Презентация урока для интерактивной доски на тему: Структура сварного шва. Строение сварных соединений
В зависимости от реальных условий процесса сварки, температуры, скорости нагрева и охлаждения различных участков металл сварного соединения неоднороден и состоит из следующих зон (рис. 1.1).
Металл шва – это та зона, в которой в связи с нагревом выше температуры плавления (линии ликвидус) свариваемый металл расплавляется в процессе сварки, перемешивается с металлом электрода и затем кристаллизуется. Металл шва имеет литую дендритную структуру и состоит из кристаллов столбчатой формы. Особенностью кристаллизации сварочной ванны является то, что в отличие от кристаллизации отливки в литейной форме, кристаллизация металла шва протекает при одновременном его подогреве со стороны источника тепла и быстром охлаждении за счет интенсивного теплоотвода в основной холодный металл.
Рис. 1.1. Макроструктура нахлесточного сварного соединения
Зона сплавления– расположенана границе основного металла и металла шва. В данной зоне выделяется участок с крупными зернами, т. е. участок металла, который в процессе сварки нагревался до температуры выше линии солидус, но ниже линии ликвидус (в данной температурной области происходит частичное расплавление основного металла). В нее попадают химические элементы из металла электрода (из сварочной ванны). В месте примыкания к границе сплавления основного металла со швом, из-за большой разницы химического состава основного и электродного (присадочного) металлов может образоваться химическая неоднородность. Эта неоднородность может привести к скачкообразному изменению физико-механических свойств металла околошовной зоны и снижению надежности сварного соединения. Ширина зоны сплавления изменяется в пределах 0,1 – 0,4 мм и зависит от химического состава свариваемого металла (от температурного интервала «ликвидус – солидус»), от способа и режима сварки.
Зона термического влияния – часть основного металла, примыкающая к сварному шву, с измененными в процессе сварки структурой и свойствами. Общая ширина ЗТВ зависит от условий нагрева и охлаждения, от теплофизических свойств и толщины свариваемого металла, от метеоусловий и пр. (при дуговой сварке она составляет – 2 – 6, а при газовой – до 30 мм).
Изменение структуры в околошовной зоне, например на однопроходном стыковом соединении, можно проследить, поместив над сечением сварного соединения кривую распределения максимальной температуры, совместив ее в том же масштабе температуры с диаграммой состояния железо-цементит.
Намечая на диаграмме состояния сплавов характерные зоны и участки, перенесем их границы на график распределения температуры (рис. 1.2). Из точек пересечения горизонтальных линий с кривой охлаждения опустим перпендикуляры на рисунок сечения сварного соединения. Это позволит определить линейные границы отдельных участков зоны термического влияния. Наибольшее применение в сварочном производстве получили низко- и среднеуглеродистые стали. В процессе сварки плавлением низкоуглеродистых сталей применяют сварочные материалы, при которых металл шва получается либо низкоуглеродистым, либо низколегированным. Такие стали малочувствительны к скорости охлаждения и не образуют закалочных структур. Их структура, как правило, ферритно-перлитная.
Рассмотрим зону термического влияния сварного соединения (см. рис. 1.2 – 1.4):
1 – переходный участок или участок сплавления , обычно размер его невелик. Интервал температуры, для стали 20, около 1490 – 1520°С. Структура стали – крупнозернистая, возможно образование видманштеттовой структуры (рис. 1.4);
2 – участок перегрева (см. рис. 1.3, б и 1.4). Металл нагревается выше 1100°С, до температуры, близкой к линии солидус. В этом интервале температуры за счет роста зерна аустенита формируется крупнозернистая структура перегретой стали с пониженной ударной вязкостью. Часто на этом участке образуется видманштеттова структура (крупнозернистая с зернами феррита иглообразной формы), что еще больше повышает хрупкость стали. Ширина этого участка – 1 – 3 мм;
3 – участок нормализации (рис. 1.4). Металл нагревается выше третьей критической точки Ас 3 (от 900 до 1100°С). В процессе полной перекристаллизации в аустенит, на этом участке образуется мелкозернистая (сорбитообразная) структура, которая обеспечивает более высокие механические свойства стали, по сравнению со свойствами исходного металла и свойствами других участков зоны термического влияния. Ширина этого участка – 1,2 – 4 мм;
Рис. 1.2. Схема строения сварного шва
4 – участок неполной перекристаллизации (рис. 1.4). Металл нагревается до температуры 725 – 850°С (между первой Ас 1 и третьей критическими точками Ас 3). Процесс измельчения зерна происходит только за счет перекристаллизации той части структуры, которая занята перлитом, а размер зерен феррита не изменяется. Поэтому сталь на этом участке может состоять не только из мелких зерен, но и отдельных крупных зерен феррита. Сталь с разнозернистым строением имеет более низкие механические свойства, чем мелкозернистая сталь. Ширина этого участка – 0,7 – 4 мм;
5 – участок рекристаллизации. Температура нагрева этого участка ниже первой критической точки Ас 1 (727°С). При сварке горячекатаной или отожженной стали, на этом участке ЗТВ никакие структурные изменения в металле не происходят.
Если же сталь перед сваркой была наклепана (нагартована) в результате холодной пластической деформации (штамповка, гибка, правка), то при нагреве в интервале температуры 550 – 600°С произойдет процесс рекристаллизации (рост новых равноосных зерен за счет исходных деформированных). По сравнению с исходным металлом прочность и твердость стали снизятся, а пластичность увеличится. В случае если температура нагрева металла на этом участке близка к первой критической точке (727°С) и длительность пребывания его при этой температуре значительна, то происходит процесс собирательной рекристаллизации. При этом укрупняется зерно и происходит разупрочнение металла. Данный участок в этом случае называют участком разупрочнения.
Рис. 1.3. Структура стали Ст3сп при автоматической дуговой сварке: а – металл шва, феррит и перлит (проволока Св-08ГА, флюс АН-348А); б – участок перегрева зоны термического влияния (видманштеттовая структура); в – основной металл. ×100
6 – участок синеломкости. Температура нагрева металла на данном участке сварного шва в интервале 200 – 400°С, при котором на поверхности стали появляются синие цвета побежалости (пленки окислов). Характеризуется тем, что прочность и твердость металла повышаются, а пластичность и ударная вязкость – резко падают. Это явление получило название «синеломкость». Вероятной причиной этого является старением металла – выделение по границам зерен из пересыщенного твердого раствора дисперсных карбидов и нитридов.
1.1.3. Влияние структуры шва на механические свойства сварного соединения
Таким образом, структура и, соответственно, механические свойства металла отдельных зон и участков сварного соединения неодинаковы (рис. 1.4).
Рис. 1.4. Микроструктура зоны термического влияния при дуговой сварке низкоуглеродистой стали Ст3сп (смотреть слева направо – от основного металла к металлу шва) ×100
В зоне термического влияния наиболее низкие механические свойства наблюдаются у металла шва, на границе сплавления, участке перегрева и участке синеломкости. У наплавленного металла шва это объясняется литой структурой металла и вероятностью наличия дефектов (инородных включений, пор, непроваров, трещин и т. п.) (рис. 1.5), в переходной зоне шва – тем, что структура стали состоит из литых зерен и крупных кристаллов перегретого металла с характерной для них низкой прочностью. На участке синеломкости также низкие пластичность и ударная вязкость. Такая разносвойственность участков сварного шва особенно резко проявляется при эксплуатации сварных конструкций, испытывающих динамические и циклические нагрузки.
Структурную неоднородность сварного соединения можно в определенной степени устранить термической обработкой. Если на термическую обработку возлагается только задача снятия внутренних напряжений, возникших в результате сварки, то можно ограничиться низкотемпературным отжигом при 500 – 600°С с последующим медленным охлаждением. Перегрев и видманштеттовая структура ЗТВ устраняются измельчением зерна стали за счет повторной перекристаллизации (полным отжигом или нормализацией).
а б в
Рис. 1.5. Макродефекты сварных соединений: а – поры и шлаковые включения; б – межкристаллитная трещина; в – трещина в околошовной зоне
Наиболее эффективным средством изменения параметров термического цикла является предварительный или сопутствующий подогрев места сварки (последующее снижение скорости охлаждения для уменьшения закалочных явлений). Однако подогрев иногда не может быть использован из-за возможности чрезмерного роста зерна стали (перегрева), образования околошовных горячих трещин или из-за трудности осуществления.
Прочность сварного соединения зависит также от дефектов, не связанных со структурными превращениями, – это неправильное формирование шва, образование наплывов и подрезов, образование трещин при неравномерной усадке в процессе кристаллизации металла шва. При затвердевании объем шва уменьшается, а основной металл препятствует этой усадке. В результате могут образоваться значительные внутренние напряжения и даже трещины.
Что будем делать с полученным материалом:
Если этот материал оказался полезным ля Вас, Вы можете сохранить его на свою страничку в социальных сетях:
Сварные соединения, выполненные сваркой плавлением, можно разделить на несколько зон, отличающихся макро- и микроструктурой, химическим составом, механическими свойствами и другими признаками: сварной шов, зону сплавления, зону термического влияния и основной металл (рис. 1). Характерные признаки зон связаны с фазовыми и структурными превращениями, которые претерпевают при сварке металл в каждой зоне.
Рис. 1. Характерные зоны сварных соединений1 - шов, 2 - зона термического влияния, 3 - основной металл, 4 - околошовный участок зоны термического влияния, 5 - зона сплавления, T л, T c и T п - темпе
Сварной шов характеризуется литой макроструктурой металла. Ему присуща первичная микроструктура кристаллизации, тип которой зависит от состава шва и условий фазового перехода из жидкого состояния в твердое.
Зона термического влияния (ЗТВ) - участок основного металла, примыкающий к сварному шву, в пределах которого вследствие теплового воздействия сварочного источника нагрева протекают фазовые и структурные превращения в твердом металле. В результате этого ЗТВ имеет отличные от основного металла величину зерна и вторичную микроструктуру. Часто выделяют околошовный участок ЗТВ или околошовную зону (ОШЗ). Она располагается непосредственно у сварного шва и включает несколько рядов крупных зерен. Металл шва, имеющий литую макроструктуру, и ЗТВ в основном металле, имеющая макроструктуру проката или рекристаллизованную макроструктуру литой или кованой заготовки, разделяются друг от друга поверхностью сплавления. На поверхности шлифов, вырезанных из сварного соединения и подвергнутых травлению реактивами, она при небольших увеличениях наблюдается как линия или граница сплавления.
Зона сплавления (ЗС) - это зона сварного соединения, где происходит сплавление наплавленного и основного металла. В нее входит узкий участок шва, расположенный у линии сплавления, а также оплавленный участок ОШЗ. Первый участок образуется вследствие недостаточно эффективного переноса, расплавленного основного металла в центральные части сварочной ванны. Здесь имеет место перемешивание наплавленного и основного металлов в соизмеримых долях. На оплавленном участке ОШЗ возможно появление между оплавленными зернами жидких прослоек, имеющих аналогичный состав. В случае применения разнородных наплавленного и основного металлов (например, аустенитного и перлитного) ЗС отчетливо наблюдается в виде переходной прослойки. Она имеет часто существенно отличающиеся от металла шва и ЗТВ химический состав, вторичную микроструктуру и свойства. Распределение элементов по ширине ЗС имеет сложный характер, который определяется процессами перемешивания направленного и основного металла, диффузионного перераспределения элементов между твердой и жидкой фазами и в твердой фазе на этапе охлаждения.
Основной металл располагается, за пределами ЗТВ и не претерпевает изменений при сварке. Может влиять на превращения в ЗТВ в зависимости от его макро- и микроструктуры, определяемых способом первичной обработки металла (прокат, литье, ковка, деформирование в холодном состоянии) и последующей термообработкой (отжиг, нормализация, закалка с отпуском, закалка со старением и т. п.).
В процессе дуговой сварки происходит расплавление основного и присадочного материала, образуется жидкая сварочная ванна, при затвердевании которой формируется сварное соединение. Рассмотрим более детально особенности процесса плавления и кристаллизации при сварке. В отличие от большой металлургии, размеры сварочной ванны небольшие, время нахождения металла в жидком состоянии мало, одновременно происходят процессы нагрева и кристаллизации металла, в результате неравномерности нагрева и охлаждения возникают значительные внутренние напряжения. Сварочную ванну условно можно разделить на две части (см. рисунок ниже): головная (АВ и САД), в которой происходит нагрев и плавление основного металла и хвостовая (ВК и СКД), в которой идут процессы охлаждения, кристаллизации и формирования сварного шва. Фронтом кристаллизации служат стенки сварочной ванны, форма которой происходит по нормали к поверхности фронта.
Скорость роста кристаллов на разных участках ванны - разная. В точках В, С и Д Vкр = 0, а в точке К Vкр = Vсв. Во всех других точках хвостовой части ванны она будет меняться от 0 до Vcв. При этом растущие столбчатые или дендритные кристаллы будут изгибаться в сторону движения дуги. Вследствие избирательности процесса кристаллизации перед фронтом будет накапливаться примесь и центральные части шва будут обогащены примесью. В зависимости от формы сварочной ванны (глубокая и узкая) кристаллы будут расти навстречу друг другу, образовывая транскристаллитную структуру, которая крайне не желательна, поскольку может вызвать образование трещин в середине шва. Для измельчения крупно дендритной литой структуры сварных швов применяют:
Модифицирование - введение в сварочную ванну готовых центров кристаллизации, в виде порошков тугоплавких металлов;
Применение в процессе сварки механических колебаний ванны, или электромагнитного перемешивания жидкого металла;
Применение, по возможности многопроходных швов. термическая или термомеханическая обработка сварного шва.
Кроме расплавления металла сварочный источник воздействует также на основной металл. Количество вносимого тепла определяется погонной энергией источника: отношение мощности к скорости сварки (q/v) Процесс распространения тепла описывается температурными полями. Температурным полем называют совокупность значений температуры в данный момент во всех точках пространства (тела). Температурное поле удобно характеризовать изотермами. Изотермические поверхности являются геометрическими местами точек тела, имеющими одинаковую температуру. Геометрические места точек пересечения изотермической поверхности с какой-либо поверхностью является изотермой. В частном случае нагрева металлического листа каким-либо неподвижным сосредоточенным сварочным источником тепла (дугой, газовым пламенем, электронным лучом) изотермы на наружной поверхности будут представляться окружностями. При этом каждая точка основного металла, находящаяся на некотором расстоянии от оси шва, будет вначале нагреваться, а затем охлаждаться. Кривая, описывающая изменения температуры точки во времени называется термическим циклом. Основными характеристиками термического цикла есть: максимальная температура, время нагрева, время охлаждения Особенно важными параметрами является максимальная температура, так как она определяет возможность протекания структурных превращений в металле и время охлаждения, которое связано со скоростью охлаждения - одним из основных факторов вероятности получения закалочных структур.
Металл однопроходного шва имеет структуру литой стали. При многослойном сваривании последний шов имеет крупнозернистую структуру литой стали, а предыдущие швы, вследствие термического действия - структуру с мелкими зернами феррита и перлита. После процесса кристаллизации и перитектического преобразова-ния шов имеет структуру аустенита, зерна которого образовываются на границах первичных столбчатых кристаллов. При снижении температуры структурных изменений не будет до температуры Аr3. Потом начнутся преобразования в твердой фазе - вторичная кристаллизация. Будет выделяться феррит, а аустенит будет обогащаться углеродом и при температуре 727°С произойдет эвтектоидное преобразование As → Фр + Цк. Высокие скорости охлаждения металла сварного шва влияют на характер преобразований, которые рассматривались для равновесных условий. Необходимо следующие особенности вторичных преобразований:
1. Феррит, что выделяется при переходе через температуру, что характеризуется линией GS не успевает весь выделиться и потому аустенит в момент эвтектоидного преобразования будет иметь меньше углерода чем 0,8%.
2. В результате эвтектоидного преобразования образовывается большее количество перлита с меньшим содержимым углерода, чем при равновесных превращениях (за счет смещения точки S вниз и влево).
3. Образовывается перлит, который имеет более тонкое строение. Скорость охлаждения металла шва изменяется в очень широких границах. В начальный момент она составляет 200 - 300 град/с, а затем быстро снижается.
Таким образом, зоны металла, которые имели большую скорость охлаждения, будут иметь мелкозернистую перлитную структуру, причем количество перлита будет больше чем при равновесных условиях. По химическом составу металл шва обычно отличается от основного металла, так как имеет литую структуру, которая имеет худшие механические свойства, чем основный металл, и для обеспечения условия равнопрочности металл шва легируют специальными элементами, которые повышают его механические свойства. Кроме этого, как правило, металл шва всегда имеет меньшее содержание углерода, чем основный металл, благодаря особым условиям, которые имеют место при сварке.
Зона основного металла, в которой за счет нагрева и охлаждения происходят изменения структуры и свойств, называется зоной термического влияния (ЗТВ). Ширина зоны заканчивается температурой около 100°С. и, при сварке может изменяться в зависимости от режима и способа сварки от десятых долей миллиметра до 40 - 50 мм.
При сварке низкоуглеродных сталей (0,1 - 0,25% С) ЗТВ в основном состоит из таких участков:
1. Участок неполного расплавления - это зона металла, который нагревался до температур, которые лежат между линиями солидус и ликвидус. При дуговых методах сварки участок небольшой и крайне трудно различим.
2. Участок перегрева - включает металл, который нагревался от 1100 – 1200°С до температуры солидус, характеризуется крупным зерном и низкими механическими свойствами. Часто в перлите наблюдаются пластинки феррита, которые выделились под углом 120° (такая структура носит название видмандштеттова). Участок сплавления и участок перегрева вместе называются еще околошовной зоной (ОШЗ). В ОШЗ структура и свойства резко отличаются от основного металла: снижается пластичность и ударная вязкость, образовываются горячие и холодные трещины.
3. Участок нормализации - включает металл, который был нагрет выше температуры (Ас3) до – 1100 - 1200°С. Процессы перекристаллизации дают мелкие зерна аустенита, которые не успевают вырасти и при превращении дают мелкие зерна феррита и перлита. Эта структура и участок имеет очень хорошие механические свойства.
4. Участок неполной перекристаллизации - зона металла, который был нагрет между температурами 727°С (Aс1) и Ас3. На этом участке могут быть крупные зерна феррита, который не прошел перекристаллизацию, а также мелкие зерна перлита, которые образовались с аустенита, поэтому этот участок имеет относительно невысокие механические свойства.
5. Участок рекристаллизации - металл нагрет выше температуры рекристаллизации (для железа Трек = 0,4 Тпл = 450°С) и до 727°С. Если металл не имел холодной пластической деформации перед сваркой, то этого участка не существует, а если такая деформация имела место, то получим крупные зерна, феррита и перлита, причем размер зерен будет определятся степенью пластической деформации.
6. Участок синеломкости - металл нагрет от 100°С до 500°С. Этот участок не имеет видимого изменения структуры, тем не менее характеризуется снижением пластических свойств, которое вызвано выделением с твердого раствора феррита субмикроскопических частичек различных примесей, которые располагаются по границам зерен.
В ЗТВ проходят также диффузные процессы. В зависимости от температуры и времени выдержки можно наблюдать диффузию углерода и иных элементов с ОШЗ и наоборот. Примером такого процесса есть проникновение меди в основный металл при наплавке меди на сталь, снижение содержания углерода в ОШЗ при наплавке швами, которые содержат элементы, с которыми углерод образовывает нерастворимые соединения (карбиды).
В зависимости от реальных условий процесса сварки, температуры, скорости нагрева и охлаждения различных участков металл сварного соединения неоднороден и состоит из следующих зон (рис. 2).
Металл шва - это та зона, в которой в связи с нагревом выше температуры плавления (линии ликвидус) свариваемый металл расплавляется в процессе сварки, перемешивается с металлом электрода и затем кристаллизуется. Металл шва имеет литую дендритную структуру и состоит из кристаллов столбчатой формы. Особенностью кристаллизации сварочной ванны является то, что в отличие от кристаллизации отливки в литейной форме, кристаллизация металла шва протекает при одновременном его подогреве со стороны источника тепла и быстром охлаждении за счет интенсивного теплоотвода в основной холодный металл.
Рис. 2. Макроструктура нахлесточного сварного соединения
Зона сплавления - расположена на границе основного металла и металла шва. В данной зоне выделяется участок с крупными зернами, т. е. участок металла, который в процессе сварки нагревался до температуры выше линии солидус, но ниже линии ликвидус (в данной температурной области происходит частичное расплавление основного металла). В нее попадают химические элементы из металла электрода (из сварочной ванны). В месте примыкания к границе сплавления основного металла со швом, из-за большой разницы химического состава основного и электродного (присадочного) металлов может образоваться химическая неоднородность. Эта неоднородность может привести к скачкообразному изменению физико-механических свойств металла околошовной зоны и снижению надежности сварного соединения. Ширина зоны сплавления изменяется в пределах 0,1-0,4 мм и зависит от химического состава свариваемого металла (от температурного интервала "ликвидус - солидус"), от способа и режима сварки.
Зона термического влияния - часть основного металла, примыкающая к сварному шву, с измененными в процессе сварки структурой и свойствами. Общая ширина ЗТВ зависит от условий нагрева и охлаждения, от теплофизических свойств и толщины свариваемого металла, от метеоусловий и пр. (при дуговой сварке она составляет - 2-6, а при газовой - до 30 мм).
Изменение структуры в околошовной зоне, например на однопроходном стыковом соединении, можно проследить, поместив над сечением сварного соединения кривую распределения максимальной температуры, совместив ее в том же масштабе температуры с диаграммой состояния железо-цементит. Намечая на диаграмме состояния сплавов характерные зоны и участки, перенесем их границы на график распределения температуры (рис. 3). Из точек пересечения горизонтальных линий с кривой охлаждения опустим перпендикуляры на рисунок сечения сварного соединения. Это позволит определить линейные границы отдельных участков зоны термического влияния.
Рассмотрим зону термического влияния сварного соединения (см. рис. 3):
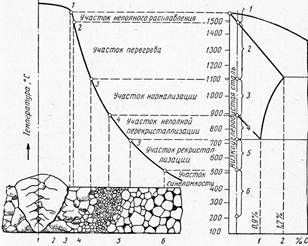
Рис. 3. Схема строения сварного шва
1 - переходный участок или участок сплавления, обычно размер его невелик. Интервал температуры, для стали 20, около 1490-1520°С. Структура стали - крупнозернистая, возможно образование видманштеттовой структуры;
2 - участок перегрева. Металл нагревается выше 1100°С, до температуры, близкой к линии солидус. В этом интервале температуры за счет роста зерна аустенита формируется крупнозернистая структура перегретой стали с пониженной ударной вязкостью. Часто на этом участке образуется видманштеттова структура (крупнозернистая с зернами феррита иглообразной формы), что еще больше повышает хрупкость стали. Ширина этого участка - 1-3 мм;
3 - участок нормализации. Металл нагревается выше третьей критической точки Ас3 (от 900 до 1100°С). В процессе полной перекристаллизации в аустенит, на этом участке образуется мелкозернистая (сорбитообразная) структура, которая обеспечивает более высокие механические свойства стали, по сравнению со свойствами исходного металла и свойствами других участков зоны термического влияния. Ширина этого участка - 1,2-4 мм;
4 - участок неполной перекристаллизации. Металл нагревается до температуры 725-850°С (между первой Ас1 и третьей критическими точками Ас3). Процесс измельчения зерна происходит только за счет перекристаллизации той части структуры, которая занята перлитом, а размер зерен феррита не изменяется. Поэтому сталь на этом участке может состоять не только из мелких зерен, но и отдельных крупных зерен феррита. Сталь с разнозернистым строением имеет более низкие механические свойства, чем мелкозернистая сталь. Ширина этого участка - 0,7-4 мм;
5 - участок рекристаллизации. Температура нагрева этого участка ниже первой критической точки Ас1 (727°С). При сварке горячекатаной или отожженной стали, на этом участке ЗТВ никакие структурные изменения в металле не происходят.
6 - участок синеломкости. Температура нагрева металла на данном участке сварного шва в интервале 200-400°С, при котором на поверхности стали появляются синие цвета побежалости (пленки окислов). Характеризуется тем, что прочность и твердость металла повышаются, а пластичность и ударная вязкость - резко падают. Это явление получило название "синеломкость". Вероятной причиной этого является старением металла - выделение по границам зерен из пересыщенного твердого раствора дисперсных карбидов и нитридов.
Зона термического влияния - это неотъемлемая часть сварной конструкции и её свойства будут определять общую несущую способность этой конструкции.
Есть некоторые значимые свойства, которые необходимо обеспечивать почти в любом случае. К таким свойствам относится стойкость зоны термического влияния к хрупкому разрушению.
Хрупкое разрушение - это развитие дефектов сварного шва (чаще всего трещин) с высокой скоростью. Хрупкое разрушение может начаться от уже имеющихся трещин и других дефектов, например, непроваров или шлаковых включений.
Ещё одним необходимым свойством для зоны термического влияния является сопротивление усталости. Но, как правило, отдельно эту зону испытать очень трудно и испытаниям подвергают всё сварное соединение.
Как уже говорилось, отдельно испытать зону термического влияния на прочность затруднительно ввиду её малой ширины. Косвенную оценку прочностным свойствам можно дать, если измерить твёрдость зоны.
Наибольшее возможное значение твёрдости в зоне термического влияния (да и, вообще, в металле), зависит, в основном, от содержания углерода в составе стали. Углерод сильно влияет на свариваемость стали. Давая оценку свариваемости сталей, можно утверждать, что стали с низким содержанием углерода (менее 0,20%), свариваются без ограничений. А стали с повышенным содержание углерода (более 0,25%), уже необходимо сваривать с предварительным подогревом, последующей термообработкой (отпуском или отжигом) и контролем погонной энергии сварки.
Процесс кристаллизации сварочной ванны.
Хорошо свариваются те металлы и сплавы, которые в своеМ составе имеют элементы, обладающие неограниченной взаимной растворимостью как в жидком, так и в твердом состоянии. Такие металлы и сплавы не будут образовывать соединения, вызывающие охрупчивание сварного соединения. Хорошую взаимную растворимость имеют железо и никель, железо и ванадий, железо и хром, молибден и тантал, никель и вольфрам, никель и медь, никель и кобальт, хром и молибден, хром и ванадий, хром и титан и т.д.
Процесс кристаллизации сварных швов отличается от кристаллизации слитков высокими скоростями кристаллизации, поскольку после интенсивного нагрева металла концентрированным источником тепла происходит быстрый отвод тепла в свариваемое отделение. Скорость охлаждения сварных швов исчисляется десятками и сотнями градусов в секунду.
Кристаллизацию сварных швов изучают металлографическим методом, путем исследования образовавшейся структуры. Металлографическим методом установлено, что в верхней части швов располагаются наиболее крупные, а в нижней наиболее мелкие кристаллиты. В средней части швов кристаллиты имеют удлиненную форму (транс-кристаллитное строение), р в верхней части швов ветвистую форму (дендритное строение).
Процесс кристаллизации сварных швов осуществляется прерывисто, чем объясняется появление кристаллизационных слоев, каждый из которых состоит из нескольких основных участков (рис. 24):
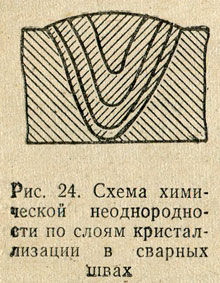
нижнего - с небольшим содержанием углерода, серы и фосфора (имеющего наиболее интенсивное почернение при травлении); среднего - наиболее широкого, характеризующегося сравнительно однородным почернением и содержащего углерод, серу и фосфор в тех же количествах, что и металл шва, а также верхнего, - характеризующегося интенсивным ослаблением почернения.
Первый участок возникает в результате кристаллизации тонкой прослойки жидкого металла, примыкающей к оплавленной поверхности, которая обогащена углеродом, серой и фосфором, переместившимися из примыкающих участков основного металла.
Второй участок кристаллизуется из жидкого металла исходного состава. Вследствие большой скорости кристаллизации затвердевший металл ванны по однородности близок к жидкому металлу, из которого он образовался. Третий участок слоя в верхней части второго участка формируется более обедненным углеродом, серой и фосфором.
Образование последующих слоев происходит таким же способом. При формировании столбчатых кристаллитов из каждого оплавленного кристаллита основного металла вырастает целая группа одинаково ориентированных дендритов, составляющих столбчатый кристаллит. Направленность главных осей дендритов определяется направлением теплоотвода, а геометрические размеры дендритов зависят от геометрических размеров столбчатых кристаллитов. Более крупным столбчатым кристаллитам соответствуют более крупные разветвленные дендриты. В процессе затвердевания сварных швов перед фронтом растущих кристаллитов маточный раствор насыщается различными примесями. В самую последнюю очередь затвердевает средняя часть швов, поэтому обычно в ней сосредоточивается максимальное количество примесей.
Структуры сварных швов.
При изучении металла сварного шва различают макро- и микроструктуру. Макроструктура
рассматривается невооруженным глазом или при небольших (до 10 - 15-кратных) увеличениях. Структура металла, увеличенная более чем в 60 -1 00 раз, называется микроструктурой
.
Макро- и микроструктура бывает первичной и вторичной. Первичная структура образуется непосредственно а процессе затвердевания расплава; вторичная - в результате фазовых (термических) превращений. Сварные швы имеют целый комплекс структур наплавленного металла и металла, который в процессе сварки подвергался нагреву. Рассмотрим различные участки структуры сварного шва (рис. 25).
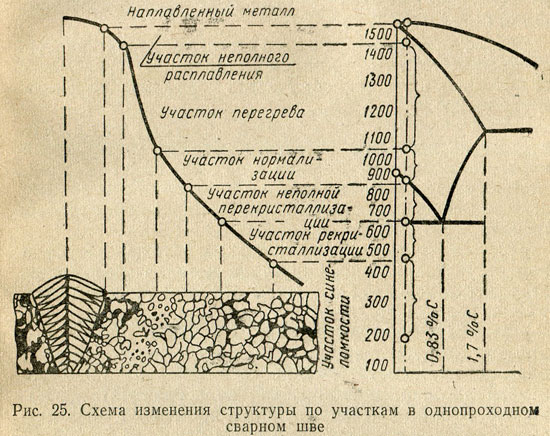
Участок наплавленного металла
(шва) имеет столбчатое строение. Столбчатые кристаллиты от переходной зоны между участком неполного расплавления и наплавленным металлом направлены вглубь шва. Кристаллит состоит из отдельных дендритов, имеющих общую направленность, которые иногда могут иметь и различную разветвленность. Группа дендритов, имеющая четкую границу, составляет столбчатый кристаллит. В корне шва, ближе к переходной зоне, составляющие столбчатый кристаллит дендриты разветвлены минимально.
На участке неполного расплавления
первичная структура характеризуется химической неоднородностыо. Вторичная структура этого участка напоминает видманшеттову структуру. Видманшеттова структура - это структура стали с прямолинейным расположением волокон). Эта зона невелика и для дуговой сварки составляет от 0,1 до 0,5 мм
.
На участке перегрева шва
может образоваться крупнозернистая структура, которая придает металлу наименьшую пластичность и ударную вязкость. Чтобы уменьшить протяженность участка перегрева, следует увеличить скорость сварки или выполнить сварку за несколько проходов. Ширина зоны участка перегрева иногда достигает 3 - 4 мм
.
Участок нормализации шва
характеризуется мелкозернистым строением металла. В зависимости от размеров швов ширина участка нормализации колеблется от 0,2 до 4 - 5 мм
.
На участке неполной перекристаллизации
не все зерна основного металла подвергаются перекристаллизации. Ширина этой зоны от 0,1 до 5 мм
.
Рекристаллизационный участок
появляется при сварке пластических деформированных сталей, ширина этого участка составляет 0,1 - 1,5 мм
.
Участок синеломкости
расположен за участком рекристаллизации. Структура металла здесь не отличается от исходной структуры. На этом участке температура нагрева достигает 200 - 400° С.
Методы выявления структуры сварных швов.
Для этого из металла сварных швов приготовляют шлифы - образцы изучаемого металла со специально подготовленной плоской (шлифованной, полированной) поверхностью. Для выявления структуры применяют механическое, химическое, электролитическое полирование и окислительное травление.
Причины образования горячих и холодных трещин в сварных соединениях.
В процессе сварки могут образовываться трещины. Горячие трещины образуются в условиях повышенных температур из-за большой усадки при охлаждении металла сварочной ванны и из-за изменения состава свариваемых материалов. Большой склонностью к горячим трещинам, например, обладают сплавы, содержащие около 5% хрома и от 1,0 до 2,5% углерода, и сплавы с 9 - 10% хрома при содержании 0,9 - 1,2% углерода.
Холодные трещины образуются в металле шва и околошовной зоны из-за резкого изменения механических свойств, а также характера напряженного состояния вследствие фазовых и структурных превращений. В образовании холодных трещин при сварке сталей существенную роль играет водород, который выделяется из твердого раствора в имеющиеся в металле микрообъемы (пустоты). В них выделившийся атомарный водород соединяется в молекулы и создает в окружающем объеме металла внутреннее давление, которое образует высокое напряжение, способствующее образованию трещин при нагрузке и даже без нагрева.