Что называется проваром сварочного шва. Типы сварных швов и их характеристика. Сварные угловые соединения
Сварные соединения. При ручной дуговой сварке выполняют соединения встык, втавр, внахлестку, угловые; в отдельных случаях - прорезные, торцовые с накладками, пробочные (рис. 36). Сварным называют неразъемное соединение, выполненное сваркой. В ГОСТ 2601 - 74 установлены термины на стыковое, угловое, нахле-сточное и тавровое соединения.
Сварные угловые соединения
Процессы и типы сварки. Существует несколько процессов сварки, которые отличаются тем, как тепло или энергия прикладываются к суставу. Мягкая пайка Сварочная сварка для сварки Газовая сварка Сварка с сопротивлением Индукционная сварка Дуговая сварка Сварка отливкой Фрикционная сварка Взрывная сварка Для обеспечения сварки некоторые процессы требуют только силы для соединения, другие требуют наполнителя и тепловая энергия, которая плавит указанный металл. Каждый из различных процессов сварки имеет свои особые технические характеристики и их удельные затраты.
Рис. 36. Классификация сварных соединений
а - стыковые; б - тавровые; в - угловые; г - нахлесточные; д- прорезные; е - торцовые; ж - с накладками; з - пробочные
Стыковые соединения. Такой вид соединения по сравнению с другими обеспечивает наименьшие собственные напряжения и деформации при сварке, расход основного и наплавленного металла, времени на сварку, что обусловило наибольшее его применение в сварочном производстве. Собираться встык могут листы одинаковой или разной толщины. Во втором случае на листе большей толщины делается скос с одной или двух сторон- до толщины меньшего листа. Разновидностью стыкового является соединение с отбортовкой и втавр. Соединения с отбортовкой применяют при тйлщине листов до 3 мм. Листы толщиной 3-8 мм сббирают без скоса кромок и с зазором 0,5-2 мм. Элементы толщиной до 6 мм сваривают с одной стороны, толщиной более 6 мм с двух сторон. У листов толщиной 3-8 мм кромки также можно скашивать. При толщине металла 3-26 мм выполняется односторонний скос кромок, называемый F-образной разделкой. Для металла толщиной 12-40 мм кромки скашивают с двух сторон (Х-об-разная разделка); при скосе одной кромки разделка называется К-образной. При Х-образной разделке количество наплавленного металла почти в 2 раза меньше, чем при У-образной, что приводит к уменьшению расхода электродов, электроэнергии, остаточных напряжений и деформаций и увеличению производительности. Для металла толщиной 20-60 мм рекомендуется U-об-разная разделка кромок, имеющая те же преимущества перед Х-образной, как последняя перед У-образной.
Сравнительная характеристика сварных швов
Его применение будет в основном зависеть от типа материала, который будет использоваться, появления союза и использования, которое будет дано союзу. Это объединение двух кусков металла с помощью другого металла, называемого вкладом, который применяется среди них в жидком состоянии. В этом процессе образуется сплав между металлами, и с этим достигается адгезия, которая генерирует соединение. Этот тип сварки используется для соединения деталей, которые не будут подвергаться большим нагрузкам или силам.
Тавровые соединения (рис. 36,6). Этот вид соединения получается при сопряжении торца одного элемента с поверхностью другого. Вертикальный элемент может быть без скоса кромок, со скосом одной или двух кромок.
Угловые соединения (рис. 36,в). В таком соединении торец одного собираемого элемента прихватывается к концу плоскости другого элемента, образуя прямой, тупой или острый угол. Угловое соединение является частным случаем таврового.
Одним из его основных применений является объединение элементов в электрические схемы. Обычно наполнитель металла расплавляется с помощью паяльника и течет по капиллярности. Обычно для удаления оксидов с поверхностей, подлежащих соединению, требуются специальные флюсы и повышение текучести до наполнителя.
Что называется сваркой?
Некоторые из наполнителей представляют собой сплавы меди, алюминия или серебра. Твердый припой можно классифицировать по способу нанесения наполнителя. Предварительно расплавленный наполнитель металла вводится между двумя частями, подлежащими соединению, когда он затвердевает, части соединяются.
Нахлесточные соединения. При наложении плоскости одного собираемого элемента на плоскость другого (рис. 36,г) образуются нахлесточные соединения. Они рекомендуются для металла толщиной не более 10 - 12 мм. Сварку следует вести с двух сторон, чтобы в зазор между касающимися элементами не попала влага.
Прорезные соединения (рис. 36,<3). Разновидностью нахлесточных соединений являются прорезные, выполняемые, когда длина нормального шва нахлесточного не обеспечивает необходимой прочности.
Сварные нахлёсточные соединения
Металл наполнителя в твердом состоянии помещается между соединяемыми частями, они нагреваются в газовой или электрической печи, так что при температуре расплавленный металл наполнителя и соединение образуются при его охлаждении. Тепло наносится на факел локально на части соединяемого металла, наполнитель металла в виде проволоки расплавляется в суставе. Факелы могут работать со следующими окислителями: сжатым воздухом, атмосферным воздухом, кислородом или воздухом, хранящимся под давлением в баке.
Торцовые соединения (рис. 36,е). Сварной шов у торцовых соединений накладывается на расположенные на одном уровне торцы собираемых листов.
Соединения с накладками (рис. 36,ж). Такой вид соединений осуществляется, когда их нельзя заменить стыковыми или нахлесточными, по сравнению с которыми требуек:я дополнительный расход металла на накладки.
Топливом могут быть: спирт, белый бензин, метан, пропан-бутан, водород или ацетилен. Температура соединяемых деталей и наполнительного металла может быть достигнута с помощью сопротивления току, индукции или дуги во всех трех способах, когда нагрев задается прохождением тока между соединяемыми металлическими частями.
Это самый старый процесс сварки. Процесс состоит в нагревании штук, которые должны быть соединены в кузницу с его пластическим состоянием, а затем посредством давления или нарезания соединения штук. В этой процедуре не используется металлический наполнитель, и ограничение процесса заключается в том, что его можно наносить только небольшими кусками и в виде листа. Соединение делается из центра деталей наружу, и необходимо избегать окисления, для этого используются тяжелые масла с флюсом, обычно используется бура в сочетании с солью аммония.
Соединения пробочные (рис. 36,з). В указанном соединении свариваемые элементы располагаются внахлестку, верхний лист просверливается по линии сварного шва в отдельных точках. Отверстия завариваются. При этом с нижним листом образуется прочная связь. Пробочные соединения имеют хорошую прочность при небольшой плотности шва.
Сварные швы. Участок сварного соединения, образовавшийся в результате кристаллизации металла сварочной ванны, называется сварным швом.
Типы сварных швов и их характеристика
Этот процесс включает в себя все сварные швы, которые используют горючий газ для генерирования энергии, необходимой для расплавления входного материала. Наиболее часто используемыми видами топлива являются метан, ацетилен и водород, которые в сочетании с кислородом в качестве окислителя генерируют аутогенные и оксидные сварные швы.
Кислородная сварка является продуктом комбинации кислорода и водорода в факеле. Автогенная сварка достигается путем объединения ацетилена и кислорода в факеле. Он известен как аутогенный, поскольку с комбинацией топлива и комбатанта существует автономия, которую нужно обрабатывать в разных средах. Ацетилен получают путем отбрасывания карбидов карбида кальция в воде, где осадок представляет собой гашеную известь и ацетиленовые газы.
По размещению в пространстве швы делятся на нижние, горизонтальные, вертикальные и потолочные (рис. 37). Нижним называется шов, расположенный на горизонтальной плоскости или на плоскости, наклонной к горизонту под углом до 60° (1,02 рад). Вертикальными и горизонтальными называются швы, расположенные на вертикальной плоскости или на плоскости, отклоненной от вертикали на угол 30° (0,51 рад). Потолочными называют швы, расположенные на «потолке».
Цилиндры и регуляторы для кислородной сварки. В факелах автогенной сварки могут быть получены три типа пламени, которые уменьшают, нейтрализуют и окислитель. Из трех нейтральных является тот, который имеет наибольшее применение. Это пламя сбалансировано в количестве ацетилена и кислорода, который он использует.
В восстановительном или науглероживающем пламени имеется избыток ацетилена, который генерирует то, что между световым конусом и оболочкой имеется белый конус, длина которого определяется избытком ацетилена. Это пламя используется для сварки монелей, никеля, некоторых стальных сплавов и многих цветных материалов.
Рис. 37. Классификация сварных швов по расположению их в пространстве
а - нижние; б - горизонтальные; в - вертикальные; г - потолочные
Рис. 38. Прерывистые швы
По протяженности различают непрерывные и прерывистые швы (рис. 38). Длина отдельного отрезка прерывистого шва лежит в пределах 50-150 мм, а расстояние между ними равняется 1,5-2,5 длины отрезка.
Окислительное пламя имеет тот же вид, что и нейтральное пламя, за исключением того, что конус света короче и окружающий конус имеет больше цвета. Это пламя используется для сварки плавлением латуни и бронзы. Одним из выводов этого типа пламени является использование в режущих факелах, в которых внезапное окисление создает разрез металлов. В режущих факелах рядом с центральным отверстием имеется серия небольших вспышек, через которые поступает значительный поток чистого кислорода, который режет металл.
В некоторых случаях при автогенной сварке воздух используется в качестве окислителя, что означает, что температура этого пламени на 20% ниже, чем температура кислорода, поэтому его использование ограничивается объединением только нескольких металлов, таких как свинец. При этом типе сварки факел известен как «горелка Бунзена».
Количество наплавленного металла также является одним из факторов, определяющих вид сварного шва.
Рис. 39. Швы нормальные
По типу сварного соединения швы делятся на стыковые и угловые. Кратчайшее расстояние от поверхности одной из свариваемых частей до границы углового шва на поверхности второй свариваемой части называется катетом.
Сварные тавровые соединения
Процессы газовой сварки могут включать в себя те, в которых соединяемые детали нагреваются, а затем без металлического наполнителя они прижимаются с достаточной силой для создания соединения. Принцип действия этого процесса состоит в том, чтобы пропускать электрический ток большой интенсивности через соединяемые металлы, так как при объединении того же сопротивления больше, чем в их телах, будет возрастать повышение температуры, используя эту энергию и при небольшом давлении достигается соединение.
Характерные виды брака в сварных швах и соединениях
Сварка сопротивлением применима практически ко всем металлам, за исключением олова, цинка и свинца. В процессах контактной сварки включаются. Точечная сварка точечной сварки точечной сварки точечной сварки точечной сварки электрический ток проходит через два заостренных электрода из-за сопротивления соединяемого материала, достигается нагрев и давление на детали, генерируемые точка сварки. Точечные сварочные аппараты могут быть закреплены или подвижны или соединены с роботом или механическим рычагом.
Элементы разделки сварного шва. К геометрическим элементам разделки шва относятся угол разделки, зазор между свариваемыми деталями, притупление, скос кромки и смещение свариваемых деталей относительно друг друга (рис. 40). Угол разделки кромок при ручной сварке обычно принимается равным 60±5° (1,02+0,8 рад), притупление-1-3 мм, зазор - 0- 4 мм. Отсутствие разделки кромок при толщине металла свыше 8 мм обычно приводит к непровару. К непровару приводит также отсутствие зазора. Кромки без притупления могут явиться причиной образования прожогов. Смещение кромок затрудняет, а в некоторых случаях делает невозможным получение сварного соединения хорошего качества. Величина смещения зависит от толщины стыкуемых деталей и ответственности изделия. Для таких изделий смещение регламентируется техническими условиями на их изготовление. Смещение кромок на деталях и арматуре трубопроводов, не подведомственных Госгортехнадзору в соответствии со СНиП Ш-Г.9-62 «Технологические трубопроводы. Правила производства и приемки работ» допускается в пределах, указанных ниже.
Схема точечной сварочной машины. Точечная сварка - это процесс, аналогичный процессу точек, только в этом случае несколько точек создаются одновременно с каждым процессом. Точки определяются положением набора кончиков, которые вступают в контакт одновременно.
Сварка швов состоит в непрерывном соединении двух перекрывающихся листов. Соединение создается нагревом, полученным из-за сопротивления прохождению тока и постоянному давлению, оказываемому двумя круглыми электродами. Этот процесс сварки является непрерывным.
Стыковая сварка состоит в объединении двух частей с одной и той же секцией, они прижимаются, когда через них проходит электрический ток, который генерирует тепло на контактной поверхности. При созданной температуре и давлении между двумя частями соединение достигается.
Типы сварных швов и их характеристика
По конструктивным признакам (по взаимному расположению соединяемых элементов) сварные соединения разделяют на:
- стыковые - свариваемые элементы примыкают торцовыми поверхностями и являются продолжением один другого, область применения таких соединений расширяется;
- нахлесточные - боковые поверхности соединяемых элементов частично перекрывают друг друга;
- тавровые - торец одного элемента примыкает под углом (обычно 90°) и приварен к боковой поверхности другого элемента;
- угловые - соединяемые элементы приваривают по кромкам один к другому. В силовых конструкциях угловые швы почти не применяют и на прочность не рассчитывают.
- торцовые - соединяемые элементы соединяют боковыми поверхностями и сваривают с торца. Этот вид соединений на прочность, как правило, не рассчитывают.
На рисунке 1 приведены примеры перечисленных выше типов сварных швов.
Эта сварка производится за счет использования тепла, создаваемого сопротивлением потоку электрического тока, индуцированного в соединяемых частях. Обычно эта сварка достигается также давлением. Он состоит в соединении катушки с соединяемыми металлами и потому что в объединении металлов существует большая устойчивость к прохождению тока, индуцированного в той части, в которой генерируется тепло, которое генерирует давление объединение двух частей.
Это процесс, в котором его энергия получается с помощью тепла, создаваемого электрической дугой, которая образуется между куском и электродом. Обычно электрод также служит в качестве наполнителя, который расплавляется электрической дугой, так что он может быть нанесен между штучками, подлежащими соединению. Ток, который используется в процессе, может быть прямым или альтернативным, который используется в большинстве прямых, потому что энергия более постоянна с тем, что может генерировать устойчивую дугу.
В зависимости от типа сварного шва различают сварные соединения:
- со стыковыми швами (в стыковых и тавровых соединениях) ;
- с угловыми швами (в нахлесточных, тавровых, угловых и торцовых соединениях) .
Исходное условие проектирования сварного соединения - обеспечение равнопрочности сварного шва и соединяемых элементов.
Условие равнопрочности, например, для сварного нахлесточного соединения сводится к тому, что расчет параметров сварного шва следует выполнять по силе [F]
, определяемой по прочности элемента с наименьшим поперечным сечением:
Для генерации арки существуют следующие электроды. Углеродный электрод: в настоящее время мало используется, электрод используется только в качестве проводника для получения тепла, металл наполнителя добавляется отдельно. Металлический электрод: сам электрод служит в качестве наполнителя при расплавлении на соединяемых материалах. Они могут использоваться для этих сварочных аппаратов для электродов прямого или переменного тока, а второй состоит из статических трансформаторов, которые генерируют низкое техническое обслуживание и первоначальные инвестиции.
[F] = δ×b×[σ] р ,
где: δ - толщина свариваемой детали; b - ширина свариваемой детали; [σ] р – допускаемое напряжение растяжения.
Сварные швы разделяют на рабочие
и связующие
. На прочность рассчитывают только рабочие швы, которые непосредственно передают рабочую нагрузку между соединяемыми элементами.
Связующие швы испытывают напряжения только от совместной деформации с основным металлом. Они мало нагружены и на прочность их не рассчитывают.
Композиции электродных покрытий могут быть органическими или неорганическими, и эти вещества можно подразделить на те, которые образуют шлак, и те, которые являются потоками. Некоторые из основных соединений. Растворители: графит, алюминий, опилки. Для улучшения связи: силикат натрия, силикат калия и асбест.
Для улучшения сплава и сопротивления сварки: ванадия, цезия, кобальта, молибдена, алюминия, циркония, хрома, никеля, марганца и вольфрама. Типы электродов. Электроды для такого типа сварки подчиняются стандартам качества, результатам и типам использования. Номенклатура такова.
Сварные стыковые соединения
Стыковым соединением называется сварное соединение двух элементов, примыкающих друг к другу торцевыми поверхностями и размещенных на одной поверхности или в одной плоскости.
Стандартом ГОСТ 5264-80 предусмотрено 32 типа стыковых соединений, условно обозначенных С1, С2, ... С28 и т.д., имеющих различную подготовку кромок в зависимости от толщины, расположения свариваемых элементов, технологии сварки и наличия оборудования для обработки кромок.
Е указывает, что он является электродом с покрытием. Иногда у электродов есть буквы в конце, это зависит от компании, которая их создала. Следующую таблицу. Письма В зависимости от марки электродов устанавливаются сплавы и характеристики проникновения.
Сила тока, которая должна применяться для генерации сварки, очень важна, она зависит от того, что электрод не прилипает, что сварочная обтекаемость между двумя частями или что соединяемые детали не перфорированы. Практическая рекомендация, которая используется в семинарах для определения текущего, без необходимости прибегать к таблице, такова.
Стыковые соединения являются наиболее простыми и надежными из всех сварных соединений. Их рекомендуют в конструкциях, подверженных воздействию переменных напряжений.
Встык можно сваривать листы, полосы, трубы, швеллеры, уголки и другие фасонные профили.
Если стыковое соединение образуют два металлических листа, то их сближают до соприкосновения по торцам и сваривают.
Выступ стыкового шва над основным металлом является концентратором напряжений. Поэтому в ответственных соединениях его удаляют механическим способом.
При автоматической сварке в зависимости от толщины δ
деталей сварку выполняют односторонним (рис. 1, б, в, г)
или двусторонним (рис. 1,а)
швами.
При толщинах δ
до 15мм
сварку выполняют без специальной подготовки кромок. При большей толщине листов предварительно выполняют специальную подготовку кромок.
При ручной сварке без подготовки кромок сваривают листы толщиной до 8мм . Шов накладывают с одной стороны (при δ ≤ 3 мм) или с двух сторон (3 < δ ≤ 8 мм) .
В районе сварного шва из-за высокой местной температуры может произойти изменение физических, химических, структурных свойств основного металла и, как следствие, понижение его механических характеристик - появляется так называемая зона термического влияния . Поэтому разрушение сварного соединения происходит обычно в зоне влияния, т.е. вблизи сварного шва.
Расчет стыкового соединения выполняют по размерам сечения детали в зоне термического влияния.
Условие прочности при нагружении растягивающей силой F
соединения в виде полосы:
σ р = F/(δ×b) ≤ [σ]’ р
Допускаемые напряжения для расчета сварных соединений принимают по механическим характеристикам материала в зоне влияния сварного шва и отмечают штрихом [σ]" р в отличие от допускаемых напряжений основного металла [σ] р .
В стыковом соединении, нагруженном изгибающим моментом М , вычисляют напряжения σ и изгиба:
σ и = М/W ≤ [σ]’ p
Как уже указывалось выше, стыковое соединение может быть выполнено не только из листов или полос, но и из труб, уголков, швеллеров и других фасонных профилей. Во всех случаях сварная конструкция получается близкой к целой.
Сварные нахлёсточные соединения
Нахлесточным соединением называют сварное соединение, в котором сваренные угловыми швами элементы расположены параллельно и частично перекрывают друг друга.
Стандартом предусмотрено два таких соединения: Н1
и Н2
, которые отличаются только тем, что в соединении H1
к поверхности элементов привариваются два торца, а в соединении H2
- только один торец.
Иногда применяют разновидности нахлесточного соединения: с накладкой и с точечными швами, соединяющими части элементов конструкции.
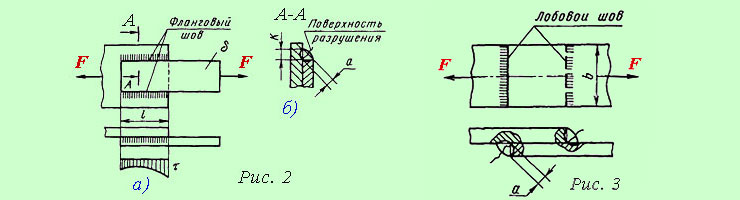
Сварное нахлесточное соединение выполняют фланговыми (рис. 2,а)
или лобовыми (рис. 3)
швами. При этом шов заполняет угол между боковой поверхностью одного элемента и кромкой другого. Такие швы называют угловыми
.
Угловые швы выполняют однопроходными и многопроходными, без скоса кромок и со скосом кромок.
Основными характеристиками углового шва являются (рис. 2,б)
: k
- катет (по аналогии со стороной прямоугольного треугольника), а
- рабочая высота (определяет наименьшее сечение в плоскости, проходящей через биссектрису прямого угла, по которому происходит разрушение - срез)
.
Обычно для шва при ручной сварке а = 0,7k
(высота прямоугольного треугольника с катетами
k
)
.
Автоматическую сварку характеризует более глубокий провар: а = k
. Условия работы такого шва более благоприятные.
Не рекомендуется применять катет менее 3мм
.
Вследствие различной жесткости соединяемых элементов касательные напряжения τ (напряжения среза) по длине флангового шва распределены неравномерно (рис. 2,а) . Чем длиннее шов, тем больше неравномерность. Поэтому длину шва ограничивают:
30 мм < l ≤ 60k,
где: k – катет сварного шва, мм, l - длина шва.
В швах длиной менее 30 мм не успевает установиться тепловой режим и получается некачественный шов. А при длинных швах существует высокая неравномерность в распределении напряжений.
Угловой шов при нагружении испытывает сложное напряженное состояние. Однако для простоты такой шов условно рассчитывают на срез под действием средних касательных напряжений τ .
Условие прочности флангового шва (рис. 2) :
τ = F/(a×2l) ≤ [τ]’ (здесь 2 – число швов)
Во избежание возникновения повышенных изгибающих напряжений лобовые швы следует накладывать с двух сторон (рис. 3)
.
Как показывает практика, разрушение лобовых швов происходит вследствие их среза по биссектральной плоскости. Поэтому расчет лобовых швов условно ведут по напряжениям среза τ
.
Поверхность разрушения определяют размеры а
и b
:
τ = F / (a×2b) ≤ [τ]’
Применяют также комбинированные швы, состоящие из фланговых и лобовых.
Для простоты считают, что сила F
растяжения нагружает швы равномерно:
τ = F / (a×L) ≤ [τ]’
где: L – периметр комбинированного шва : L = 2l +b
Сварные угловые соединения
Угловым соединением называется сварное соединение двух элементов, размещенных под углом и сваренных в месте примыкания их краев (см. рис. 1, д, е, ж)
.
Стандартом предусмотрено десять типов угловых соединений: от У1
до У10
.
Иногда при сварке применяют угловое соединение со стальной подкладкой, которая обеспечивает надежный провар элементов по всему сечению. При толщине металла 8...100 мм применяют двустороннюю разделку примыкающего элемента под углом примерно 45° .
Расчеты угловых сварных соединений на прочность проводятся редко, поскольку в силовых конструкциях их почти не применяют. Способы расчета такого соединения на прочность аналогичны способам расчетов для таврового соединения и зависит от типа шва.
Подробнее методика таких расчетов изложена ниже.
Сварные тавровые соединения
Тавровым соединением называется такое сварное соединение, в котором торец одного элемента примыкает под углом и присоединен к боковой поверхности другого элемента. Чаще всего тавровое соединение образуют элементы, расположенные во взаимно перпендикулярных плоскостях (рис. 1, з, и, к)
.
Такое соединение может быть выполнено швами с глубоким проплавлением, получаемыми при автоматической сварке и при сварке с предварительной подготовкой кромок (стыковым швом), или угловыми швами при ручной сварке.
Стандартом предусмотрено несколько типов таких соединений: с Т1
по T9
.
Метод расчета углового и таврового соединения зависит от типа шва.
Швы с глубоким проплавлением прочнее основного металла. При нагружении соединения силой F разрушение происходит по сечению детали в зоне термического влияния. Расчет проводят по нормальным напряжениям растяжения σ р :
σ р = F / (δ×b) ≤ [σ]’ р
Учет сварки проявляется в том, что принимают допускаемые напряжения для сварного шва, хотя расчет проводят по основному металлу.
Угловой шов менее прочен, чем основной металл. Поверхность разрушения расположена в биссектральной плоскости шва, как в лобовых и фланговых швах нахлесточных соединений.
Напряжения среза:
τ р = F / (a×2b) ≤ [τ]’
Если соединение нагружено сжимающей силой, то часть силы передает основной металл и допускаемые напряжения можно повысить примерно на 60 % .
Характерные виды брака в сварных швах и соединениях
На рисунке 4 представлены наиболее часто встречающиеся виды брака при сварке изделий, которые могут значительно снизить прочность шва и конструкции в целом.
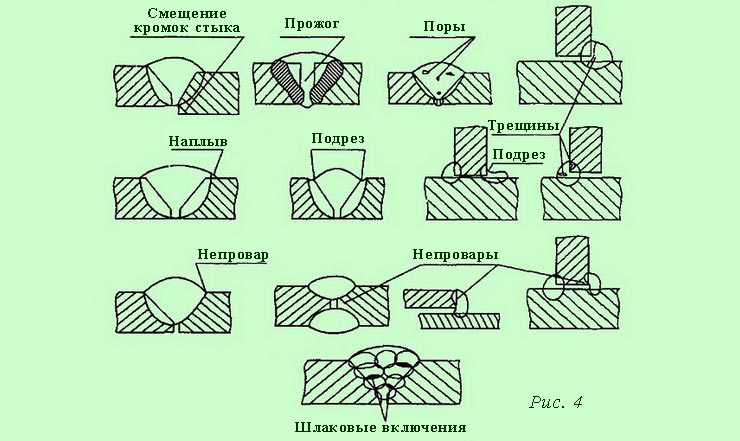
Сравнительная характеристика сварных швов
Из перечисленных сварных соединений наиболее надежными и экономичными являются стыковые соединения
, в которых действующие нагрузки и усилия воспринимаются так же, как в целых элементах, не подвергавшихся сварке, т. е. они практически равноценны основному металлу, конечно, при соответствующем качестве сварочных работ. Однако надо иметь в виду, что обработка кромок стыковых соединений и их подгонка под сварку достаточно сложны, кроме того, применение их бывает ограничено особенностями формы конструкций.
Угловые и тавровые соединения
также распространены в конструкциях. Их положительные свойства сказываются при изготовлении объемных конструкций.
Нахлесточные соединения
наиболее просты в работе, так как не нуждаются в предварительной разделке кромок, и подготовка их к сварке проще, чем стыковых и угловых соединений. Вследствие этого, а также из-за конструктивной формы некоторых сооружений они получили распространение для соединения элементов небольшой толщины, но допускаются для элементов толщиной до 60 мм
.
Недостатком нахлесточных соединений является их неэкономичность, вызванная перерасходом основного и наплавленного металла. Кроме того, из-за смещения линии действия усилий при переходе с одной детали на другую и возникновения концентрации напряжений снижается несущая способность таких соединений.
Кроме перечисленных сварных соединений и швов при ручной дуговой сварке применяют соединения под острыми и тупыми углами по ГОСТ 11534-75
, но они встречаются значительно реже.
Для сварки в защитном газе, сварки алюминия, меди, других цветных металлов и их сплавов применяют сварные соединения и швы, предусмотренные отдельными стандартами. Например, форма подготовки кромок и швов конструкций трубопроводов предусмотрена ГОСТ 16037-80
, в котором определены основные размеры швов для различных видов сварки.