Cum să topești aluminiul acasă. Turnare de investiții. Temperaturile solidus și lichidus ale aliajelor de aluminiu.
Majoritatea de topire aliaje de aluminiu nu este dificil.Componentele de aliere, cu excepția magneziului, zincului și uneori a cuprului, sunt introduse sub formă de ligături.La topirea unor porțiuni mici de aliaje turnate în cuptoare cu creuzet, de regulă, nu se folosesc fluxuri de protecție. Operațiunea obligatorie este rafinarea din incluziuni nemetalice și hidrogen dizolvat. Cele mai greu de topit sunt aliajele aluminiu-magneziu și multicomponent rezistente la căldură.
La topirea aliajelor forjate, se acordă o atenție deosebită curățării cuptorului de zgură și captivității din topitura anterioară. La trecerea la o altă marcă de aliaj, cu excepția topiturii de tranziție, cuptorul și mixerele sunt spălate pentru a îndepărta resturile vechiului aliaj. Cantitatea de metal pentru spălare ar trebui să fie de cel puțin un sfert din capacitatea cuptorului. Temperatura metalului în timpul spălării este menținută la 40-50°C peste temperatura de turnare a aliajului înainte de spălare. Pentru a accelera curățarea, metalul din cuptor este amestecat intens timp de 8-10 minute. Pentru spălare se folosește aluminiu sau retopire.În cazurile în care metalul este scurs complet din cuptor, se poate limita la spălarea cu fluxuri. Topirea aliajului se realizează sub flux
Materialele de incarcare se incarca in urmatoarea succesiune: lingou de aluminiu, deseuri voluminoase, topire, ligaturi (metale pure). Este permisă încărcarea așchiilor uscati și a resturilor de dimensiuni mici în metal lichid la o temperatură care nu depășește 730 ° C. Cuprul este introdus în topitură la o temperatură de 740-750 °C, siliciu - la 700-740 °C folosind un clopot. Zincul este încărcat înainte de magneziu, care este introdus de obicei înainte ca metalul să fie drenat. Supraîncălzirea maximă admisă pentru aliajele turnate este de 800-830 "C, iar pentru aliajele forjate 750-760 °C.
Când este topit în aer, aluminiul se oxidează. Principalii agenți oxidanți sunt oxigenul și vaporii de apă. În funcție de temperatura și presiunea acestor gaze, precum și de condițiile cinetice de interacțiune, oxidul de aluminiu Al2O3, precum și Al2O și AlO, se formează ca urmare a oxidării aluminiului. Probabilitatea formării crește odată cu creșterea temperaturii și scăderea presiunii parțiale a oxigenului în sistem. În condiții normale de topire, faza stabilă termodinamic este oxidul de aluminiu solid γ-Al2O3, care nu se dizolvă în aluminiu și nu formează cu acesta compuși cu punct de topire scăzut. Când este încălzit la 1200 °C, γ-Al2O3 recristalizează în α-Al2O3. În timpul oxidării, pe suprafața aluminiului solid și lichid se formează un film de oxid dens, durabil, cu o grosime de 0,1–10 µm, în funcție de temperatură și timpul de expunere. Când se atinge această grosime, oxidarea se oprește practic, deoarece difuzia oxigenului prin peliculă încetinește brusc.
Procesul de oxidare a aliajelor lichide de aluminiu este foarte complex și insuficient studiat. Datele disponibile din literatura de specialitate arată că intensitatea oxidării componentelor aliajului este o funcție de presiunea oxigenului, presiunea de disociere a oxizilor acestora, concentrația componentelor din aliaj, viteza de difuzie a atomilor către atomii de oxigen, interacțiunea dintre oxizi între ei etc. Cinetica oxidării este determinată de continuitatea, densitatea și rezistența filmelor de oxid. La aceeași concentrație se oxidează în primul rând elementele cele mai active, în care formarea de oxid este asociată cu cea mai mare scădere a potențialului izobar-izoterm.
Majoritatea elementelor de aliere (cupru, siliciu, mangan) nu au un efect semnificativ asupra procesului de oxidare a aluminiului și asupra proprietăților protectoare ale peliculei de oxid, deoarece au un raport de VMem0/mVMe≥1. Filmul de oxid de pe aliajele binare de aluminiu cu aceste elemente la concentrația lor scăzută este format din γ-Al2O3 pur. La conținuturi semnificative ale acestor elemente, se formează soluții solide de oxizi ai elementelor de aliere în γ-Al2O3 și spinelele corespunzătoare.
Metalele alcaline și alcalino-pământoase (potasiu, sodiu, bariu, litiu, calciu, stronțiu, magneziu), precum și zincul (0,05-0,1%) cresc foarte mult oxidabilitatea aluminiului. Motivul pentru aceasta este structura liberă și poroasă a oxizilor acestor elemente. Filmul de oxid de pe topiturile duble în acest caz este îmbogățit cu oxizi ai metalelor alcaline și alcalino-pământoase. Pentru a neutraliza efectele nocive ale zincului, în topiturile de aluminiu se introduce 0,1-0,15% Mg.
Aliajele de aluminiu cu magneziu formează o peliculă de oxid de compoziție variabilă. Cu un conținut scăzut de magneziu de 0,005% (în masă) - pelicula de oxid are structura γ-Al2O3 și este o soluție solidă de MgO în γ-Al2O3; la un continut de 0,01-1,0% Mg, pelicula de oxid este formata din spinel (MgO*Al2O3) de compozitie variabila si cristale de oxid de magneziu; la un conținut de peste 1,5% Mg, pelicula de oxid constă aproape în întregime din oxid de magneziu.
Beriliul și lantanul încetinesc oxidarea aliajelor de aluminiu. Adăugarea de 0,01% beriliu sau lantan reduce rata de oxidare a aliajelor de Al-Mg la nivelul de oxidare a aluminiului. Efectul protector al acestor elemente se explică prin compactarea peliculei de oxid prin umplerea porilor formați cu oxizi de beriliu și lantan.
Fluorul și fluorurile gazoase (SiF4, BF3, SF6 etc.) prezente în atmosfera cuptorului într-o cantitate de până la 0,1% (în greutate) reduc foarte mult oxidabilitatea topiturii de aluminiu. Fiind adsorbite pe suprafața peliculei de oxid, acestea reduc rata de penetrare a oxigenului pe suprafața metalică.
Amestecarea topiturii în timpul procesului de topire este însoțită de o încălcare a integrității filmului de oxid și amestecarea fragmentelor sale în topitură.Îmbogățirea topiturii cu incluziuni de oxid are loc și ca rezultat al reacțiilor de schimb cu căptușeala de dispozitivele de topire. Cea mai semnificativă influență asupra gradului de contaminare a topiturii cu pelicule este exercitată de oxidarea la suprafață a materialelor inițiale de încărcare primară și secundară. Rolul negativ al acestui factor crește pe măsură ce compactitatea scade și suprafața specifică a materialului crește.
Filmul de oxid de sarcină este, de asemenea, o sursă de saturație a topiturii cu hidrogen, deoarece 30-60% constă din Al(OH)3. Umiditatea legată chimic este îndepărtată cu greu de pe suprafața materialelor de încărcare chiar și la o temperatură de 900 C. Hidroxidul, care intră în topitură, o saturează puternic cu hidrogen. Din acest motiv, nu este de dorit să se introducă în încărcătură așchii, rumeguș, tunsoare, îmbinări și alte deșeuri necompacte. O importanță deosebită este organizarea depozitării și procesării la timp a deșeurilor și returnarea producției proprii, prevenind oxidarea și coroziunea cu formarea de hidroxizi. Introducerea retururilor proprii în sarcină este asociată și cu acumularea inevitabilă în aliaje a unei impurități nocive a fierului, care formează compuși intermetalici duri complecși cu componentele aliajelor, care reduc proprietățile plastice și înrăutățesc prelucrarea pieselor turnate prin tăiere.
Alături de oxizi și compuși intermetalici, în topitură pot fi prezente și alte incluziuni nemetalice, cum ar fi carburi, nitruri și sulfuri. Cu toate acestea, cantitatea lor este mică în comparație cu conținutul de oxizi. Compoziția de fază a incluziunilor nemetalice din aliajele de aluminiu este diversă. În plus față de oxizii de aluminiu, aceștia pot conține oxid de magneziu (MgO), spinel de magneziu (MgAl2O4), aluminiu, magneziu, nitruri de titan (AlN, Mg3N2, TiN), carbură de aluminiu (Al4C3), boruri de aluminiu și titan (AlB2, TiB2) și etc. Cea mai mare parte a incluziunilor sunt oxizi.
În funcție de origine, incluziunile nemetalice găsite în aliaje pot fi împărțite în două grupe: incluziuni dispersate și pelicule.Majoritatea incluziunilor dispersate are o dimensiune de 0,03-0,5 microni. Sunt distribuite relativ uniform în volumul topiturii. Grosimea cea mai probabilă a filmelor de oxid este de 0,1-1,0 microni, iar lungimea este de la zecimi de milimetru până la câțiva milimetri. Concentrația unor astfel de incluziuni este relativ scăzută (0,1-1,0 mm2/cm2), iar distribuția este extrem de neuniformă. Când topiturile stau, incluziunile mari pot pluti sau precipita. Cu toate acestea, datorită suprafeței specifice mari a filmelor și a diferenței mici dintre densitatea acestora și densitatea topiturii, plutirea (depunerea) are loc lent, majoritatea filmelor rămân în topitură și sunt transportate în turnare atunci când matrița este umplut. Suspensiile fin dispersate se separă și mai încet. Aproape toți intră în casting.
În timpul topirii, aluminiul este saturat cu hidrogen, al cărui conținut poate ajunge la 1,0-1,5 cm3 la 100 g de metal. Principala sursă de hidrogen este vaporii de apă, a căror presiune parțială în atmosfera cuptoarelor de topire a gazelor poate ajunge la 8-16 kPa.
Efectul elementelor de aliere și al impurităților asupra solubilității de echilibru a hidrogenului în aluminiu a fost puțin studiat. Se știe că cuprul și siliciul reduc solubilitatea hidrogenului, în timp ce magneziul o mărește. Solubilitatea hidrogenului este crescută și de toate elementele de hidroformare (titan, zirconiu, litiu, sodiu, calciu, bariu, stronțiu etc.) Astfel, un aliaj de aluminiu cu 2,64% Ti poate elibera până la 25 cm3 de hidrogen la 100 g. , și un aliaj de aluminiu cu 5 % Zr - 44,5 cm3 la 100 g. Metalele alcaline și alcalino-pământoase (sodiu, litiu, calciu, bariu) care formează hidruri cresc cel mai activ solubilitatea hidrogenului și a aluminiului.
O proporție semnificativă de hidrogen dizolvat în aliaje este gazul introdus de aliajele principale și cuprul electrolitic.De exemplu, aliajul principal aluminiu-titan, în funcție de tehnologia de topire, poate conține până la 10 cm3 de hidrogen la 100 g, iar cuprul electrolitic cu acumulări - până la 20 cm3 la 100 g. Aliajele turnate conțin mai multe impurități și incluziuni nemetalice decât aliajele forjate. Prin urmare, sunt mai predispuși la absorbția gazelor.
Cinetica procesului de hidrogenare a topiturii de aluminiu este limitată de transferul de masă al hidrogenului în metalul lichid, prin filmul de oxid de suprafață și în mediu gazos. Compoziția aliajului și conținutul de incluziuni nemetalice, care determină permeabilitatea filmului de oxid, mobilitatea de difuzie a hidrogenului și posibilitatea eliberării acestuia din topitură sub formă de bule, au cel mai semnificativ efect asupra transferului de masă. . Compoziția mediului gazos are, de asemenea, un efect semnificativ asupra permeabilității filmului. Mobilitatea de difuzie a hidrogenului în aluminiu este redusă de cupru, siliciu și în special magneziu, mangan și titan. Incluziunile nemetalice fin dispersate, având o capacitate mare de adsorbție a hidrogenului, încetinesc puternic mobilitatea difuziei acestuia în topiturile de aluminiu.
Filmul de oxid de aluminiu are o permeabilitate scăzută pentru atomii de hidrogen, încetinește reacția de interacțiune a topiturii cu umiditatea atmosferică. La o grosime a filmului de 1–10 µm, schimbul de gaze între metal și atmosferă se oprește practic. Compoziția aliajului are o mare influență asupra permeabilității filmului. Toate elementele care cresc oxidabilitatea aluminiului (magneziu, litiu, sodiu, stronțiu, calciu) cresc permeabilitatea peliculei de oxid pentru hidrogen. Elementele de aliere (cupru, zinc, siliciu) au un efect redus asupra schimbului de gaze. Ele slăbesc oarecum pelicula de oxid și, prin urmare, contribuie la o saturare mai rapidă a aliajelor cu hidrogen.
Compoziția atmosferei deasupra topiturii afectează în mod semnificativ permeabilitatea la hidrogen a peliculei de oxid. Permeabilitatea filmului crește semnificativ dacă în mediul gazos sunt prezenți Cl2, C2Cl6, BF4, SiF4, freoni și alte halogenuri. Clorurile, cu o mare afinitate pentru aluminiu, sunt adsorbite, pătrund sub pelicula de oxid și o distrug ca urmare a formării clorurii de aluminiu gazoase. Fluorurile interacționează mai puțin activ cu aluminiul. Interacționând cu filmul de oxid, ele contribuie la deshidratarea suprafeței sale și la desorbția moleculelor și atomilor de oxigen. Având o capacitate mare de adsorbție, fluorurile ocupă locurile active eliberate pe film și creează complexe de oxifluoruri de tip Al2O2F2, care opresc accesul oxigenului și vaporilor de apă la topitură, fac filmul subțire și permeabil la hidrogen. Fluxurile lichide care conțin fluoruri distrug, de asemenea, pelicula de oxid și facilitează degazarea topiturii.
Hidrogenul dizolvat, eliberat în timpul cristalizării topiturii, determină formarea porozității de contracție a gazului și a gazului în piese turnate. Odată cu creșterea concentrației de hidrogen, porozitatea gazului a pieselor turnate crește. Predispoziția aliajelor de aluminiu la porozitatea gazului este determinată de gradul de suprasaturare a soluției solide cu hidrogen, care este exprimat ca raport Stp=Szh. Gradul de suprasaturare al soluției solide crește odată cu creșterea vitezei de răcire.
Pentru fiecare aliaj, există concentrații limită de hidrogen, sub care porii de gaz nu se formează în piese turnate la viteze de răcire date. Deci, de exemplu, pentru a preveni formarea porilor de gaz în timpul solidificării pieselor turnate cu pereți groși dintr-un aliaj de Al - 7% Si, conținutul de hidrogen din topitură nu trebuie să depășească 0,15 cm3 la 100 g. Hidrogenul limită conţinutul în duralumini este de 0,12-0, 18 cm3 la 100 g în funcţie de intensitatea răcirii în timpul cristalizării.
Protecția topiturii de aluminiu de oxidare și absorbția hidrogenului se realizează prin topirea sub flux într-o atmosferă ușor oxidantă. Ca flux de acoperire în topirea majorității aliajelor care conțin nu mai mult de 2% Mg, se utilizează un amestec de cloruri de sodiu și potasiu (45% NaCl și 55% KCl) într-o cantitate de 1-2% din greutatea încărcăturii. Compoziția fluxului corespunde unei soluții solide cu un punct de topire minim de 660 °C. În acest scop, se recomandă și un flux mai complex (Tabelul 12).
Pentru aliajele de aluminiu-magneziu se folosesc ca flux de acoperire carnalitul (MgCl2 * KCl) și amestecurile de carnalită cu 40-50% clorură de bariu sau 10-15% fluorură de calciu. Dacă utilizarea fluxului nu este posibilă, protecția împotriva oxidării se realizează prin introducerea de beriliu (0,03-0,05%). Fluxurile de protecție sunt utilizate pe scară largă în topirea aliajelor în cuptoare cu reverberație.
Pentru a preveni interacțiunea cu umiditatea, se iau măsuri de îndepărtare a acesteia de căptușeala cuptoarelor de topire și a dispozitivelor de turnare, de rafinarea și modificarea fluxurilor; instrumentul de topire și turnare este supus calcinării și colorării, materialele de încărcare sunt încălzite, curățate și uscate.
Cu toate acestea, indiferent de cât de atent este protejată topitura, atunci când este topită în aer, se dovedește întotdeauna contaminată cu oxizi, nitruri, carburi, incluziuni de zgură și flux, hidrogen, prin urmare, trebuie curățată înainte de turnare în matrițe.
Rafinare prin topire
Pentru curățarea aliajelor de aluminiu de incluziuni nemetalice în suspensie și hidrogen dizolvat, se folosesc decantarea, purjarea cu gaze inerte și active, tratarea cu săruri și fluxuri clorurate, evacuarea, filtrarea prin plasă și filtre granulare și rafinarea cu electroflux.
Ca proces independent, decantarea poate fi aplicată în cazurile în care diferența de densitate este suficient de mare și dimensiunea particulelor nu este prea mică. Ho și în aceste cazuri procesul este lent, este necesar consum crescut combustibil și se dovedește a fi ineficient.
Purificarea topiturii prin suflare cu gaze inerte sau active se bazează pe apariția a două procese de difuzie a gazului dizolvat în bule, acțiunea suflată și flotantă a bulelor în raport cu incluziunile și a celor mai mici bule de gaz. Rafinarea este realizată cu mai mult succes, cu atât dimensiunea bulelor de gaz suflat este mai mică și distribuția lor este mai uniformă pe volumul topiturii. În acest sens, metoda de prelucrare a topiturii merită o atenție deosebită. gaze inerte folosind inserții ceramice poroase. În comparație cu alte metode de introducere a gazelor inerte în topituri, suflarea prin inserții poroase este cea mai eficientă.
Epurarea topiturii cu gaze este utilizată pe scară largă în turnătorii pentru producerea de lingouri. Se realizează în cutii speciale căptușite instalate pe traseul preaplinului de metal de la mixer la matriță. Pentru rafinarea topiturii de aluminiu se utilizează azot, argon, heliu, clor și amestecul acestuia cu azot (90%), purificat de umiditate și oxigen.
Purjarea cu azot sau argon se efectuează la 720-730 °C. Durata suflarii, in functie de volumul topiturii, variaza intre 5-20 de minute; consumul de gaz este de 0,3-1% din masa topiturii. O astfel de prelucrare permite reducerea conținutului de incluziuni nemetalice la 1,0-0,5 mm2/cm2 conform eșantionului tehnologic al V.I. Dobatkin și BK. Zinoviev, iar conținutul de hidrogen este de până la 0,2-0,15 cm3 la 100 g de metal.
Tratarea topiturii cu clor se efectuează în camere închise sau oale cu capac cu gaze de evacuare în sistemul de ventilație. Clorul este introdus în topitură prin tuburi cu duze la 710-720 °C. Durata rafinării la o presiune a clorului de 108-118 kPa este de 10-12 minute; consumul de clor - 0,2-0,8% din greutatea topiturii. Utilizarea clorului asigură un nivel mai ridicat de purificare în comparație cu azotul tehnic și argonul. Cu toate acestea, toxicitatea clorului, necesitatea procesării topiturii în camere speciale și dificultățile asociate cu uscarea acestuia limitează semnificativ utilizarea clorării topiturii în condiții industriale. Înlocuirea clorului cu un amestec de clor și azot (90%) asigură un nivel suficient de ridicat de purificare, dar nu rezolvă problemele asociate cu toxicitatea și uscarea.
Degazarea prin suflare este însoțită de pierderi de magneziu: atunci când este tratată cu azot, se pierde 0,01% din magneziu; atunci când sunt tratate cu clor, aceste pierderi cresc la 0,2%.
Rafinarea cu cloruri este utilizată pe scară largă în producția de modele și turnătorie. În acest scop, se utilizează clorura de zinc, clorura de mangan, hexacloretanul, tetraclorura de titan și o serie de alte cloruri. Datorită higroscopicității clorurilor, acestea sunt supuse uscării (MnCl2, C3Cl6) sau retopirii (ZnCl2). Tehnologia rafinarii cu cloruri consta in introducerea lor in topitura cu agitare continua cu clopot pana la incetarea degajarii produselor gazoase de reactie.Clorurile de zinc si mangan se introduc in cantitate de 0,05-0,2% la temperatura de topire de 700-730. °C; hexacloretan - într-o cantitate de 0,3-0,7% la 740-750 ° C în mai multe etape. Odată cu scăderea temperaturii, eficiența rafinării scade datorită creșterii vâscozității topiturii; rafinarea la temperaturi mai ridicate este nepractică, deoarece este asociată cu oxidarea intensă a topiturii.
În prezent, în magazinele de turnare modelată pentru rafinare se folosesc pe scară largă tabletele din preparatul Degazer, constând din hexacloretan și 10% (în greutate) clorură de bariu, care sunt introduse în topitură fără a folosi „clopote”. Posedând o densitate mai mare decât cea a topiturii, tabletele se scufundă pe fundul recipientului, asigurând prelucrarea întregului volum al topiturii.
Sărurile clorurate interacționează cu aluminiul conform reacției: 3MnCl2 + 2Al → 2AlCl3 + 3Mn.
bule clorura de aluminiu, urcând la suprafaţa topiturii, antrenează incluziuni nemetalice în suspensie; hidrogenul dizolvat în metal difuzează în bule, iar topitura este purificată. După amestecare, topitura este lăsată să se stabilească timp de 10–45 min la 720–730°C pentru a îndepărta micile bule de gaz.
Rafinarea cu cloruri se efectuează în cuptoare sau oale cu o suprafață specifică mică a topiturii. În cuptoarele cu un strat de topire scăzut, rafinarea cu cloruri este ineficientă. În ceea ce privește nivelul de purificare din incluziuni nemetalice și gaze, tratamentul cu cloruri este inferior purjării cu clor.
Purificarea topiturii de aluminiu cu fluxuri este utilizată la topirea aliajelor turnate și forjate. Pentru rafinare se folosesc fluxuri pe bază de săruri clorurate ale metalelor alcaline și alcalino-pământoase cu adaos de săruri de fluorură - criolit, fluoruri, fluoruri de sodiu și potasiu (Tabelul 13).
În practica topirii majorității aliajelor de aluminiu forjat, fluxul nr. 1 este utilizat pentru rafinare.
Pentru curățarea aliajelor de aluminiu cu magneziu se folosesc fluxuri pe bază de carnalit - 80-90% MgCl2 * KCl, 10-20% CaF2, MgF2 sau K3AlF6. Fluxurile pretopite și uscate în cantitate de 0,5-1% din greutatea metalului sunt turnate pe suprafața topiturii la 700-750 °C. Apoi, timp de 3-5 minute, fluxul este frământat energic în topitură, zgura este îndepărtată și topitura este lăsată să se depună timp de 30-45 de minute. După îndepărtarea repetată a zgurii, topitura este folosită pentru umplerea formelor. La prelucrarea unor volume mari de metal, fluxul este introdus pe fundul topiturii folosind un „clopot”.
Fluxurile nr.2 si 13 sunt utilizate pe scara larga pentru rafinarea aliajelor de aluminiu turnat (silicine), se introduc in topituri sub forma lichida in cantitate de 0,5-1,5% (din greutate) si se framanta energic. Ele contribuie la distrugerea spumei formate în timpul umplerii oalelor de distribuire și îmbogățesc topiturile cu sodiu.
In timpul aspirarii se obtine un nivel ridicat de degazare.Această metodă de curățare este utilizată în principal în turnătoriile de modă. Esența sa constă în faptul că metalul topit conform tehnologiei standard în cuptoarele convenționale este turnat într-o oală, care este apoi plasată într-o cameră cu vid. Metalul din cameră se menține la o presiune reziduală de 1330 Pa timp de 10-30 minute; temperatura de topire este menținută în intervalul 720-740 °C. În cazurile în care evacuarea se efectuează fără încălzire, topitura este supraîncălzită la 760-780 °C înainte de prelucrare. Dispunerea instalației de degazare în vid este prezentată în fig. 93.
ÎN anul trecut pentru a curăța topiturile de aluminiu de incluziuni nemetalice, filtrarea prin plasă, filtre ceramice granulare și poroase este din ce în ce mai utilizată la scară largă. Filtrele cu plasă sunt utilizate pe scară largă pentru a curăța topiturile de incluziuni și pelicule mari.Separă acele incluziuni a căror dimensiune este mai mare decât celula de plasă. Pentru fabricarea filtrelor cu plasă, se utilizează pânză de sticlă de diferite mărci cu dimensiuni ale celulelor de la 0,5x0,5 până la 1,5x1,5 mm și plase metalice (din titan). Filtrele din fibră de sticlă sunt instalate în cutii de joncțiuneși matrițe, în canale de deschidere și creuzete de distribuție (Fig. 94), utilizarea lor face posibilă reducerea conținutului de incluziuni și pelicule nemetalice mari de 1,5-2 ori; nu afectează conținutul de incluziuni dispersate și hidrogen.
Filtrele granulare oferă un efect de curățare mult mai mare. Caracteristica lor distinctivă este o suprafață mare de contact cu metalul și prezența unor canale lungi și subțiri cu secțiune transversală variabilă. Purificarea topiturii de metal din incluziunile suspendate în timpul filtrării prin filtre granulare se datorează proceselor mecanice și adezive. Primul dintre ele joacă un rol decisiv în separarea incluziunilor mari și a filmelor, al doilea - în separarea incluziunilor fin dispersate. Datorită efectului de grilă, filtrele granulare rețin doar acele incluziuni a căror dimensiune depășește diametrul efectiv al canalelor intergranulare. Cu cât diametrul granulelor de filtrare este mai mic și cu cât împachetarea acestora este mai densă, cu atât nivelul atins de purificare a topiturii din incluziuni și pelicule mari este mai mare (Fig. 95).
Odată cu creșterea grosimii stratului filtrant, eficiența curățării crește. Filtrele umectabile prin topire sunt mai eficiente decât cele care nu sunt umectabile.
Filtrele dintr-un aliaj de fluoruri de calciu si magneziu fac posibila obtinerea de piese turnate din aliaje AL4, AK6 si AMg6 de 1,5-3 ori mai putin contaminate cu incluziuni mari decat filtrele de magnezit.
Viteza și regimul curgerii topiturii prin canalele intergranulare ale filtrului au un efect semnificativ asupra completității separării incluziunilor și filmelor mari. Odată cu creșterea vitezei, scade posibilitatea de sedimentare a incluziunilor dintr-un flux în mișcare sub acțiunea gravitației și probabilitatea de a spăla incluziunile deja sedimentate ca urmare a acțiunii hidrodinamice, al căror grad este proporțional cu pătratul filtrării. rata, crește.
Eficiența purificării topiturii de aluminiu din incluziuni fine prin filtre granulare crește pe măsură ce umezirea filtrului și incluziunile din topitură se deteriorează.
La fabricarea filtrelor se folosesc argila refractară, magnezitul, alundum, silice, aliaje de săruri de clorură și fluor și alte materiale. Completitudinea îndepărtării incluziunilor nemetalice în suspensie depinde de natura materialului filtrant. Cele mai eficiente filtre sunt cele realizate din fluoruri (materiale active) (Figurile 95 și 96).
Materialele active, împreună cu incluziuni și pelicule mari, fac posibilă separarea a până la 30–40% din suspensiile fin dispersate și reducerea conținutului de hidrogen din aliajele care au fost rafinate cu flux sau cloruri cu 10–20%. Pe măsură ce suspensiile fine sunt îndepărtate, dimensiunea granulelor din piese turnate crește, conținutul de gaz scade, proprietățile plastice ale aliajelor cresc (Fig. 97) 6 mm în diametru și o înălțime a stratului filtrant de 100-120 mm.
Filtrele granulare, precum și filtrele cu plasă, sunt instalate în calea deplasării metalului din mixer în matriță. În turnarea continuă a lingourilor, matrița este locul optim de instalare; în turnare modelată, filtrul este așezat într-un colț, creuzet de distribuție sau vas de deschidere.
În fig. 98.
Înainte de utilizare, filtrul este încălzit la 700-720 °C pentru a îndepărta umezeala adsorbită și pentru a preveni înghețarea metalului în canale.
Umplerea se realizează în așa fel încât nivelul superior al filtrului să fie acoperit cu un strat de metal de 10-15 mm, iar scurgerea metalului după filtru are loc sub nivelul inundat. În aceste condiții, conținutul rezidual de incluziuni și pelicule nemetalice din turnare poate fi crescut la 0,02-0,08 mm2/cm2 conform eșantionului tehnologic al V.I. Dobatkin și V.K. Zinoviev, adică de 2-4 ori redusă în comparație cu filtrarea prin filtre cu plasă.
Cel mai metoda eficienta purificarea topiturii de aluminiu din pelicule și incluziuni mari nemetalice - rafinare prin electroflux. Esența acestui proces constă în trecerea unor jeturi subțiri de topitură printr-un strat de flux lichid cu impunerea simultană a unui câmp constant sau constant asupra metalului și fluxului. curent alternativ care creează mai mult conditii favorabile pentru adsorbţia incluziunilor prin flux ca urmare a scăderii tensiunii interfaciale la interfaţa cu metalul. Odată cu creșterea suprafeței specifice și a duratei de contact a metalului cu fluxul, eficiența curățării crește. Prin urmare, modelele dispozitivelor de rafinare cu flux și electroflux prevăd zdrobirea cu jet (Fig. 99).
Modul optim de rafinare prin electroflux presupune trecerea unui jet de metal cu diametrul de 5-7 mm, încălzit la 700-720°C, printr-un strat de flux topit gros de 20-150 mm cu aplicarea unui câmp. curent continuu putere 600--800 A si tensiune 6-12 V cu polarizarea catodica a metalului. La un consum de flux (carnalit cu 10-15% CaF2, MgF2 sau K3AlF6 pentru aliaje Al - Mg și Al - Mg - Si și criolit pentru alte aliaje de aluminiu) 4-8 kg la 1 tonă de topitură și îndepărtarea atentă a umidității din dispozitive de flux și turnare, conținutul de incluziuni mari nemetalice din aliajele AK6, AMg6, V95 poate fi redus la 0,003-0,005 mm2/cm2 conform eșantionului tehnologic.
Spre deosebire de filtrele granulare, rafinarea cu electroflux nu afectează macrostructura aliajelor, ceea ce indică o eficiență mai scăzută a acesteia în curățarea de incluziuni nemetalice dispersate.
Aliajele forjate si turnate sunt, de asemenea, supuse rafinarii din impuritatile metalice: sodiu, magneziu, zinc si fier.
Îndepărtarea sodiului din aliajele forjate de aluminiu și aluminiu-magneziu AMg2, AMg6 se realizează prin suflarea topiturii cu vapori de clor sau clorură (C2Cl6, CCl4, TiCl4), freon (CCl2F2) și filtrarea prin filtre granulare AlF3 cu granulație de 4-6 mm. Utilizarea acestor metode face posibilă aducerea conținutului de sodiu rezidual în topitură până la 2/3*10-4%. Efectul nociv al sodiului asupra proprietăților tehnologice ale aliajului poate fi suprimat prin introducerea în topitură de aditivi de bismut, antimoniu, teluriu sau seleniu, care formează compuși intermetalici refractari cu sodiul.
Aliajele secundare de aluminiu în unele cazuri sunt supuse purificării de impurități de magneziu, zinc și fier prin fluxare, distilare în vid și decantare, urmată de filtrare. Îndepărtarea magneziului prin flux se bazează pe reacția 2Na3AlF6 + 3Mg → 6NaF + 3MgF2 + 2A1. Suprafața topiturii este acoperită cu un flux format din 50% criolit și 50% clorură de sodiu. Apoi aliajul este încălzit la 780-800 °C și amestecat intens împreună cu fluxul timp de 10-15 minute. Produșii de reacție care au plutit la suprafața topiturii sunt îndepărtați; cu un continut ridicat de magneziu (1-2,5%), procesul de rafinare se repeta de mai multe ori. Cu ajutorul criolitului, conținutul de magneziu din topitură poate fi redus la 0,1%. Rafinarea aliajelor secundare de aluminiu din magneziu poate fi realizată cu succes cu un flux format din 50% Na2SiF6, 25% NaCl și 25% KCl. În aceste scopuri, pot fi utilizate fluxuri care conțin oxigen, cum ar fi cloratul de potasiu (KClO3).
Purificarea topiturii din magneziu și zinc se realizează în cuptoare de distilare în vid la 950-1000°C. Ca urmare a unei astfel de procesări, se obțin aliaje care conțin 0,1-0,2% Mr și 0,02-0,05% Zn. Purificarea topiturii din magneziu prin distilare se realizează în cazurile în care conținutul său în aliaj este ridicat și utilizarea curățării cu flux devine neprofitabilă.
Decantarea poate reduce conținutul de fier din aliajul de aluminiu la 1,7%, adică aproape până la conținutul eutectic, conform diagramei de stare de echilibru aluminiu-fier. Reducerea suplimentară se realizează prin combinarea procesului de decantare cu introducerea în aliaj de crom, mangan sau magneziu.Adăugarea acestor elemente deplasează punctul eutectic către aluminiu și contribuie la separarea fierului în exces. Odată cu introducerea a 1-1,5% Mn în topitură, conținutul de fier din aceasta poate fi redus la 0,7%. Aditivul de magneziu în cantitate de 25-30% vă permite să aduceți conținutul de fier la 0,1-0,2%. Procesul de separare a compușilor intermetalici ai fierului este accelerat prin combinarea decantarii cu filtrarea. Filtrarea se realizează printr-un filtru de bazalt încălzit la 700 °C folosind vid. Rafinarea din fier cu magneziu este aplicabilă aliajelor care conțin nu mai mult de 1,0% Si. La un conținut mai mare de siliciu, se formează siliciuri care complică foarte mult filtrarea și elimină o cantitate semnificativă de magneziu din ciclu. În plus, aliajul este sărăcit în siliciu.
Deșeurile de aluminiu și duraluminiu sunt ușor de topit acasă. Și pentru aceasta nu este necesară construirea furnalelor, pentru a crea tracțiune, așa cum este obișnuit în conformitate cu condițiile standard.
Autorul metodei de topire a aluminiului pe o sobă cu gaz folosește ca creuzet o oală din oțel inoxidabil. Punctul de topire al aluminiului este de 660 de grade. Aragaz nu poate asigura o astfel de încălzire. Mai întâi, în 15 minute, creuzetul cu conținutul se încălzește, apoi se aprinde arzător de gaz, care asigură temperatura necesară pentru a topi aluminiul. Cuptoare de topire finiteîn acest magazin.
Atenţie! Nu folosiți un creuzet atât de instabil ca în acest videoclip. Asigurați-vă că utilizați hota, lăsați fereastra deschisă și nu lucrați des acasă cu aluminiu topit.
Ce se poate face folosind astfel de cuptoare de topire? De exemplu, ca și pe site-ul nostru web, puteți realiza un model de arme din aluminiu. Acest lucru necesită spumă, nisip și o topitorie. Apropo, articolul conține și un link către un analog al topitoriei, care este prezentat aici.
Mulți percep termenul „turnătorie” ca ceva asociat cu producția mare și abilitățile și abilitățile profesionale. Dar, de fapt, turnarea unei piese pe cont propriu acasă este realist chiar și pentru umanistul însuși, care nu știe nimic despre tehnica turnării.
Cum să turnați o piesă de aluminiu
Caracteristica metalului
Aluminiul este unul dintre cele mai ieftine, mai comune și disponibile metale, care poate fi ușor prelucrat și turnat. Principalele caracteristici ale aluminiului sunt conductivitatea electrică și termică ridicată, precum și rezistența crescută la coroziune. Punctul de fierbere al acestui metal alb-argintiu este de 2500 °C. Aluminiul pur se topește la 660°C, în timp ce aluminiul tehnic se topește la 658°C. Este puțin probabil ca aparatele de încălzire a locuințelor să poată furniza o astfel de temperatură, așa că este mai bine să folosiți un cuptor cu mufă cu creuzet pentru a turna o piesă de aluminiu.
Cuptor cu mufă și scopul său
Un cuptor cu mufă este un dispozitiv indispensabil pentru încălzirea independentă a diferitelor metale acasă. Un astfel de dispozitiv este capabil să topească nu numai aluminiul, ci și cuprul și multe metale neferoase, precum și uscarea și arderea produselor ceramice.
Tipuri de cuptoare cu mufă
Dispozitivele de mufă pentru topirea metalelor sunt de următoarele tipuri:
- vid;
- aer;
- gaz;
- electric.
Prin proiectare, acestea sunt împărțite în:
- tubular;
- vertical;
- orizontală;
- în formă de clopot.
Cuptorul cu mufă este format dintr-o cameră de încălzire și un acumulator special de căldură.
Faceți un cuptor cu mufă cu propriile mâini
Pentru fabricarea dispozitivului avem nevoie următoarele instrumente și materiale:
- sârmă;
- Bulgară;
- caramida (7 buc.);
- ochelari de protecție;
- ciocan;
- galeata de metal;
- bucată de fier etc.
Etapele construcției unui cuptor:
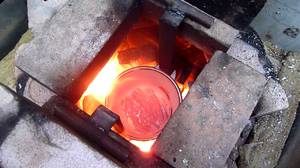
Pentru mai multă funcționalitate, este permis instalarea a doua radiatoare electrice, care poate fi pornit în secvență sau în același timp. De exemplu, pentru lipirea unei cantități mici de materii prime, este pornit doar un încălzitor inferior, iar dacă scara de topire este mare, se folosesc două dispozitive.
Cuptorul cu mufă cu încărcare superioară este foarte compact, ceea ce îi permite să fie depozitat în casa de țară, în garaj sau pe balcon.
Principiul de funcționare al cuptorului este destul de simplu: pe suprafața de lucru a cuptorului este instalat un recipient pentru lipire (crezet) cu materii prime plasate acolo unde este încălzit la temperatura dorită (660 ° C). Metalul încălzit este turnat într-o matriță pregătită în prealabil, care poate fi făcută din ipsos sau alt material incombustibil. Pentru fabricarea formei, se recomandă utilizarea tencuielii albe sau sculpturale, care pot fi achiziționate de la orice magazin de materiale de construcție.
După cum am menționat mai devreme, pentru lipirea aluminiului într-un cuptor nevoie de o găleată specială(crezet), care este realizat dintr-un metal cu un punct de topire mai mare decât cel al aluminiului sau dintr-un material refractar. Pentru fabricarea recipientelor pentru topirea aluminiului, porțelanul, grafitul, corindonul, cuarțul, oțelul sau fonta se folosesc. Găleata poate fi achiziționată de la un magazin specializat sau realizată independent. Mărimea creuzetului este determinată de cantitatea așteptată de materie primă pentru topire.
Metalul trebuie așezat cât mai strâns posibil și presat puțin. Deoarece aluminiul pierde semnificativ volumul în timpul topirii, este necesar să adăugați periodic materii prime în oală.
Important. Materia primă adăugată trebuie să fie absolut uscată, deoarece chiar și o cantitate mică de umiditate care pătrunde în aluminiul fierbinte poate provoca o stropire ascuțită, în urma căreia metalul iese din cuptor și vă poate provoca arsuri grave, mai ales dacă aluminiul topit vă intră în ochi.
Prin urmare, înainte de a începe lucrul, ar trebui să aveți grijă de siguranța dvs.: cumpărați ochelari de protecție sau o mască și este mai bine să obțineți un costum special de metalurgist ignifug.
În procesul de topire a metalului acasă, va apărea o peliculă de oxid pe suprafața aluminiului fierbinte, precum și se formează diverse zguri(vopsea veche, particule de murdărie etc.). Cantitatea sa depinde direct de calitatea materiilor prime. Înainte de a turna metalul topit în matrițe, este necesar să îndepărtați zgura folosind unelte speciale. Apoi se recomandă să păstrați aluminiul în cuptor pentru mai mult timp pentru a face metalul mai fluid. Acest lucru va simplifica foarte mult turnarea ulterioară.
Piese din aluminiu turnăm noi înșine
Luați în considerare cel mai simplu mod de a lipi o piesă acasă.
Noi vom avea nevoie:
- fier vechi;
- oală pentru topire;
- mucegaiuri.
Etapele procesului:
- Pregătiți un recipient pentru topirea aluminiului acasă. În acest scop, puteți folosi o bucată de țeavă de oțel.
- Faceți un formular. Pentru piesele cu o structură complexă, forma poate consta din mai multe elemente. Forma poate fi din ipsos (sculptural). Nu folosiți niciodată alabastru!
- Pentru a evita lipirea gipsului de recipientul pentru formular, trebuie mai întâi să-l ungeți cu ulei.
- În procesul de turnare a gipsului, recipientul trebuie agitat periodic pentru a preveni formarea bulelor.
Important. Deoarece tencuiala se întărește foarte repede, încercați să fixați modelul piesei în tencuială cât mai curând posibil. De asemenea, se recomandă instalarea unui obiect mic (de exemplu, un băț) în ipsos, care va servi drept canal pentru turnarea piesei viitoare.
Pentru mulți, termenul „turnătorie” este strâns asociat cu suprasolicitarea și abilitățile profesionale speciale. De fapt, este realist să turnați o piesă din metalul necesar cel mai mult persoana normala fără antrenament acasă. Procesul are propriile sale subtilități, dar este în puterea de a-l face acasă cu propriile mâini. În exterior, seamănă cu fabricarea greutăților de plumb pentru pescuit. Caracteristicile procesului de turnare a aluminiului sunt asociate cu specificatii tehnice material.
Cum să te piși aaluminiu
caracteristicile aluminiului. Aluminiul este unul dintre cele mai comune metale.
Este de culoare alb-argintiu, se pretează suficient de bine pentru turnare și prelucrare. Datorită caracteristicilor sale, aluminiul este echipat cu o conductivitate termică și electrică ridicată și are și rezistență la coroziune.
Pentru aluminiul tehnic, punctul de topire este de 658 de grade, pentru aluminiul de înaltă puritate - 660, punctul de fierbere al aluminiului este de 2500 de grade.
Pentru turnarea aluminiului, este puțin probabil ca aparatele de încălzire a locuinței să fie utile și să ofere temperatura dorită. Este necesar să topești aluminiul prin încălzirea lui la o temperatură de peste 660 de grade.
Turnare aluminiu: alegerea sursei de căldură
Ca sursă de căldură pentru topirea aluminiului, puteți folosi:
- O metodă foarte eficientă este obținută datorită unui cuptor cu mufă cu creuzet fabricat singur. Un creuzet (un instrument necesar pentru topirea aluminiului) este instalat pe suprafața de lucru a acestui cuptor, i se adaugă materii prime. Cu ajutorul unui cuptor cu mufă, este foarte ușor să turnați aluminiu.
- Pentru a obține punctul de topire al aluminiului, temperatura de ardere a lichefiat sau gaz natural, în acest caz, procesul poate fi efectuat într-un cuptor de casă.
- Cu o cantitate mică de topire, puteți folosi căldura obținută prin arderea gazului într-o sobă de uz casnic pe gaz.
- Temperatura cerută va fi asigurată de tăietoare cu gaz sau generatoare de acetilenă, dacă există în gospodărie.
Prepararea aluminiului
În ciuda faptului că procesul de topire se va desfășura acasă, acesta trebuie luat în mod responsabil. Metalul trebuie mai întâi curățat de murdărie, zdrobit în bucăți mici. În acest caz, procesul de topire va merge mai rapid.
Alegerea se oprește pe aluminiu mai moale, ca material mai pur, cu mai puține impurități. În timpul topirii, zgura este îndepărtată de pe suprafața lichidă a metalului.
Turnare cu nisip
Pentru fabricarea pieselor turnate se folosesc mai multe tehnologii. Cel mai simplu este turnarea cu nisip:
- Dacă este necesară producerea unei piese de aluminiu de formă simplă, atunci turnarea poate fi efectuată printr-o metodă deschisă direct în sol - silice. Ei fac un model mic din orice material: lemn, polistiren. Instalat într-un balon. Pământul este așezat în straturi mici și bătut cu grijă. După ce proba este îndepărtată, silicea își păstrează bine forma și turnarea se face direct în ea.
- Ca amestec de formare, puteți utiliza nisip combinat cu adeziv silicat sau ciment amestecat cu lichid de frână. Raportul dintre materiale ar trebui să fie astfel încât, dacă amestecul este comprimat, să-și păstreze forma.
Video „Turnare de aluminiu într-o matriță de pământ (nisip) acasă”
Pentru detalii formă complexă se utilizează altă tehnologie.
Turnare de investiții
Această metodă cunoscută de mult timp pentru fabricarea produselor din aluminiu acasă poate fi ușor modificată. Principiul turnării este următorul:
Modelul este realizat din material fuzibil. Este așezat într-o anumită formă, turnat cu ipsos. Sunt instalate un canal sau mai multe. După ce tencuiala s-a întărit, se usucă bine. La temperaturi ridicate, materialul fuzibil devine lichid și curge prin canalizare. În matrița rezultată se toarnă o țagle de aluminiu.
Detaliile procesului pot fi clarificate în videoclip.
Video „Turnare de aluminiu de înaltă presiune”
Astfel, chiar și cel mai obișnuit meșter amator poate realiza piesa necesară din aluminiu de diferite forme.
Cum să turnați o formă complexă din aluminiu
În întreprinderile industriale, matrițele metalice sunt adesea folosite. Se pot obține forme de turnare pentru turnarea aluminiului diverse materiale. Cel mai adesea, se folosește gipsul. Gipsul poate fi achiziționat de la orice magazin de feronerie la orice preț îți poți permite. Se recomandă utilizarea tencuielii sculpturale sau albe.
O opțiune excelentă este cea sculpturală, care este marcată G-16. Datorită prețului ridicat, poate fi înlocuit cu G-7 - gips alb obișnuit. Este strict interzisă înlocuirea cu alabastru, în ciuda faptului că acestea sunt în lucrari de constructii adesea interschimbabile.
Să luăm în considerare o modalitate simplă de a turna o piesă de aluminiu cu propriile mâini acasă.
Pentru turnarea unei piese din aluminiu, avem nevoie de:
- vas pentru topire;
- fier vechi;
- matriță pentru topire.
Principalele etape ale procesului:
1. Pregătim un vas pentru topire (puteți folosi un vas dintr-o parte a unei țevi de oțel).
2. Facem o matriță pentru topire. Dacă piesa are o structură complexă, atunci forma poate avea mai multe componente.
În versiunea noastră, formularul va consta din două părți. În primul rând, gândiți-vă cum să simplificați piesa pentru comoditate (recomandăm să întăriți găurile cu bandă).
Forma este foarte ușor de realizat din ipsos sculptural (nu folosiți alabastru!). Puteți folosi plastilină.
3. Înainte de turnarea gipsului, recipientul trebuie lubrifiat cu ulei, astfel încât gipsul să nu se lipească de recipient.
4. Turnați ușor gipsul, agitați periodic matrița pentru a elibera bulele.
Este important de știut: procesul de întărire a tencuielii este destul de rapid, așa că aveți grijă și încercați să instalați modelul în tencuială la timp.
5. Necesită un strat primar pentru turnarea următoare.
Luăm un burghiu și facem 4 găuri mici, procesăm forma cu ulei. Acest lucru este necesar pentru ca părțile finite ale matrițelor să fie cât mai stabile posibil în timpul procesului de turnare.
6. Umplerea celui de-al doilea strat.
7. După ce are loc întărirea, este necesar să scoateți cu grijă matrița din recipient și să separați jumătățile.
8. Înainte de turnare, procesăm matrița cu funingine pentru a evita lipirea aluminiului lichid. Forma trebuie să se usuce. Desigur, procesul de uscare are loc toată ziua. Este recomandabil să uscați semifabricatul de ipsos în cuptor. Începeți la temperatura 11 - o oră și două ore la temperatură 300 C. În tencuială trebuie prevăzute găuri pentru turnarea aluminiului și îndepărtarea aerului rezidual.
În acest fel topim aluminiul.
9. Apoi punem metalul lichid în formă și așteptăm să se răcească complet.
Drept urmare, obținem piesa de prelucrat dorită, apoi o șlefuim și facem găuri speciale.
Burnt-out casting: caracteristici tehnologice
Fabricarea pieselor din aluminiu folosind turnarea arsă are propriile sale caracteristici, care vor fi discutate mai jos. Lucrarea se desfășoară în următoarea secvență:
- Styrofoam este folosit ca material pentru modelul acasă. Folosind elemente de tăiere și lipici, creați o figură care să semene cu forma dorită cu contururi.
- Pregătiți un recipient pentru realizarea unui model. Puteți folosi o cutie veche de pantofi. Se amestecă alabastru cu apă. Turnați amestecul în cutie. Așezați modelul din spumă. Netezi. Lăsați timp materialului să se usuce bine. Datorită procesului rapid de solidificare a alabastrului, lucrați într-un ritm accelerat.
- Scoateți cutia. Încingeți forma în cuptor pentru a usca alabastrul și îndepărtați orice umezeală rămasă. În caz contrar, toată apa din alabastru va intra în aluminiu și se va transforma în abur, ceea ce va duce la pori din metal și stropirea aluminiului din matriță în timpul lucrului.
- Topiți aluminiul. Îndepărtați zgura topită de pe suprafața lichidului. Turnați metalul în matriță în locul spumei. Din temperatura ridicata acesta din urmă va începe să se ardă și aluminiul îi va lua locul.
- După ce metalul s-a răcit, spargeți matrița și îndepărtați modelul rezultat din aluminiu turnat. Puteți vedea procesul mai detaliat în videoclip.
Siguranta si pregatirea locului de munca
Lucrările la temperaturi ridicate se caracterizează prin vapori nocivi și sunt însoțite de degajarea de fum, astfel încât acestea trebuie efectuate în aer liber sau într-o încăpere ventilată forțat. Trebuie folosit un ventilator lateral.
Procesul de turnare este însoțit de stropi, sunt posibile curgeri de metal topit. La locul de muncă va trebui mai întâi să-l acoperiți cu o foaie de metal. Nu este recomandat să efectuați lucrări într-o zonă rezidențială - este nesigur pentru alții.
Principalele greșeli în turnarea aluminiului
Înainte de a efectua turnarea de aluminiu acasă, acordați atenție principalelor greșeli care sunt observate în timpul lucrării:
- La fabricarea matrițelor de ipsos, este necesar ca toată umezeala să se evapore în timpul procesului de uscare. În caz contrar, la umplerea formularului, apa începe să se evapore, se transformă în abur și poate rămâne în interiorul aluminiului sub formă de pori și cochilii.
- Cu o încălzire insuficientă sau dacă aluminiul s-a răcit înainte de a începe lucrul, metalul nu va umple bine matrița și zonele îndepărtate vor rămâne goale.
- Nu răciți metalul prin scufundare în lichid. În acest caz, structura internă a materialului este încălcată.
Aluminiul se poate îndoi ca hârtia sau poate fi la fel de dur ca oțelul. Aluminiul este peste tot, chiar și în noi.
Fiecare adult primește aproximativ 50 mg de aluminiu în fiecare zi prin alimente, nu este o dietă, este pur și simplu inevitabil.
Aluminiul este cel mai comun metal de pe planetă. Conținutul său în scoarța terestră este de 8%, dar nu este ușor de extras, cel puțin în forma sa pură.
Spre deosebire de aur și argint, aluminiul nu apare ca pepite sau vene întregi. Aluminiul este de 3 ori mai ușor decât fierul sau cuprul.
Aluminiul în forma sa originală nu seamănă deloc cu metalul, totul din cauza „iubirii” speciale a aluminiului pentru oxigen.
De fapt, prima utilizare a aluminiului în istorie a avut loc atunci când olarii orientali au adăugat argilă bogată în aluminiu produselor lor pentru a le face mai puternice. .
Suficient pentru a face cutii de bere, suficient de puternic pentru mașinile de curse, flexibil pentru pielea avioanelor, capabil să se transforme în orice, aluminiul este un material indispensabil pentru lumea modernă.
Și acestea nu sunt toate caracteristicile pe care le stochează acest metal util.
În timpul topirii și turnării în aer, aliajele de aluminiu sunt ușor oxidate și saturate cu hidrogen, iar efectul nociv al gazelor dizolvate asupra calității pieselor turnate este vizibil chiar și cu cantități mici din ele în topitură. S-a stabilit prin practică că cantitatea maximă admisă de hidrogen din aliajele de aluminiu, care face posibilă obținerea de piese turnate de înaltă calitate, este estimată la 0,1-0,20 cm 3 /100 g de metal. Prin urmare, atenția principală în timpul topirii este acordată prevenirii oxidării excesive și a saturației cu gaz a aliajului. Având în vedere efectele nocive ale impurităților din aliajele de aluminiu, aceștia se străduiesc și să obțină un aliaj cu cantități minime din aceste impurități, în special fier.
Metodele de topire a aliajelor de aluminiu depind de tipul de cuptoare și de materialele de încărcare utilizate. Tipul de cuptoare de topire se alege în funcție de natura producției și scopul aliajului.
Topirea aliajelor de aluminiu se realizeaza in cuptoare cu creuzet cu incalzire pe ulei, gaz si electric, in cuptoare cu reverberatie cu flacara, cuptoare cu rezistenta electrica cu vatra si cuptoare cu inductie. După scop, se disting cuptoarele de topire, de distribuție și de topire-distribuie.
Metalul de cea mai înaltă calitate se obține prin topirea în cuptoare cu inducție. În aceste cuptoare, topirea are loc rapid, metalul este bine amestecat și mai puțin saturat de gaz. Cuptoarele cu reverberație pe gaz sunt utilizate pentru topirea aliajelor de aluminiu în atelierele de turnare a țaglelor, precum și pentru retopirea deșeurilor și așchiilor. Cuptoarele cu rezistență electrică reflectorizante sunt comune în turnătoriile modelate.
Cuptoarele cu creuzet cu diferite metode de încălzire sunt utilizate pentru topirea cantităților relativ mici de metal (sunt deosebit de convenabile ca cuptoare de susținere).
Pentru topirea aliajelor de aluminiu se folosesc creuzete metalice sudate, turnate, mai rar forjate.
La topirea în creuzete metalice, există pericolul ca aliajul să interacționeze cu creuzetul și să îl contamineze cu impurități de fier. Cele mai agresive în ceea ce privește creuzetele din fontă sunt aliajele de aluminiu cu siliciu, apoi cu magneziu și mai puțin cu cupru și zinc. Prin urmare, pereții creuzetelor sunt acoperiți cu vopsele speciale de protecție înainte de topire, în plus, sunt selectate compoziții din fontă sau oțel care sunt mai rezistente la aluminiu. De exemplu, fontele cenușii sunt mai rezistente dacă conțin mai mult grafit și este într-o formă foarte ramificată. Siliciul din fontă (precum și siliciul din topitură) contribuie la interacțiunea metalului cu materialul creuzetului, prin urmare, se străduiesc să reducă conținutul său în fontă la limita inferioară și aluminiu (1,2–3,0% ) este folosit ca element de grafitizare în timpul topirii. În plus, aluminiul reduce oxidabilitatea creuzetului din exterior. Conținutul de mangan trebuie menținut la minimum. Crezetele din fontă cu un conținut de aluminiu de până la 8% și cu aditivi de crom (0,4-1,0%), precum și nichel și molibden, au rezistență ridicată.
- Când se topește pe materiale și ligaturi de încărcare proaspătă, aluminiul este mai întâi încărcat (în întregime sau parțial), iar apoi ligaturile sunt dizolvate.
- Dacă topirea se efectuează pe un aliaj de lingouri preliminare sau pe un lingot de silumin, aliajele de lingouri sunt mai întâi încărcate și topite, iar apoi aliajul este încărcat cu cantitatea necesară de aluminiu și aliaje principale.
- Metalele foarte predispuse la deșeuri, cum ar fi zincul, magneziul, sunt introduse în ultimul aliaj, de preferință sub un strat de flux.
- Dacă sarcina constă din deșeuri și lingouri de metal, succesiunea de încărcare este determinată de numărul de componente ale încărcăturii: în primul rând, cea mai mare parte a încărcăturii este încărcată în cuptor și topită. Dacă totuși deșeurile sunt puternic contaminate, este mai bine să le topești mai întâi, să le degazezi și apoi să încarci lingoul.
- Dacă capacitatea cuptorului și dimensiunile încărcăturii vă permit să încărcați diferitele sale componente în același timp, atunci împreună încarcă ceva care are un punct de topire apropiat, de exemplu, siliciu, deșeuri, lingouri de aluminiu. Amestecul este selectat cu cea mai mică cantitate de impurități pentru un aliaj dat. Așezarea încărcăturii în cuptor ar trebui să fie realizată în mod compact, topirea trebuie efectuată rapid. Când încărcați într-o baie de lichid, încărcătura solidă trebuie preîncălzită.
Materialele de încărcare și retururile trebuie depozitate în încăperi uscate și calde. Depozitarea lor în încăperi umede sau în aer liber duce la absorbția umidității și la creșterea oxidării.
Încărcarea este de obicei alcătuită din deșeuri și 20-60% din materiale proaspete, cântărite cu atenție în conformitate cu datele calculate. Calculul încărcăturii aliajelor de aluminiu turnat se efectuează conform datelor GOST (în funcție de compoziția medie sau optimă). În funcție de caracteristicile aliajelor și de cerințele pentru proprietățile turnării, compoziția unor componente se calculează cu cantitatea minimă, altele - cu maxim, iar al treilea componente se calculează prin cantitatea medie.
De exemplu, atunci când se calculează taxa pentru prepararea lingourilor din aliajele de aluminiu AK4, AK5, AK6 și D16, conținutul de cupru din aliaje este luat în funcție de limita superioară, ceea ce ajută la reducerea tendinței aliajelor de fisurare, iar conținutul de fier, magneziu și siliciu este luat, dimpotrivă, conform limitei inferioare, pentru a reduce segregarea.
Aliajul AL4 are următoarele limite compoziție chimică conform GOST: 8-10,5% Si, 0,25-0,5% Mn, 0,17-0,3% Mg, restul Al. De obicei, calculul se efectuează pe un conținut de siliciu de 8,25-9,25%. Conținutul de siliciu redus față de media (9,25%) este luat, deoarece ajută la creșterea rezistenței, la reducerea contracției concentrate și segregarea aliajului. Dar o scădere excesivă a siliciului determină o scădere a fluidității și a proprietăților mecanice, ceea ce este deosebit de important la turnarea pieselor cu pereți subțiri. Prin urmare, în astfel de cazuri, calculul se efectuează pe un conținut de siliciu de 9,25%. Manganul este introdus în aliajul AL4 în principal pentru a elimina efectele nocive ale fierului, dar un conținut crescut de mangan poate provoca o segregare severă. Prin urmare, dacă sarcina este relativ pură în ceea ce privește fierul, atunci calculul se bazează pe conținutul mediu de mangan (0,37%), iar dacă sarcina este puternic contaminată, atunci cantitatea de mangan este ajustată la 0,45%, adică mai aproape. până la limita superioară. Este deosebit de important atunci când pregătiți încărcătura de aliaj AL4 să luați în considerare efectul magneziului asupra proprietăți mecanice acest aliaj. Când conținutul de magneziu este la limita inferioară, aliajul va avea rezistență și duritate reduse, dar ductilitate ridicată.
Adesea, atunci când alegeți compoziția optimă a unui aliaj, este necesar să luați în considerare influența mai multor componente asupra proprietăților aliajului în același timp și apoi să alegeți cele mai convenabile combinații ale acestora. De exemplu, aliajul D19 (3,8-4,3% Cu; 1,8-2,3% Mg) are proprietăți de rezistență ridicată la căldură dacă cantitatea totală de cupru și magneziu din aliaj este de 6,1%, ceea ce este necesar să se țină seama la calcularea sarcinii. La topirea aliajului AL19 (4,5-5,3% Cu, 0,6-1,0% Mn, 0,25-0,35% Ti,<0,3% Fe, <0,3% Si, 0,05% Mg, остальное Al) высокие прочностные и пластические свойства получаются в том случае, когда содержание меди и марганца находятся на среднем уровне марочного состава сплава (5% Cu, 0,8% Mn,0 3% Ti, остальное Al). Любые отклонения от среднего содержания этих металлов неблагоприятно сказываются на механических свойствах.
Prin urmare, la topirea unor aliaje de aluminiu (în special a celor multicomponente), uneori este necesar să se pregătească mai întâi un aliaj pregătitor cu o anumită compoziție chimică din metale pure, să-l turneze în lingouri, să se analizeze compoziția și apoi, în funcție de compoziția specificată, utilizați-l ca încărcătură inițială pentru prepararea aliajului de lucru, mergând direct pentru matrițe de turnare.
Aliajele standard, a căror tehnologie de topire este destul de bine dezvoltată, sunt de obicei preparate o singură dată din materiale de încărcare, iar metalul este turnat imediat în matrițe.
Topirea încărcăturii este forțată, dar nu se recomandă supraîncălzirea topiturii. Dacă încărcătura este de dimensiuni mici, pentru a proteja împotriva oxidării excesive, topirea se efectuează folosind fluxuri de acoperire dintr-un amestec de săruri de clorură, care sunt încărcate împreună cu sarcina metalică într-o cantitate de 2-3% din greutate. metal. La atingerea supraîncălzirii necesare, metalul este controlat prin probe tehnologice pentru saturarea gazelor și contaminarea cu incluziuni de oxid și, dacă este necesar, se începe rafinarea și degazarea aliajului. Pe tot parcursul topiturii, începând cu prepararea materialelor de încărcare, este necesar să se prevină oxidarea excesivă și saturarea cu gaz a topiturii. Pentru a face acest lucru, este necesar să pregătiți cu atenție încărcătura pentru topire și să o curățați de impurități, precum și să păstrați cuptorul și toate uneltele curate. Cu cât se acordă mai multă atenție și timp pregătirii încărcăturii și cuptorului, cu atât mai puțini oxizi și gaze vor fi în topitură și cu atât este mai ușor să rafinați topitura înainte de turnare. Topirea neatentă, în cazul în care se utilizează o încărcătură umedă contaminată, nu usucă căptușeala cuptorului (calculată pentru curățarea ulterioară a topiturii ca urmare a rafinării și degazării la sfârșitul topiturii), nu dă rezultate bune, deoarece este adesea mai ușor să împiedici intrarea oxizilor în topitură și gaze înainte de a scăpa de ei.
Practica topirii aliajelor de aluminiu arată că există o relație directă între cantitatea de filme de oxid din topitură și saturația sa în gaz. Cu cât mai multe filme de oxid din aliaj, cu atât este mai mare saturația cu gaz. Prin urmare, amestecarea excesivă a topiturii trebuie evitată, mai ales dacă topirea se efectuează fără fluxuri de acoperire.