярни. Същността му се крие във факта, че металът, разтопен по стандартна технология в конвенционалните пещи, се излива в черпак, който след това се поставя във вакуумна камера. Металът в камерата се държи при остатъчно налягане от 1330 Pa за 10-30 минути; температурата на стопилката се поддържа в рамките на 720-740 °C. В случаите, когато евакуацията се извършва без нагряване, стопилката се прегрява до 760-780 °C преди обработка. Схемата на инсталацията за вакуумна дегазация е показана на фиг. 93
IN последните годиниза почистване на алуминиеви стопилки от неметални включвания, филтрирането през мрежести, гранулирани и порести керамични филтри все повече се използва в голям мащаб. Мрежестите филтри се използват широко за почистване на стопилки от големи включвания и филми.Те отделят онези включвания, чийто размер е по-голям от мрежестата клетка. За производството на мрежести филтри се използват стъклени платове от различни марки с размери на клетките от 0,5x0,5 до 1,5x1,5 mm и метални мрежи (от титан). В тях са монтирани филтри от фибростъкло разклонителни кутиии матрици, в затворни канали и разпределителни тигели (фиг. 94), използването им позволява да се намали съдържанието на големи неметални включвания и филми с 1,5-2 пъти; те не влияят на съдържанието на дисперсни включвания и водород.
Гранулираните филтри дават много по-голям почистващ ефект. Тяхната отличителна черта е голяма контактна повърхност с метала и наличието на дълги тънки канали с променливо напречно сечение. Пречистването на метални стопилки от суспендирани включвания по време на филтриране през гранулирани филтри се дължи на механични и адхезивни процеси. Първият от тях играе решаваща роля при отделянето на големи включвания и филми, вторият - при отделянето на фино диспергирани включвания. Поради ефекта на мрежата, гранулираните филтри задържат само онези включвания, чийто размер надвишава ефективния диаметър на междугрануларните канали. Колкото по-малък е диаметърът на филтърните зърна и по-плътна е тяхната опаковка, толкова по-високо е постигнатото ниво на пречистване на стопилките от големи включвания и филми (фиг. 95).
С увеличаване на дебелината на филтърния слой ефективността на почистване се увеличава. Омокрящите се в стопилка филтри са по-ефективни от тези, които не се омокрят.
Филтрите от сплав от калциеви и магнезиеви флуориди позволяват да се получат отливки от сплави AL4, AK6 и AMg6, 1,5-3 пъти по-малко замърсени с големи включвания, отколкото магнезитовите филтри.
Скоростта и режимът на протичане на стопилката през междугрануларните канали на филтъра оказват значително влияние върху пълнотата на разделяне на големи включвания и филми. С увеличаване на скоростта възможността за утаяване на включвания от движещ се поток под действието на гравитацията намалява и вероятността за отмиване на вече утаени включвания в резултат на хидродинамично действие, чиято степен е пропорционална на квадрата на филтрацията скорост, се увеличава.
Ефективността на пречистването на алуминиеви стопилки от фини включвания чрез гранулирани филтри се увеличава с влошаване на овлажняването на филтъра и включванията от стопилката.
За производството на филтри се използват шамот, магнезит, алунд, силициев диоксид, сплави на хлоридни и флуорни соли и други материали. Пълнотата на отстраняването на суспендирани неметални включвания зависи от естеството на филтърния материал. Най-ефективните филтри са тези, направени от флуориди (активни материали) (фигури 95 и 96).
Активните материали, заедно с големи включвания и филми, дават възможност за отделяне на до 30-40% от фино диспергирани суспензии и намаляване на съдържанието на водород в сплави, които са били рафинирани с флюс или хлориди с 10-20%. С отстраняването на фините суспензии размерът на зърното в отливките се увеличава, газосъдържанието намалява, пластичните свойства на сплавите се увеличават (фиг. 97) Диаметър 6 mm и височина на филтърния слой 100-120 mm.
Гранулирани филтри, както и мрежести филтри, се монтират по пътя на преместване на метала от смесителя в матрицата. При непрекъснато леене на блокове матрицата е оптималното място за монтаж; при профилно отливане филтърът се поставя в щранг, разпределителен тигел или литникова купа.
Типичните оформления на гранулирани филтри при леене на профилни отливки и блокове са показани на фиг. 98
Преди употреба филтърът се нагрява до 700-720 °C, за да се отстрани адсорбираната влага и да се предотврати замръзване на метала в каналите.
Пълненето се извършва по такъв начин, че горното ниво на филтъра да е покрито с метален слой от 10-15 mm, а изтичането на метал след филтъра се случва под наводненото ниво. При тези условия остатъчното съдържание на неметални включвания и филми в отливката може да се увеличи до 0,02-0,08 mm2/cm2 според технологичната проба на V.I. Добаткин и В.К. Зиновиев, т.е. 2-4 пъти намален в сравнение с филтрирането през мрежести филтри.
Повечето ефективен методпречистване на алуминиеви стопилки от филми и големи неметални включвания - рафиниране с електропоток. Същността на този процес се състои в преминаване на тънки струи от стопилка през слой от течен поток с едновременно налагане на постоянно или постоянно поле върху метала и потока. променлив токкоето създава повече благоприятни условияза адсорбция на включвания от поток в резултат на намаляване на повърхностното напрежение на границата с метала. С увеличаване на специфичната повърхност и продължителността на контакт на метала с потока, ефективността на почистване се увеличава. Следователно, конструкциите на устройствата за рафиниране на флюс и електрофлюс предвиждат струйно раздробяване (фиг. 99).
Оптималният режим на рафиниране на електропотока включва преминаване на метална струя с диаметър 5-7 mm, нагрята до 700-720 ° C, през слой от разтопен поток с дебелина 20-150 mm с прилагане на поле постоянен токмощност 600--800 A и напрежение 6-12 V с катодна поляризация на метала. При разход на флюс (карналит с 10-15% CaF2, MgF2 или K3AlF6 за сплави Al - Mg и Al - Mg - Si и криолит за други алуминиеви сплави) 4-8 kg на 1 тон стопилка и внимателно отстраняване на влагата от устройства за флюс и изливане, съдържанието на големи неметални включвания в сплави AK6, AMg6, V95 може да бъде намалено до 0,003-0,005 mm2/cm2 според технологичната проба.
За разлика от гранулираните филтри, електропоточното рафиниране не влияе върху макроструктурата на сплавите, което показва по-ниската му ефективност при почистване от дисперсни неметални включвания.
Кованите и отлети сплави също са подложени на рафиниране от метални примеси: натрий, магнезий, цинк и желязо.
Отстраняването на натрий от алуминиеви и алуминиево-магнезиеви ковани сплави AMg2, AMg6 се извършва чрез продухване на стопилките с хлорни или хлоридни пари (C2Cl6, CCl4, TiCl4), фреон (CCl2F2) и филтриране през AlF3 гранулирани филтри на зърнест 4-6 мм. Използването на тези методи позволява да се доведе до 2/3*10-4% остатъчното съдържание на натрий в стопилката. Вредното въздействие на натрия върху технологичните свойства на сплавта може да бъде потиснато чрез въвеждане в стопилката на добавки от бисмут, антимон, телур или селен, които образуват с натрия огнеупорни интерметални съединения.
Вторичните алуминиеви сплави в някои случаи се подлагат на пречистване от примеси на магнезий, цинк и желязо чрез флюс, вакуумна дестилация и утаяване, последвано от филтриране. Отстраняването на магнезий чрез флюс се основава на реакцията 2Na3AlF6 + 3Mg → 6NaF + 3MgF2 + 2A1. Повърхността на стопилката е покрита с флюс, състоящ се от 50% криолит и 50% натриев хлорид. След това сплавта се нагрява до 780-800 °C и интензивно се смесва заедно с флюса в продължение на 10-15 минути. Продуктите на реакцията, които са изплували на повърхността на стопилката, се отстраняват; с високо съдържание на магнезий (1-2,5%), процесът на рафиниране се повтаря няколко пъти. С помощта на криолит съдържанието на магнезий в стопилката може да се намали до 0,1%. Рафинирането на вторични алуминиеви сплави от магнезий може да се извърши успешно с флюс, състоящ се от 50% Na2SiF6, 25% NaCl и 25% KCl. За тези цели могат да се използват кислород-съдържащи потоци, като калиев хлорат (KClO3).
Пречистването на стопилки от магнезий и цинк се извършва във вакуумни дестилационни пещи при 950-1000°C. В резултат на такава обработка се получават сплави, съдържащи 0,1-0,2% Mr и 0,02-0,05% Zn. Пречистването на стопилки от магнезий чрез дестилация се извършва в случаите, когато съдържанието му в сплавта е високо и използването на почистване на флюс става нерентабилно.
Утаяването може да намали съдържанието на желязо в алуминиевата сплав до 1,7%, т.е. почти до евтектичното съдържание, според диаграмата на равновесното състояние алуминий-желязо. По-нататъшно намаляване се постига чрез комбиниране на процеса на утаяване с въвеждането на хром, манган или магнезий в сплавта.Добавянето на тези елементи измества евтектичната точка към алуминия и допринася за отделянето на излишното желязо. С въвеждането на 1-1,5% Mn в стопилката, съдържанието на желязо в нея може да бъде намалено до 0,7%. Магнезиевата добавка в количество от 25-30% ви позволява да донесете съдържанието на желязо до 0,1-0,2%. Процесът на отделяне на интерметалните съединения на желязото се ускорява чрез комбиниране на утаяване с филтрация. Филтрирането се извършва през базалтов филтър, нагрят до 700 °C с помощта на вакуум. Рафинирането от желязо с магнезий е приложимо за сплави, съдържащи не повече от 1,0% Si. При по-високо съдържание на силиций се образуват силициди, които значително усложняват филтрирането и премахват значително количество магнезий от цикъла. Освен това сплавта е изчерпана от силиций.
Отпадъците от алуминий и дуралум лесно се топят буквално у дома. И за това не е необходимо да се изграждат доменни пещи, да се създава сцепление, както е обичайно в съответствие със стандартните условия.
Авторът на метода за топене на алуминий на газов котлон използва черпак от неръждаема стомана като тигел. Точката на топене на алуминия е 660 градуса. Газова печкане може да осигури такова отопление. Първо, в рамките на 15 минути тигелът със съдържанието се затопля, след което се включва газов котлон, което осигурява температурата, необходима за стопяване на алуминия. Готови топилни пещив този магазин.
Внимание! Не използвайте такъв нестабилен тигел като в това видео. Не забравяйте да използвате аспиратора, оставете прозореца отворен и не работете често у дома с разтопен алуминий.
Какво може да се направи с помощта на такива топилни пещи? Например, както в нашия уебсайт, можете да направите алуминиев модел оръжия. Това изисква пяна, пясък и топилна машина. Между другото, статията съдържа и линк към аналог на топилната, който е представен тук.
Мнозина възприемат термина "леярна" като нещо, свързано с голямо производство и професионални умения и способности. Но всъщност леенето на част у дома е реалистично дори за самия хуманист, който не знае нищо за техниката на леене.
Как да отлеете алуминиева част
Характеристика на метала
Алуминият е един от най-евтините, най-разпространените и достъпни метали, който може лесно да се обработва и отлива. Основните характеристики на алуминия са висока електрическа и топлопроводимост, както и повишена устойчивост на корозия. Точката на кипене на този сребристо-бял метал е 2500 °C. Чистият алуминий се топи при 660°C, докато техническият алуминий се топи при 658°C. Малко вероятно е домашните отоплителни уреди да осигурят такава температура, така че е по-добре да използвате тигелна муфелна пещ за отливане на алуминиева част.
Муфелна пещ и нейното предназначение
Муфелната пещ е незаменимо устройство за самостоятелно нагряване на различни метали у дома. Такова устройство е способно да топи не само алуминий, но и мед и много цветни метали, както и сушене и изпичане на керамични продукти.
Видове муфелни пещи
Муфелните устройства за топене на метали са от следните видове:
- вакуум;
- въздух;
- газ;
- електрически.
По дизайн те са разделени на:
- тръбни;
- вертикален;
- хоризонтален;
- с форма на камбана.
Муфелната пещ се състои от нагревателна камера и специален акумулатор на топлина.
Изработване на муфелна пещ със собствените си ръце
За производството на устройството, от което се нуждаем следните инструменти и материали:
- тел;
- Български;
- тухли (7 бр.);
- защитни очила;
- чук;
- метална кофа;
- парче желязо и др.
Етапи на изграждане на пещ:
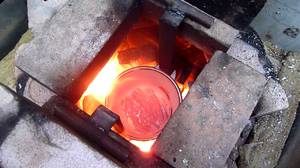
За повече функционалност е разрешено монтаж на два електрически нагревателя, който може да се включва последователно или едновременно. Например, за запояване на малко количество суровини, се включва само един долен нагревател и ако мащабът на топене е голям, се използват две устройства.
Муфелната пещ с горно зареждане е много компактна, което позволява да се съхранява в селска къща, в гаража или на балкона.
Принципът на работа на пещта е доста прост: на работната повърхност на пещта се монтира контейнер за запояване (тигел) с поставени там суровини, където се нагрява до желаната температура (660 ° C). Загрятият метал се излива в предварително подготвена форма, която може да бъде направена от гипс или друг негорим материал. За производството на формата се препоръчва използването на бяла или скулптурна мазилка, която може да бъде закупена във всеки магазин за строителни материали.
Както споменахме по-рано, за запояване на алуминий в пещ нужда от специална кофа(тигел), който е направен от метал с точка на топене по-висока от тази на алуминия или от огнеупорен материал. За производството на съдове за топене на алуминий, порцелан, графит, корунд, кварц, стомана или чугун. Кофата може да бъде закупена в специализиран магазин или направена самостоятелно. Размерът на тигела се определя от очакваното количество суровина за топене.
Металът трябва да бъде положен възможно най-плътно и леко притиснат. Тъй като алуминият значително губи обем по време на топенето, суровините трябва периодично да се добавят към черпака.
Важно. Добавената суровина трябва да е абсолютно суха, тъй като дори малко количество влага, която попадне в горещия алуминий, може да причини рязко пръскане, в резултат на което металът изпръсква от пещта и може да причини тежки изгаряния, особено ако разтопен алуминий попада в очите ви.
Ето защо, преди да започнете работа, трябва да се погрижите за вашата безопасност: закупете очила или маска и е по-добре да вземете специален огнеупорен металургичен костюм.
В процеса на топене на метал у дома, върху повърхността на горещ алуминий ще се появи оксиден филм, както и се образуват различни шлаки(стара боя, частици мръсотия и др.). Неговото количество зависи пряко от качеството на суровините. Преди да излеете разтопения метал във форми, е необходимо да отстраните шлаката със специални инструменти. След това се препоръчва да държите алуминия в пещта още известно време, за да направи метала по-течен. Това значително ще опрости по-нататъшното му леене.
Ние сами отливаме алуминиеви части
Помислете за най-лесния начин за запояване на част у дома.
ще ни трябва:
- метален скрап;
- черпак за топене;
- калъпи.
Стъпки на процеса:
- Пригответе контейнер за топене на алуминий у дома. За тази цел можете да използвате парче стоманена тръба.
- Направете формуляр. За части със сложна структура формата може да се състои от няколко елемента. Формата може да бъде направена от гипс (скулптурна). Никога не използвайте алабастър!
- За да избегнете залепването на гипс към контейнера за формата, първо трябва да го смажете с масло.
- В процеса на изливане на гипс контейнерът трябва периодично да се разклаща, за да се предотврати образуването на мехурчета.
Важно. Тъй като гипсът се втвърдява много бързо, опитайте се да поставите модела на детайла в гипс възможно най-скоро. Също така се препоръчва да се монтира малък предмет (например пръчка) в гипс, който ще служи като канал за изливане на бъдещата част.
За мнозина терминът "леярна" е тясно свързан с претоварване и специални професионални умения. Всъщност е реалистично да отлеете част от необходимия метал за най-много обикновен човекбез тренировки вкъщи. Процесът има свои тънкости, но е по силите да го направите у дома със собствените си ръце. Външно наподобява производството на оловни тежести за риболов. Характеристиките на процеса на леене на алуминий са свързани с технически спецификацииматериал.
Как да пикаеш аалуминий
характеристики на алуминия.Алуминият е един от най-разпространените метали.
Той е сребристо-бял на цвят, достатъчно добре се поддава на леене и механична обработка. Поради своите характеристики алуминият е снабден с висока топло- и електрическа проводимост, а също така има устойчивост на корозия.
За технически алуминий точката на топене е 658 градуса, за алуминий с висока чистота - 660, точката на кипене на алуминия е 2500 градуса.
За леене на алуминий домашните отоплителни уреди едва ли ще бъдат полезни и ще осигурят желаната температура. Необходимо е алуминият да се стопи, като се нагрее до температура над 660 градуса.
Алуминиева отливка: избор на източник на топлина
Като източник на топлина за топене на алуминий можете да използвате:
- Много ефективен метод се постига благодарение на самостоятелно изработена тигелна муфелна пещ. В работната повърхност на тази пещ е монтиран тигел (необходим инструмент за топене на алуминий), към него се добавят суровини. С помощта на муфелна пещ е много лесно да се лее алуминий.
- За да се получи точката на топене на алуминия, температурата на горене на втечнен или природен газ, в този случай процесът може да се извърши в домашна фурна.
- С малко количество топене можете да използвате топлината, получена от изгаряне на газ в домакинска газова печка.
- Необходимата температура ще бъде осигурена от газови резци или ацетиленови генератори, ако има такива в домакинството.
Алуминиева подготовка
Въпреки факта, че процесът на топене ще се извършва у дома, той трябва да се подхожда отговорно. Металът първо трябва да бъде почистен от мръсотия, натрошен на малки парченца. В този случай процесът на топене ще върви по-бързо.
Изборът е спрян на по-мек алуминий, като по-чист материал, с по-малко примеси. По време на топенето шлаката се отстранява от течната повърхност на метала.
Пясъчно леене
За производството на леярски части се използват няколко технологии. Най-простото е пясъчно леене:
- Ако е необходимо да се произведе алуминиева част с проста форма, тогава леенето може да се извърши по открит метод директно в почвата - силициев диоксид. Те правят малък модел от всякакъв материал: дърво, полистирол. Инсталиран в колба. Почвата се полага на малки слоеве и внимателно се набива. След като пробата се отстрани, силициевият диоксид поддържа формата си добре и леенето се извършва директно в него.
- Като формираща смес можете да използвате пясък, комбиниран със силикатно лепило, или цимент, смесен със спирачна течност. Съотношението на материалите трябва да бъде такова, че ако сместа се компресира, тя запазва формата си.
Видео "Леене на алуминий в глинена (пясъчна) форма у дома"
За детайли сложна формаизползва се друга технология.
Инвестиционно леене
Този отдавна известен метод за производство на алуминиеви продукти у дома може да бъде леко модифициран. Принципът на леене е както следва:
Моделът е изработен от стопяем материал. Полага се в определена форма, излива се с мазилка. Монтират се един или няколко тръбопровода. След като мазилката се втвърди, тя се изсушава добре. При високи температури разтопимият материал става течен и изтича през тръбопровода. В получената форма се излива алуминиева заготовка.
Подробностите за процеса могат да бъдат изяснени във видеото.
Видео "Алуминиево леене под високо налягане"
По този начин дори най-обикновеният любител може да направи необходимата част от алуминий с различни форми.
Как да отлеете сложна форма от алуминий
В промишлените предприятия често се използват метални форми. Формите за леене на алуминий могат да бъдат получени от различни материали. Най-често се използва гипс. Гипсът може да бъде закупен във всеки магазин за хардуер на всяка цена, която можете да си позволите. Препоръчва се използването на скулптурна или бяла мазилка.
Отличен вариант е скулптурният, който е обозначен с G-16. Поради високата цена може да бъде заменен с G-7 - обикновен бял гипс. Строго е забранено да се заменят с алабастър, въпреки факта, че са вътре строителни дейностичесто взаимозаменяеми.
Нека разгледаме един прост начин за отливане на алуминиева част със собствените си ръце у дома.
За да отлеем алуминиева част, имаме нужда от:
- съд за топене;
- метален скрап;
- калъп за топене.
Основните етапи на процеса:
1. Подготвяме съд за топене (може да използвате съд от част от стоманена тръба).
2. Правим форма за топене. Ако частта има сложна структура, тогава формата може да има няколко компонента.
В нашата версия формулярът ще се състои от две части. Първо, помислете как да опростите частта за удобство (препоръчваме да подсилите дупките с лента).
Формата е много лесна за изработка от скулптурна мазилка (не използвайте алабастър!). Можете да използвате пластилин.
3. Преди да излеете гипса, съдът трябва да се намаже с масло, за да не може гипсът да залепне за съда.
4. Внимателно изсипете гипса, периодично разклащайте формата, за да освободите мехурчетата.
Важно е да знаете:процесът на втвърдяване на гипса е доста бърз, така че бъдете внимателни и се опитайте да инсталирате модела в гипс навреме.
5. Изисква първичен слой за предстоящото изливане.
Взимаме бормашина и правим 4 малки дупки, обработваме формата с масло. Това е необходимо, за да може готовите части на формите да лежат възможно най-стабилно по време на процеса на леене.
6. Запълване на втория слой.
7. След като настъпи втвърдяване, е необходимо внимателно да извадите формата от контейнера и да отделите половинките.
8. Преди леене обработваме формата със сажди, за да избегнем залепването на течен алуминий. Формата трябва да изсъхне. Естествено, процесът на сушене протича през целия ден. Препоръчително е да изсушите гипсовата заготовка във фурната. Започнете при температура 11 - един час и два часа при температура 300 В. В мазилката трябва да се предвидят отвори за изливане на алуминий и отстраняване на остатъчния въздух.
По този начин топим алуминия.
9. След това поставяме течния метал във формата и изчакваме да изстине напълно.
В резултат на това получаваме желания детайл, след което го смиламе и правим специални дупки.
Изгорели отливки: технологични характеристики
Производството на алуминиеви части чрез изгорено леене има свои собствени характеристики, които ще бъдат разгледани по-долу. Работата се извършва в следната последователност:
- Като материал за модела у дома е използван стиропор. С помощта на режещи елементи и лепило направете фигура, която наподобява желаната форма с очертания.
- Подгответе съд за направата на модел. Можете да използвате стара кутия за обувки. Смесете алабастър с вода. Изсипете сместа в кутията. Поставете модела от пяна. Изгладете. Дайте време на материала да изсъхне добре. Поради бързия процес на втвърдяване на алабастър, работете с ускорени темпове.
- Премахнете кутията. Загрейте формата във фурната, за да изсушите алабастъра и да премахнете останалата влага. В противен случай цялата вода от алабастъра ще влезе в алуминия и ще се превърне в пара, което ще доведе до изпръскване на пори в метала и алуминий от матрицата по време на работа.
- Разтопете алуминия. Отстранете стопената шлака от повърхността на течността. Изсипете метала във формата на мястото на пяната. От висока температурапоследният ще започне да изгаря и алуминият ще заеме неговото място.
- След като металът се охлади, счупете формата и отстранете получения модел от лят алуминий. Можете да видите процеса по-подробно във видеото.
Безопасност и подготовка на работното място
Високотемпературната работа се характеризира с вредни изпарения и е придружена от отделяне на дим, така че трябва да се извършват на открито или в принудително вентилирано помещение. Трябва да се използва страничен вентилатор.
Процесът на леене е придружен от пръски, възможни са потоци от разтопен метал. работно мястопърво ще трябва да го покриете с метален лист. Не се препоръчва да се извършва работа в жилищен район - това е опасно за другите.
Основните грешки при леене на алуминий
Преди да извършите алуминиево леене у дома, обърнете внимание на основните грешки, които се наблюдават по време на работа:
- При производството на гипсови форми е необходимо цялата влага да се изпари по време на процеса на сушене. В противен случай при пълнене на формата водата започва да се изпарява, превръща се в пара и може да остане вътре в алуминия под формата на пори и черупки.
- При недостатъчно нагряване или ако алуминият е изстинал преди започване на работа, металът няма да запълни добре матрицата и отдалечените зони ще останат кухи.
- Не охлаждайте метала чрез потапяне в течност. В този случай вътрешната структура на материала е нарушена.
Алуминият може да се огъва като хартия или да бъде твърд като стомана. Алуминият е навсякъде, дори в нас.
Всеки възрастен човек получава около 50 mg алуминий всеки ден чрез храната, това не е диета, просто е неизбежно.
Алуминият е най-разпространеният метал на планетата. Съдържанието му в земната кора е 8%, но не е лесно да се извлече, поне в чист вид.
За разлика от златото и среброто, алуминият не се среща като късове или цели вени. Алуминият е 3 пъти по-лек от желязото или медта.
Алуминият в оригиналната си форма изобщо не прилича на метал, всичко това се дължи на специалната "любов" на алуминия към кислорода.
Всъщност първата употреба на алуминий в историята се случи, когато ориенталските грънчари добавиха богата на алуминий глина към своите продукти, за да ги направят по-здрави. .
Достатъчно, за да направи кутии за бира, достатъчно здрави за състезателни автомобили, гъвкави за кожи на самолети, способни да се превърнат във всичко, алуминият е незаменим материал за съвременния свят.
И това не са всички функции, които този полезен метал съхранява.
При топене и леене на въздух алуминиевите сплави лесно се окисляват и насищат с водород, а вредното влияние на разтворените газове върху качеството на отливките се забелязва дори при малки количества от тях в стопилката. Практиката установи, че максимално допустимото количество водород в алуминиеви сплави, което позволява получаването на висококачествени отливки, се оценява на 0,1-0,20 cm 3 /100 g метал. Следователно основното внимание по време на топенето се обръща на предотвратяването на прекомерно окисление и насищане с газ на сплавта. Предвид вредното въздействие на примесите в алуминиевите сплави, те също се стремят да получат сплав с минимални количества от тези примеси, особено желязо.
Методите за топене на алуминиеви сплави зависят от вида на пещите и използваните материали за зареждане. Типът на топилните пещи се избира в зависимост от естеството на производството и предназначението на сплавта.
Топенето на алуминиеви сплави се извършва в тигелни пещи с нафтово, газово и електрическо отопление, в пламъчни реверберационни пещи, подови електросъпротивителни пещи и индукционни пещи. Според предназначението се разграничават топилни, разпределителни и топилно-разпределителни пещи.
Най-висококачествен метал се получава чрез топене в индукционни пещи. В тези пещи топенето протича бързо, металът е добре смесен и по-малко наситен с газ. Газовите ревербераторни пещи се използват за топене на алуминиеви сплави в цехове за леене на заготовки, както и за претопяване на отпадъци и стърготини. Рефлективните пещи с електрическо съпротивление са често срещани във фасонните леярни.
Тигелните пещи с различни методи на нагряване се използват за топене на относително малки количества метал (те са особено удобни като задържащи пещи).
За топене на алуминиеви сплави се използват метални заварени, отлети, по-рядко ковани тигли.
При топене в метални тигели има опасност сплавта да взаимодейства с тигела и да го замърси с примеси от желязо. Най-агресивни по отношение на чугунените тигели са алуминиевите сплави със силиций, след това с магнезий и по-малко с мед и цинк. Следователно стените на тигелите са покрити със специални защитни бои преди топене, освен това се избират състави от чугун или стомана, които са по-устойчиви на алуминий. Например, сивите чугуни са по-устойчиви, ако съдържат повече графит и той е в силно разклонена форма. Силицият в чугуна (както и силиция в стопилката) допринася за взаимодействието на метала с материала на тигела, поради което се стремят да намалят съдържанието му в чугуна до долната граница, а алуминият (1,2–3,0% ) се използва като графитизиращ елемент по време на топене. Алуминият освен това намалява окисляемостта на тигела отвън. Съдържанието на манган трябва да бъде сведено до минимум. Тигелите, изработени от чугун със съдържание на алуминий до 8% и с добавки от хром (0,4-1,0%), както и никел и молибден, имат висока устойчивост.
- При топене върху свежи шихтови материали и лигатури първо се зарежда алуминият (изцяло или частично), а след това лигатурите се разтварят.
- Ако топенето се извършва върху предварителна сплав на слитък или слитък силумин, сплавите на слитъци първо се зареждат и стопяват, а след това сплавта се зарежда с необходимото количество алуминий и основни сплави.
- Метали, силно податливи на отпадъци, като цинк, магнезий, се въвеждат в сплавта последни, за предпочитане под слой флюс.
- Ако шихтата се състои от отпадъци и слитъци метали, последователността на зареждане се определя от броя на компонентите на шихта: на първо място, най-голямата част от шихта се зарежда в пещта и се разтопява. Ако обаче отпадъците са силно замърсени, по-добре е първо да се стопят, дегазират и след това да се заредят слитъкът.
- Ако капацитетът на пещта и размерите на заряда ви позволяват да зареждате различните й компоненти едновременно, тогава заедно те зареждат нещо, което има близка точка на топене, например силумин, отпадъци, алуминиеви блокове. Сместа се избира с най-малко количество примеси за дадена сплав. Полагането на заряда в пещта трябва да се извършва компактно, топенето трябва да се извършва бързо. Когато се зарежда в течна баня, твърдият заряд трябва да бъде предварително загрят.
Зарядните материали и връщанията трябва да се съхраняват в сухи и топли помещения. Съхранението им във влажни помещения или на открито води до адсорбция на влага и повишено окисляване.
Зареждането обикновено се състои от отпадъци и 20-60% от пресни материали, внимателно претеглени в съответствие с изчислените данни. Изчисляването на заряда на отляти алуминиеви сплави се извършва според данните на GOST (според средния или оптималния състав). В зависимост от характеристиките на сплавите и изискванията към свойствата на отливката, съставът на някои компоненти се изчислява по минималното количество, други - по максималното, а третите компоненти се изчисляват по средното количество.
Например, при изчисляване на таксата за приготвяне на блокове от алуминиеви сплави AK4, AK5, AK6 и D16, съдържанието на мед в сплавите се взема според горната граница, което помага да се намали склонността на сплавите към напукване, а съдържанието на желязо, магнезий и силиций се взема, напротив, според долната граница, за да се намали сегрегацията.
Сплав AL4 има следните ограничения химичен съставпо GOST: 8-10,5% Si, 0,25-0,5% Mn, 0,17-0,3% Mg, останалото Al. Обикновено изчислението се извършва при съдържание на силиций 8,25-9,25%. Приема се намалено в сравнение със средното (9,25%) съдържание на силиций, тъй като спомага за повишаване на якостта, намаляване на концентрираното свиване и сегрегация на сплавта. Но прекомерното намаляване на силиция води до намаляване на течливостта и механичните свойства, което е особено важно при леене на тънкостенни части. Следователно в такива случаи изчислението се извършва при съдържание на силиций от 9,25%. Манганът се въвежда в сплавта AL4 главно за елиминиране на вредното въздействие на желязото, но повишеното съдържание на манган може да причини тежка сегрегация. Следователно, ако зарядът е относително чист по отношение на желязото, тогава изчислението се основава на средното съдържание на манган (0,37%), а ако зарядът е силно замърсен, тогава количеството манган се коригира до 0,45%, т.е. до горната граница. Особено важно е при приготвяне на заряда от сплав AL4 да се вземе предвид влиянието на магнезия върху механични свойстватази сплав. Когато съдържанието на магнезий е на долната граница, сплавта ще има намалена якост и твърдост, но висока пластичност.
Често при избора на оптимален състав на сплав е необходимо да се вземе предвид влиянието на няколко компонента върху свойствата на сплавта едновременно и след това да се изберат най-удобните комбинации от тях. Например, сплав D19 (3,8-4,3% Cu; 1,8-2,3% Mg) има високи топлоустойчиви свойства, ако общото количество мед и магнезий в сплавта е 6,1%, което е необходимо да се вземе предвид при изчисляване на заряда. При топене на сплав AL19 (4,5-5,3% Cu, 0,6-1,0% Mn, 0,25-0,35% Ti,<0,3% Fe, <0,3% Si, 0,05% Mg, остальное Al) высокие прочностные и пластические свойства получаются в том случае, когда содержание меди и марганца находятся на среднем уровне марочного состава сплава (5% Cu, 0,8% Mn,0 3% Ti, остальное Al). Любые отклонения от среднего содержания этих металлов неблагоприятно сказываются на механических свойствах.
Ето защо, когато се топят някои алуминиеви сплави (особено многокомпонентни), понякога е необходимо първо да се подготви подготвителна сплав с определен химичен състав от чисти метали, да се излее в блокове, да се анализира съставът и след това, в зависимост от определения състав, използвайте го като начален заряд за приготвяне на работната сплав, директно за изливане на форми.
Стандартните сплави, чиято технология на топене е доста добре развита, обикновено се приготвят еднократно от материали за зареждане и металът веднага се излива във форми.
Топенето на сместа е принудително, но не се препоръчва прегряване на стопилката. Ако зарядът е малък, за да се предпази от прекомерно окисляване, топенето се извършва с помощта на покривни флюсове от смес от хлоридни соли, които се зареждат заедно с металния заряд в количество 2-3% от теглото на метални. При достигане на необходимото прегряване металът се контролира чрез технологични проби за насищане с газ и замърсяване с оксидни включвания и при необходимост се започва рафинирането и дегазирането на сплавта. По време на стопилката, като се започне с приготвянето на шихтовите материали, е необходимо да се предотврати прекомерно окисление и насищане с газ на стопилката. За да направите това, е необходимо внимателно да подготвите заряда за топене и да го почистите от примеси, както и да поддържате пещта и всички инструменти чисти. Колкото повече внимание и време се отделят на подготовката на шихта и пещта, толкова по-малко оксиди и газове ще бъдат в стопилката и толкова по-лесно ще бъде рафинирането на стопилката преди изливането. Небрежното топене, в случай че се използва замърсен, мокър заряд, не изсушава облицовката на пещта (изчислена за последващо почистване на стопилката в резултат на рафиниране и дегазиране в края на стопилката), не дава добри резултати, тъй като често е по-лесно да се предотврати навлизането на оксиди в стопилката и газовете, преди да се отървете от тях.
Практиката на топене на алуминиеви сплави показва, че има пряка връзка между количеството оксидни филми в стопилката и нейното насищане с газ. Колкото повече оксидни филми в сплавта, толкова по-високо е насищането с газ. Следователно трябва да се избягва прекомерното смесване на стопилката, особено ако топенето се извършва без покривни флюсове.