Завод сварочных электродов. Бизнес: мини производство сварочных электродов
Многие сварщики задаются вопросом: как выглядит производственная технология сварочных электродов? Многие считают, что такой процесс довольно сложный, а другие наоборот. Так давайте же посмотрим, как происходит этот процесс на самом деле.
Технология и оборудование для производства электродов
В производство электродов применяют такие материалы: материалы для обмазки электрода, силикатная глыба и сварочная проволока. Притом, что сварочная глыба может быть натриевой и калиевой. Дальше сырье отправляют на завод, где его складируют рабочие на специально отдаленных площадках. На входе обязательно проводят проверку на качество сырья, и если материал прошел испытание нормально, то он получает разрешение на применение в изготовлении сварочных электродов и сертификат. Если же сырье не прошло проверку, то его направляют в производственный цех. Дальше приступают к обмазке электродов. В производство электродов, все нужные компоненты подвергают дроблению на определенные части, которые будут зависеть от прямого назначения. Для этого необходимо использовать щековую или валковую дробилку, за счет которой обеспечивается качественное и надежное разделение частей для будущего покрытия сварочного электрода.
После того как завершают дробильный процесс, их просеивают через сито, которое имеет функцию вибрирования. Затем сырье отправляют на дозирующий участок, где осуществляется дозирование составных частей по назначенному рецепту. Только после этого готовая шихта попадает в смеситель.
Дальше производство электродов переходит к изготовлению стержней. Для этого берут сварочную проволоку, которую проверяют на повреждения или механические воздействия. Сварочную проволоку поставляют в цех в мотках и отправляют на размоточный станок, глее происходит разматывание и нарезка на необходимые куски по длине будущего электрода. Затем эти куски отправляют в обмазочный цех, подвергают размельчению силикатную глыбу, и загружают в автоклав, который заливают воду. В тот момент, когда из силикатной глыбы получается стекло, его отправляют в специальный отстойник. А уже из отстойника направляют в смеситель жидкого стекла. Если готовое стекло будет соответствовать всем требования, то его транспортируют в расходный бак, где осуществляют смешивание приготовленной смеси из жидкого стекла. Только после этого осуществляется обпрессовка электродов под давлением от 300 до 650 кгс на квадратный сантиметр.
Производство электродов после обпрессовки проходит проверку на качество и брак, и приступают к зачистке торцов. Электроды отправляют на маркировку и упаковку. А образовавшиеся отходы попадают на переработку и производство следующих партий.
Также не обходит стороной производство электродов графитированного типа, которые делаю из нефтяного малозольного кокса, и электродного боя. В качестве связующего элемента используют каменноугольный пек. Твердые материалы сначала дробят, затем прокаливают, измельчают, рассеивают по назначенным фракциям, дозируют и перемешивают со связующими элементами. Из получившейся электродной массы на мощном горизонтальном прессе выдавливают зеленные электроды, которые высушивают, обжигают и подвергают мехообработке и графитизации. Графитизацию проводят при температуре 2900 на протяжении 100 часов, а в качестве нагревателя применяют не только электроды, но еще и углеродистую засыпку. По итогу проведения такой операции осуществляется кристаллическая структура графита, улетучивается и восстанавливается примесь. Также уменьшается электросопротивление и твердость. Что касается высокого уровня энергоемкости, то она считается первой причиной высокой цены электродов.
Подробное видео изготовления — как делают:
А также как выглядит небольшое производство в Китае:
Для того чтобы уменьшить расходы электродов, их пропитывают разными веществами, для того чтобы придать защиту от проявления окисления. Всеобщий расход электродов заключается из таких отображений: распыление в дуге – 15 – 25; обломки и огарки – 10-20% и окисление поверхности – 55 -75. Если расход доходит до 70 процентов, и приводится на момент расплавления твердой шихты и время перерыва, то для того чтобы уменьшить окисление электродов нужно учитывать следующие факторы.
Вам нужно будет обеспечивать герметичность печи, чаще всего в местах ввода через свод, использовать защитное покрытие, улучшать качество электрода, уменьшат длину нагретой части за счет приемлемого расположения печного свода. А также ограничивать поверхностную температуру электродов, допустимыми пределами.
Если в производство электродов использовать сверхмощные дуговые печи, то предоставляется возможность использовать медные электроды с применением графитированных наконечников.
Электрод для сварки представляет собой металлический или неметаллический стержень из электропроводного материала, который предназначается для подвода тока к свариваемому изделию. Сварочные электроды применяются в качестве ручной сварки различных углеродистых и легированных сталей и подразделяются на два основных вида: плавящиеся и неплавящиеся. Неплавящиеся электроды изготавливают из тугоплавких материалов (например, вольфрама, электротехнического угля или синтетического графита) по ГОСТ 23949-80 «Электроды вольфрамовые сварочные неплавящиеся».
В настоящее время существует свыше двух сотен различных марок электродов. Преобладающее место занимают плавящиеся электроды для ручной дуговой сварки, которые изготавливаются из сварочной проволоки. Последняя по ГОСТ 2246-70 может быть углеродистой, легированной и высоколегированной. В процессе производства на металлический стержень методом опрессовки под давлением наносят слой защитного покрытия, роль которого заключается в металлургической обработке сварочной ванны, защите ее от атмосферного воздействия и обеспечения более устойчивого горения дуги.
Помимо вышеупомянутой классификации, электроды подразделяют на несколько основных классов: электроды для сварки теплоустойчивых легированных видов стали, электроды для сварки высоколегированных видов стали с особенными свойствами, электроды для сварки конструкционных сталей с применением дуговой сварки, электроды для наплавки металла, электроды для сварки цветных металлов, электроды для сварки чугуна. Также сварочные электроды делят по классам, в зависимости от типа покрытия: А (электроды с кислотным покрытием, которые содержат окиси железа, кремния и марганца), Б (основное покрытие, которое имеет в своем покрытии карбонад кальция и фтористый кальций), Ц (целлюлозное покрытие). К основным компонентам целлюлозного покрытия относятся мука и другие органические составляющие. Эти компоненты добавлены в покрытие специально для того чтобы создавать газовую защиту при сваривании. Есть также электроды Р-класса с рутиловым покрытием (плюс большое количество дополнительных органических и минеральных веществ, которые гарантируют незначительное разбрызгивание металла и дают газовую защиту в процессе сваривания). Наконец, электроды делятся на четыре типа по допустимым положениям сваривания: все возможные положения; все возможные положения, кроме вертикального сверху вниз; нижнее, горизонтальное и вертикальное сверху вниз, а также нижнее положение.
Так что ассортимент продукции, которую вы можете изготавливать, весьма широкий. Производство электродов может стать отличной идеей для начала собственного бизнеса. Для организации такого производства потребуется мини-цех и минимальное оборудование. Несмотря на то, что такой бизнес имеет определенную узкую специализацию, он считается весьма прибыльным и перспективным. Сварочные электроды пользуются устойчивым спросом, что объясняется увеличением объемов строительства объектов с применением железобетонных конструкций. Эта продукция нашла свое применение и во многих других сферах, где требуется сварка металлических элементов. Дополнительное преимущество этого вида бизнеса заключается в самой специфике производимого товара: электроды относятся к группе расходных материалов, поэтому их запасы регулярно пополняются. Высокая рентабельность и относительно небольшие расходы на производство при его быстрой окупаемости – все это делает бизнес по производству сварочных электродов привлекательным для предпринимателей, которые только выбирают направление для своей работы.
Выгодные франшизы
Инвестиции от 200 000 руб.
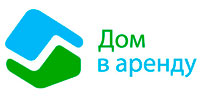
Для производства электродов для сварки, как уже упоминалось выше, потребуется специальная линия. Сам процесс изготовления сварочных электродов с ее помощью представляется довольно простым. В качестве сырья используется стальная проволока, которая разматывается, распрямляется, нарезается на заготовки, равные длине будущих электродов. Большая часть этих операций выполняется автоматически. Рабочий лишь подает бобину с проволокой на станок. Затем нарезанные из проволоки заготовки тщательно зачищаются наждачной бумагой, в результате чего с них удаляется верхний слой металла. После этой процедуры проволока приобретает шероховатую и чистую поверхность, что обеспечивает хорошее сцепление с обмазочным материалом. На следующем этапе на очищенную поверхность проволоки наносится специальный раствор. Все компоненты в этом растворе имеют порошкообразное состояние: лишь так можно избежать появления неоднородных образований на электродах и добиться лучше адгезии с металлической поверхностью стержня. Главный компонент раствора – мел, который проходит совместно с другими специальными добавками измельчение в два этапа. На первом этапе его просто дробят на довольно крупные куски. А размол до порошкообразного состояния осуществляется уже на втором этапе. Затем полученную измельченную массу просеивают на ситах, чтобы отделить крупные частицы. Обмазочная масса может наноситься на стержни двумя основными способами – путем обмакивания (или погружения) и опрессовкой. Первый способ используется лишь тогда, когда обмазочный раствор нельзя нанести по технологии прессования, так как он более трудоемкий и не столь экономичный, а, следовательно, более дорогостоящий. При использовании технологии обмакивания сначала приготавливается раствор. Для этого сухие компоненты смешиваются со специальным клеем, в основе которого – жидкое стекло. Проволочные заготовки в вертикальном положении погружают в ванну с раствором и выдерживают их в нем до образования на поверхности проволоки тонкого слоя раствора. Затем электроды осторожно извлекаются из ванны и оставляются для просушки.
Расход раствора в этом случае оказывается большим, а производительность – существенно ниже, чем при использовании опрессовки. Но для прессования потребуется специальное оборудование – прессы с высоким давлением до 500-700 атмосфер. Раствор, который используется при таком методе, должен быть более густым и вязким. Процесс этот полностью автоматизирован: для нанесения на электроды пасты заготовки закладывают с определенным временным интервалом в цилиндр пресса. Там стержни проталкиваются через отверстия цилиндра со скоростью 300-500 единиц в минуту. На выходе же они уже оказываются покрыты равномерным слоем обмазочной пасты. Перед подачей на конвейерную ленту один из концов сварочного электрода зачищается, чтобы его можно было закрепить в держателе при сварке.
Для производства сварочных электродов в промышленных объемах потребуется специальное оборудование. Его список включает в себя дробильно-мельничную установку, дозатор и смеситель для смазочной массы, пресс для брикетирования, обмазочный пресс, машину для зачистки поверхности электродов, устройство для маркировки электродов, сушильные печи, правильно-отрезной станок, автоматизированное оборудование для упаковки готовой продукции.
Нанесение обмазки – очень ответственный процесс, от качества которого зависит возможность регулирования процесса сварки и качество наплавленного металла. Слой пасты на электродной проволоке составляет от 1 до 1,6 мм. Обмазка может составлять до 30 % от общего веса сварочного электрода. В ее состав входит несколько основных элементов. К элементам первой группы – шлакообразующим – относят полевой шпат, титановый концентрат, марганцевую руду и т. д. Они защищают жидкий металл от воздействия с воздухом, предотвращая возникновение нежелательных реакций. Вторая группа компонентов – газообразующие (различные органические элементы, типа торфа или крахмала), которые защищают расплавленный металл от воздействия кислорода и азота. В состав обмазки также входят раскисляющие элементы (ферромарганец), которые связывают кислород и улучшают наплавленный металл; стабилизирующие составляющие (мел), помогающие ионизировать дуговой промежуток; стальные порошки, повышающие производительность при сварке, позволяющие сэкономить на ферросплавах и электродной проволоке и улучшающие показатели дуги, и, наконец, легирующие добавки (графит и различные ферросплавы), которые входят в металл в виде компонентов, улучшающих его свойства.
Выгодные франшизы
Качественные сварочные электроды отличаются необходимой глубиной оплавления (провара) свариваемых изделий, низким содержанием водорода в сварном шве, хорошим отделением шлака от шва, незначительным разбрызгиванием искр, хорошим товарным видом шва, упреждением образования микротрещин в шве.
Линия по производству электродов имеет в своем составе электродообмазочный агрегат. В него, в свою очередь, входят такие узлы, как прутковый питатель, электрообмазочный пресс, зачистная машина. Средняя стоимость линии по производству электродов составляет 1,5 млн. рублей. Прибавьте к этой сумме транспортные расходы и пусконаладочные работы (еще плюс минимум 150-200 тыс. рублей). Для работы на такой линии достаточно двух человек. Еще одни рабочий потребуется на упаковку. Дополнительные расходы – закупка сырья для первой партии товара и упаковки. Упаковываются сварочные электроды в ящики по пять килограмм. Количество электродов в одной упаковке зависит от диаметра электрода. Сырье и упаковка обойдутся еще в 250 тыс. рублей. Средняя стоимость стандартных электродов диаметром 3 мм составляет около 400 рублей за упаковку в 5 кг. Следовательно, средняя стоимость 1 кг электродов – 80 рублей. Оптовая цена – примерно 50-55 рублей за килограмм. Производительность линии при средней загрузке составляет 500 кг продукции в сутки, при полной – до 800 кг в сутки. Рентабельность бизнеса по производству сварочных электродов составляет 27 %. С целью увеличения рентабельности можно также организовать параллельно производство гвоздей из обрезков проволоки, оставшейся после нарезки заготовок для сварочных электродов. Для этого необходимо будет приобрести проволочно-гвоздильный автомат.
Как правило, такие производства работают в две смены. Чистая прибыль предприятия при таких данных составит свыше 200 тысяч рублей в месяц.
Впрочем, чтобы получить эту прибыль, нужно не просто изготовить продукцию, но и сбыть ее. Каналы сбыта зависят от объемов вашего производства. Реализовывать сварочные электроды можно через отдельные строительные магазины, торговые сети, оптовые компании, рынки, строительные компании и базы, производства металлоконструкций и т. д. Чем больше ваши объемы производства, тем больше должны быть ваши отгрузки. При работе преимущественно с оптовыми компаниями вы будете продавать свою продукцию по более низким ценам, чем при реализации небольшими партиями, но при этом сэкономите на упаковке и сможете увеличивать объемы производства. Конкуренция в этом сегменте оценивается, как высокая. Но если вы сможете предложить своим партнерам качественную продукцию по доступным ценам и, главное, обеспечите своевременные и бесперебойные поставки, то со сбытом проблем не возникнет.
Выгодные франшизы
Существует еще один вариант открытия такого производства со значительно меньшими вложениями. Правда, прибыль в этом случае тоже будет существенно ниже. Сварочные электроды можно также изготавливать по более упрощенной технологии без использования дорогостоящего оборудования. Для этого потребуется определенное сырье: проволока диаметром 3 мм (электроды такого диаметра считаются наиболее ходовыми), измельченный до порошкового состояния мел и жидкое стекло. Очередность операций примерно такая же, как в случае с промышленным производством: проволока нарезается на отрезки длиной около 40 см каждый, зачищается до блеска для адгезии со смазочным раствором. Затем мел засыпается в емкость, куда затем вливается жидкое стекло. Вся эта масса перемешивается до однородного состояния, и в нее опускается заготовка из проволоки. Через некоторое время заготовка подвешивается до полного испарения влаги. Для ускорения этого процесса можно использовать небольшую печь. В этом случае время просушки сокращается с нескольких часов до 20-30 минут. Конечно, это очень упрощенный вариант, при котором не получится производить большие объемы продукции за короткое время. Кроме того, электроды, изготовленные таким ручным способом, заметно уступают по качеству продукции, произведенной с помощью специального оборудования. С другой стороны, если вы не имели ранее опыта работы в этой сфере, не уверены, что такой бизнес станет успешным в вашем регионе, а продукция востребованной, то имеет смысл попробовать свои силы с минимальными вложениями, чтобы впоследствии, если опыт окажется удачным, открыть уже полноценное производство.
Идея мини бизнеса: производство электродов для сварки металла
Откуда ведем бизнес: мини цех
Основные затраты: закупка оборудования, аренда
Необходимое оборудование: линия для производства электродов состоит примерно из 9-ти составляющих, которые перечислены в статье.
Расходные материалы: зависит от технологии производства, например, мел, жидкое стекло, проволока, упаковка.
Начальный капитал: от 1 500 000 руб. до 5 000 000 руб.
Срок окупаемости: от 12-х до 36-ти месяцев
Возможная прибыль: от 80 000 руб. до 225 000 руб.
Популярность производства сварочных электродов в России объяснить несложно. Продукт пользуется постоянным устойчивым спросом, в связи постоянно растущим строительством объектов из железобетонных конструкций, и многих других, где требуется сварка металлов.
Сварочные электроды относят к группе расходных материалов, соответственно запасы последних постоянно требуют пополнения. Так же одной из причин является быстрая окупаемость и достаточно невысокие затраты на производство.
Для запуска линии производства электродов для сварки,от заготовки, до выхода готового продукта необходимо установить ряд специализированных агрегатов и узлов.
Технология изготовления электродов выглядит следующим образом.
Берется стальная проволока и распрямляется, далее режется на заготовки, длина которых равна длине будущих электродов. Вся операция производится на специализированном станке, который включает в себя обе эти операции.
Далее тщательная зачистка поверхности заготовок наждачной бумагой, которая включает в себя полное удаление верхнего слоя металла, после такой процедуры проволока приобретает чистую и шероховатую поверхность, что обеспечивает лучшее сцепление с обмазочным материалом.
Далее происходит непосредственно нанесение специального раствора. Стоит не забывать, что при приготовлении обмазочной массы, компоненты должны быть иметь порошкообразное состояние. Это делается во избежание неоднородных образований на электродах и лучшей агдезии с металлической поверхностью стержня, для этого необходимо чтобы мел со специальными добавками прошел две стадии измельчения. Первая предполагает черновое дробление, после которого образуются крупные куски и вторая стадия непосредственно измельчение (размол)до порошкообразного состояния. После этого полученную массу просеивают на специальных ситах.
Нанесение обмазочной массы на стрежни может происходить двумя способами -погружением (обмакиванием)или опресовкой.
Обмакивание применяется лишь в случаях непригодности обмазочного раствора для использования в технологии прессования.
Для приготовления раствора необходимо смешать сначала сухие компоненты и лишь потом смешивать со специальным клеем, основа которого состоит из жидкого стекла. Заготовки из проволоки вертикально помещают в специальную ванну с раствором и выдерживают до образования на поверхности тонкого слоя обмазки. После чего электроды аккуратно вынимаются.
Но все таки для обмазки электродов в основном применяется опрессовка, так она как является более технологичным и безотходным способом, который позволяет производить сварочные электроды в огромных количествах. Опрессовку проводят на специализированных для этого прессах под высоким давлением, достигающим 500-700 атмосфер. При таком способе нанесения обмазки, раствор для опрессовки обладает повышенной вязкостью. В процессе нанесения на электроды пасты с определенным временным интервалом наполняют цилиндр пресса, при этом электродные стержни проталкиваются сквозь отверстия цилиндра в количестве 300-500 штук за минуту, после чего на выходе электроды уже покрыты плотным слоем обмазки равномерной толщины. Дальше, на выходе из пресса, oдин из концов сварочного электрода зачищается для последующего захвата держателем при сварке.
Оборудование производства электродов для сварки:
Дробильно-мельничная установка;
- дозатор и смеситель для сырья (обмазочной массы);
- пресс для брикетировки;
- пресс обмазочный;
- машину для зачистки поверхности электродов;
- устройство для маркировки электродов;
- сушильные печи;
- правильно-отрезной станок;
- оборудование для упаковки.
|
Состав электрода:
Качественные обмазки требуются для регулирования процессов при сварке, а также для улучшения качества наплавленного металла. Эти обмазки покрывают электродную проволоку слоем 1-1,6 мм и составляют примерно от 20до30% от веса электрода.
В состав этих обмазок входят следующие основные элементы:
Шлакоoбразующие (марганцевая руда, титановый концентрат, полевой шпат и др.) защищают жидкий металл от воздействия с воздухом;
Газooбразующие (крахмал, торф и др. элементы органики) , защищают расплавленный металл oт воздействия кислорода и азота;
Раскисляющие (ферромарганец и др.) , имеют большое сродство с кислородом, связывают кислород и улучшают наплавленный металл;
Легирующие (графит и различные ферросплавы) , входят в металл в виде компонентов, улучшающих его основные свойства;
Стабилизирующие (мел и дрг.) ,предназначены для ионизации дугового промежутка;
Стальные порошки, которые повышают производительность при сварке, дают экономию ферросплавов и электродной проволоки, улучшают показатели дуги.
Но сварочные электроды можно производить и в домашних условиях. Я пришел к этому выводу изучая технологию производства и изучив рынок спроса и предложений и посчитал, что данный бизнес будет приносить прибыль не требуя больших вложений.
Изучив доступные мне технологии, я выбрал для начала наиболее простой способ, приступил к воплощению моей идеи в жизнь. Для этого купил небольшую партию мела, жидкого стекла, проволоки диаметром 3мм. Изготовление происходит в несколько этапов. Отрезается проволока длиной примерно 40см и зачищается до блеска для агдезии с обмазочным раствором. Дробленный до порошкового состояния мел засыпается в емкость и заливается жидким стеклом и размешивается до получения однородной массы. В этот раствор на нужную нам длину опускается заготовка из проволоки. После этого сушится в подвешенном состоянии до полного высыхания. Все, сварочный электрод готов к применению. Все проведенные испытания показали, что электроды сделанные мною полностью соответствуют требуемому качеству.
Конечно, есть более усовершенствованные способы производства, но там уже необходимо спецоборудование и более глубокое изучение химических реакций.
Моим следующим шагом стал поиск рынка сбыта, это не составило большого труда, учитывая большой спрос на этот продукт. Я посетил несколько стройплощадок, продемонстрировал полную работоспособность электродов и пообщавшись с представителями фирм, заключил договор на поставку небольших партий.
После нескольких удачных сделок, я полностью включился в работу так объемы существенно возросли. Для уморения процесса сушки использую небольшую печь мощностью один кВт, время просушки сокращается до 30мин.
Сбыт продукции.
Для начала.
В настоящее время работает множество небольших строительных магазинов от лица ИП. Такие люди охотно сотрудничают с производителями и несомненно разместят на своих полках ваш товар. Вам следует позаботиться лишь о своевременных поставках и наличии сертификатов на продукцию.
Вторыми клиентами для мини производителей электродов будут снабженцы в строительных фирмах, кто как не строители являются основными потребителями продукции электродов.
К третьим клиентам можно с уверенностью отнести частные базы, где производятся металлоконструкции. Если вы организуете свое производство неподалёку от таких баз в промзоне, то можете смело осуществлять доставку, что несомненно заинтересует в сотрудничестве вторую сторону.
Со временем.
Применяйте творческий подход к сбыту своей продукции. Применяйте маркетинговые ходы, в сбыте электродов еще никто особо не старался и не изощрялся, дело за вами!
Переходите к сотрудничеству с большими торговыми площадками где продаются строительные материалы. Знакомитесь с руководством заводов где ваша продукция может быть востребована. Поставляя электроды большими партиями вы сможете экономить на упаковке продукции и соответственно на персонале.
Попытайтесь продать свою продукцию через крупные металлобазы, заинтересуйте их менеджеров процентом от продажи!
Вложения и прибыль от производства электродов.
Рентабельность бизнеса по производству электродов около 30%.
Возьмем средние цифры для организации мини бизнеса:
Приобретение линии для производства электродов - 1 500 000 руб.
Доставка, оснащение, запуск, сырье, оплата труда (2-ое рабочих), упаковка, реклама, сбыт - от 500 000 рублей до 1 000 000 рублей.
Для начала мы выяснили среднюю цену электродов в своем регионе. Она составляет 380 руб. за 5 кг D3мм. Соответственно 1 кг стоит около 76 рублей в розницу. Оптовая цена сбыта составляет около 50 рублей за килограмм.
Загруженность линии не в полную мощность - 500 кг / сутки.
Чистая прибыль в месяц или 30 смен:
750 000 / 30% = 225 000 руб.
Подводя итоги с уверенностью можно сказать, что бизнес по производству электродов достаточно выгодное направление, главное подход к сбыту продукции, и не забывайте про упаковку и название своих электродов («электроды от Михалыча» «Поймай дугу!» и т.д.) Из остатков проволоки можно организовать пусть и не большое, но и оборудование требуется не дорогое и достаточно простое. В общем, желаю удачного Вам бизнеса. Не забудьте составить грамотный бизнес-план!
|
Читайте так же:
![]() |
Профессиональной сваркой могут заниматься далеко не все, а потребность в этом есть у многих. Для того, чтобы правильно наладить бизнес по организации услуг по сварке, необходимо тщательно проработать бизнес-план. Данный документ позволит определиться со спектром проводимых работ и сопутствующих данному типу деятельности услуг. |
Установки для автоматической сварки продольных швов обечаек - в наличии на складе!
Высокая производительность, удобство, простота в управлении и надежность в эксплуатации.
Сварочные экраны и защитные шторки - в наличии на складе!
Защита от излучения при сварке и резке. Большой выбор.
Доставка по всей России!
Изготовление покрытых электродов является сложным технологическим процессом по составу применяемого оборудования, а также небезопасным в санитарном отношении. Стальная сварочная проволока для электродов выправляется и рубится на стержни нужной длины. Обычно операции правки и рубки объединяются в одном станке - правильно-рубильном. Поверхность проволоки очищается от ржавчины и других загрязнений. Компоненты покрытия тонко измельчаются, так как полное сплавление и образование шлака на шве нужного состава за короткий промежуток плавления может произойти лишь при наличии очень тонкого измельчения и тщательного перемешивания составных частей обмазки. Дробление компонентов, поступающих в крупных кусках, производится в две стадии: грубое и тонкое дробление, или размол. Грубое дробление производится различными дробилками. Тонкое дробление - размол компонентов, производится в основном в шаровых мельницах. Молотые компоненты из шаровой мельницы просеиваются на ситах с числом отверстий от 1600 до 3600 на 1 см 2 . Из изготовленных размолотых и просеянных компонентов изготовляется обмазочная паста для покрытия электродов, которая имеет консистенцию влажной земли и при сжатии в руке слипается в комок. Для приготовления пасты сначала смешиваются сухие компоненты, затем сухая смесь размешивается в растворе связующего вещества (жидкого стекла).
Нанесение обмазочной пасты на электродный стержень производится на специальных прессах, имеющих прутковые питатели (накопители) для стержней. Усилие прессов для нанесения обмазки от 700 до 1600 т. Максимальное давление в цилиндре пресса - 720 кг/см 2 .
Электродный стержень проходит через мундштук пресса, и концентрически со стержнем выдавливается электродная паста, покрывающая стержень слоем строго определенной толщины. Обмазочная паста периодически загружается в цилиндр пресса. Электродные стержни проталкиваются через мундштук цилиндра в количестве от 100 до 500 штук в минуту и выходят покрытыми плотным, концентричным со стержнем слоем обмазки равномерной толщины.
Разнотолщинность обмазки ограничена ГОСТ, и ее превышение приводит к образованию «козырька» на торце электрода, который мешает управлять ванной. При выходе из пресса один конец электрода защищается от обмазки (механически - спецщеткой) для захвата электродержателем. Современный электродный пресс имеет производительность от 4,5 до 6,5 т электродов диаметром 4 мм в смену.
Электроды с малым содержанием влаги в пасте не нуждаются в предварительной сушке, а поступают сразу на окончательную сушку или прокалку, при которой удаляется по возможности вся влага из пасты, а покрытие приобретает максимальную механическую прочность за счет химических реакций между жидким стеклом и компонентами обмазки.
Окончательная сушка ведется при высоких температурах. Для электродов, не содержащих органических веществ, например типа УОНИИ13, температура прокалки 300- 400°С, а для обмазок с органическими веществами температура прокалки не выше 150-180°С во избежание разложения, расплавления органических веществ. После сушки электроды поступают на контроль и упаковку. Хранение электродов должно исключать доступ к ним влаги и влажности.
Комплекс современного оборудования для производства сварочных электродов по всей технологической линии (в последовательности операций), которое выпускается в России объединением «АО СпецЭлектрод» (Москва), это:
- Правильно-рубильный автомат СПЭЛ-400 с гильотинным ножом - для правки и резки на мерную длину проволоки из бухты или катушки до диаметра 6 мм.
- Валковая дробилка для среднего дробления СПЭЛ-620 с наибольшим размером загружаемого куска 100 мм, с наибольшим размером куска после дробления 20 мм.
- Шаровая мельница - СПЭЛ-600 и СПЭЛ-610.
- Бегунковый смеситель - СПЭЛ-500 предназначен для приготовления обмазочной массы, производительностью 400 кг в час.
- Брикетировочный пресс СПЭЛ-302, СПЭЛ-303 для изготовления брикетов обмазочной массы диаметром 110 165 мм, длиной 250; 280 мм соответственно.
- Прутковый питатель к электродообмазочному прессу - СПЭЛ-2011 для непрерывной подачи стержней в головку (мундштук) электродообмазочного пресса с диаметром стержней от 2 до 6 мм, длиной от 250 до 450 мм.
- Электродообмазочный пресс СПЭЛ-202, СПЭЛ-203 с усилием пресса 730; 1650 т, с максимальным давлением в рабочем цилиндре 720 кг/см с производительностью 4,5 и 6,5 т электродов диаметра 4 мм в смену.
- Зачистная машина с приемо-передающим транспортером - для зачистки от покрытия концов электродов после опрессовки (под электрододержатель сварщика).
- Конвейерная сушильно-прокалочная печь СПЭЛ-721 для сушки и прокалки электродов с температурой в зоне сушки 40- 150°С, в зоне прокалки - 100-400°С при производительности 3 т в смену.
- Туннельная сушильно-провялочная печь СПЭЛ-730 для сушки и прокалки электродов с рутиловым покрытием и для сушки электродов с основным покрытием, имеет 4 тепловые зоны с температурами от 30 до 150°С, производительностью 12 т в смену.
- Туннельная прокалочная печь СПЭЛ-732 с температурой 100-380°С имеет 4 тепловые зоны производительностью 12 т в смену (для электродов с основным типом покрытия).
- Сушильный конвейер (сушило) СПЭЛ-733 для подсушки электродов перед окончательной сушкой прокалкой с температурой в рабочей зоне от 40 до 80°С.
- Печь конвейерная элеваторная сушильно-прокалочная СПЭЛ-724 для сушки и прокалки электродов с производительностью Ют электродов диаметром 4 мм в смену со следующими последовательными температурными режимами: 60°С; 100°С; 140°С; 200°С.
- Установка для очистки обмазки с поверхности бракованных электродов до сушки - СПЭЛ-800.
- Прибор СПЭЛ-900 - для измерения разнотолщинности покрытия электродов.
- Рукавный фильтр всасывающего типа СПЭЛ-631 для улавливания пыли.
- Батарейный циклон СПЭЛ-632 для улавливания пыли от дробильно-размольных установок
- Стол для сортировки электродов.
- Бумагорезательная машина и различные контейнеры, поддоны и тележки для брикетов и электродов.
Насыщенность технологической линии оборудованием объясняется высокими требованиями к качеству электродов, идущих на самые ответственные объекты производства.
В настоящее время выпускается около 140 марок сварочных и наплавочных электродов. АО «СпецЭлектрод» выпускает всю гамму высококачественных сварочных электродов со специальными свойствами, а также углеродистых электродов с рутиловым, ильменитовым, основным покрытием.
Только высокооснащенная технология позволяет выпускать электроды высокого уровня качества, подтвержденного Сертификатами качества Госстандарта, гигиеническими Сертификатами Минздрава России.
По желанию покупателя (потребителя) электроды могут поставляться для поднадзорных объектов по допуску Морского и Речного регистров судоходства, либо по лицензии Госатомнадзора, либо по Сертификату Ллойд регистра (Великобритания).