Расчет поперечного сечения сварного шва. Большая энциклопедия нефти и газа
Режим сварки как совокупность характеристик (параметров) сварочного процесса, определяющих свойства получаемых сварных соединений, является компонентом технологии сварки. Для каждого способа и разновидности сварки применяют определенный набор параметров режима и их значений.
В специализированной литературе приводится множество рекомендаций по режимам сварки преимущественно в виде таблиц, данные которых составлены на основе результатов производственного опыта. Большинство приводимых данных относится к сварке углеродистых и низколегированных сталей, показывает числовые значения основных (обязательных) параметров для соединений разных типов и толщине металла в нижнем положении. Сведения об остальных параметрах режима и других условиях сварки приводятся эпизодически, не всегда, иногда в виде кратких записей в тексте. Но фактически их влияние тоже учитывается при отработке режимов сварки.
Результаты сильно различаются в зависимости от процедуры оценки усталостного действия. Корпуса котла предназначены для низкотемпературной и термической усталости в агрессивных средах котловой воды и пар. Их надежность и эксплуатационная надежность гарантируются комбинированными расчетами и внутренними ревизиями. Сплавы сопла проверяются только с внутренней поверхности визуально. Дефекты, которые угрожают работоспособности устройства, можно рассматривать как сварные трещины между пластиной и ниппелем.
Трещины создаются в результате длительной эксплуатации, и их образование сильно зависит от возникновения производственных дефектов. Удаление трещин обнаруживает внутренние дефекты, которые также необходимо удалить. Если не удалить, происходит повторение трещин после относительно короткого периода работы, и процесс удаления и растрескивания повторяется.
Специалисты Пермского нацио-нального исследовательского политехнического университета провели работу по изучению методики определения одного из «неосновных» параметров режима - числа проходов при многопроходной дуговой сварке.
В литературе имеется мало сведений об этом параметре режима. Известно, что металл повышенных толщин можно сварить с разным числом проходов. По экономическим соображениям предпочтительным представляется сварка с минимальным числом проходов, так как при этом будут меньше трудозатраты на зачистку швов от шлака после каждого прохода. Но должны учитываться и другие факторы.
Рисунок 1: Трещина в спящей втулке. Рисунок 2: Корень и шлак. Вклад посвящен проблеме дефектов в сварных соединениях сопла и способу ремонта поврежденного корпуса котла. Важно знать размер и распределение дефектов в сварном шве и натяжение сварного шва для оценки трещин, прогнозирования дальнейшего развития и принятия соответствующих мер.
Обнаружение дефектов в ниппельных суставах. Соски соединяются с корпусом котла «теленком» и угловым сварным швом методом ручной дуговой сварки. В сварных швах имеются дефекты производства. Рисунок 4: Передняя кромка перед сваркой. Описание метода и методологии не является предметом этого вклада. Наибольшая скорость дефектов составляет до 20 мм, но также имеются смежные дефекты, превышающие 1/4 окружности сопла.
Впервые вопрос о расчете числа проходов был изучен В. П. Демянцевичем, применительно к ручной дуговой сварке покрытыми электродами. Была показана связь оптимального числа проходов с необходимостью получения слоя наплавленного за один проход металла, имеющего определенную площадь поперечного сечения. Это положение связывается со скоростью перемещения электрода вдоль стыка. Как при слишком малой, так и при слишком большой скорости сварки возможно образование дефектов - непроваров и неудовлетворительное формирование шва.
Обнаружение дефектов поверхности ультразвука требует много времени. Этот метод неоднократно подтверждался в нескольких случаях. Точность измерения глубины дефектов с внешней поверхности мала, но достаточно для того, чтобы судить о дефектных процедурах механики разрушения. Преимущества этого контроля полностью продемонстрированы в тех случаях, когда необходимо контролировать развитие дефектов в период, меньший, чем время работы между общим ремонтом котла.
Напряжение в сварном шве с трещиной. Для получения количественного фона для оценки тяжести плоских дефектов в ниппелях был рассчитан метод терминального напряжения. Плоский дефект рассматривался как полная утечка трещины с внутренней поверхности ниппеля с глубиной, равной глубине соска. Лезвие тогда является только угловым сварным швом. В докладе мы рассмотрели следующие варианты напряженности.
Также впервые указано на необходимость сварки на разных режимах первого (корневого) и последующих проходов. Площадь наплавки за один проход связывается с диаметром электрода. Для ручной дуговой сварки рекомендованы следующие зависимости:
- для первого прохода F1 = (6/8) dэ,
- для последующих проходов
Fп = (8/12)dэ.
В этих формулах dэ - диаметр электрода в мм; F1 и Fп - площади поперечного сечения соответственно первого и каждого последующего прохода в мм2.
Притяжение трещины достигает значительных значений, а поле напряжения характеризуется коэффициентом интенсивности напряжения. Поскольку нас интересует напряжение перед трещиной, непосредственное окружение трещины было удалено с цветовой карты. Рисунок 5: Распределение объемных дефектов.
Окружная составляющая натяжения имеет аналогичный шаг, как показано на фиг. Что касается дальнейшего развития трещины, то аксиоматическая составляющая турбулентности является решающей составляющей трещины. Распределение осевого натяжного компонента показано на рис.
Общее число проходов n может быть определено по формуле:
n = (Fн. м. - F1)/Fп + 1,
где Fнм - общая площадь поперечного сечения наплавленного металла всего шва в мм2.
В настоящее время значения площадей поперечного сечения наплавленного металла для стандартных сварных соединений можно найти в изданных еще в советское время Общемашиностроительных укрупненных нормативах времени (ОУНВ) на разные способы сварки. Разработчики этих документов проводили расчеты в помощь нормировщикам сварочных работ, но они могут использоваться для решения других технических задач.
Из этих цифр видно, что момент воздействия существенно влияет на осевую составляющую натяжения, что, конечно, низкое. Влияние изгибающего момента на пониженное напряжение не является доминирующим и не превышает 10%. Рисунок 10: Осевой компонент растяжения при угловой сварке.
Ремонт после сварного шва. Как мы указывали в руководстве, необходимо было проверить обслуживание ремонта сварочных губок из-за трещин. Материал, поврежденный трещинами, включая производственные дефекты, был удален из веников. После регулировки краев краев полученная оплетка была свернута в первоначальную форму. Существует несколько случаев этого средства. Во-первых, необходимо измельчить значительное количество материала для коррекции угла. Сама веник удлиняется, и затем необходимо заполнить сварной металл металлическим швом.
В ОУНВ на ручную дуговую сварку в Приложении 10 приведены формулы для расчета площади поперечного сечения наплавленного металла всех сварных соединений из ГОСТ 5264-80, а в Приложениях 2-7 - рассчитанные по этим формулам значения площадей для разных толщин металла или катетов угловых швов.
Аналогичные, но еще более обширные сведения имеются в ОУНВ на дуговую сварку в среде инертных газов. Там так же в приложении приведены расчетные формулы, а сами рассчитанные по ним значения площадей в карты неполного штучного времени для каждого типа соединения по ГОСТ 14771-76 (для сталей) и ГОСТ 14806-80 (для алюминия и алюминиевых сплавов). Особенно важно, что в тех же картах неполного штучного времени имеются данные о количестве проходов.
На рисунке 11 показан вид локально отклоненных дефектов сварного шва форсунки перед сваркой. Еще одним недостатком является то, что он приварен в областях с высокой концентрацией натяжения. Мы надлежащим образом рассматриваем поперечную сварку, как показано на рисунке 13, в двух вариантах.
Сварка в поперечном сечении достигается за счет. В новом сварном шве в нижних слоях будут давления давления, которые будут препятствовать развитию трещин.
- Создание барьера против роста трещины.
- Увеличение расстояния между краем трещины и внешней поверхностью.
К достоинствам ОУНВ следует отнести большую дифференциацию интересующих нас данных по способам сварки (ручная, полуавтоматическая, автоматическая), типам электродов (плавящийся, неплавящийся), группам свариваемых материалов (углеродистые и низколегированные стали, высоколегированные и легированные, алюминий и алюминиевые сплавы, медь и медно-никелевые сплавы).
Дополнительным преимуществом является то, что он соединяется в области, которая имеет значительно меньшую натяжку. Этот метод ремонта можно использовать превентивно, исходя из результатов дефектоскопического осмотра и оценки срока службы сварочного ниппеля. Для сварки сварного шва, когда его недостаточно, чтобы развить трещины, целесообразно.
В случае, если в конце концов есть узел. трещины мешают значительной части сварного шва, включая угловой сварной шов, после чего рекомендуется полная замена ниппеля. Для обоих методов, сварки и обмена с перекрестной сваркой, технология была обработана.
К сожалению, в специализированной литературе нет аналогичных данных для сварки под флюсом. В принципе их можно получить расчетами, учитывая, что основные виды разделки кромок по ГОСТ 8713-79 аналогичны таковым для сварки в защитных газах и значит можно использовать те же формулы для расчета площадей поперечного сечения наплавленного металла, а конкретные значения конструктивных элементов подготовки кромок и размеров швов имеются в ГОСТе. На данный момент такие расчеты не проводились.
Рис. 13: Поперечная сварка. Исходя из результатов, в конечном итоге оцените надежность превентивной поперечной сварки. заменяющий ниппель.
- Сварные швы ниппелей не проверялись во время производства.
- Поэтому целесообразно проверить эти сварные швы на наличие внутренних дефектов.
Твердые неразъемные соединения двух металлических деталей по металлу, которые при расплавлении и диффузии приклеиваются к связанным частям, не плавя эти компоненты. Толщина слоя, 25 мм Металлы - низкий зазор, высококачественная контактная поверхность Мягкие материалы - шероховатая контактная поверхность Условия качества соединения: адгезия - клей проникает в поры и неровности поверхности сцепления - в результате сил притяжения между молекулами адгезива.
Современные методы и средства статистической обработки данных позволяют значительно упростить работу пользователей. В частности табличное представление данных во многих случаях можно заменить аналитическими моделями. Такую свертку таблиц провели в отношении данных о площадях наплавленного металла для разных типов соединений из ГОСТ 5264-80 и 14771-86. Расчеты показали, что значения площадей Fнм достаточно точно описываются формулами вида полинома второй степени.
Они часто используются в сборках и во всей автомобильной промышленности. Он используется для соединения большинства комбинаций стекла, металла и пластика, в которых по крайней мере одна поверхность пропускает ультрафиолетовое излучение. В зависимости от температуры и давления, необходимых для затвердевания клея: при нормальной температуре около 20 ° С при повышенной температуре от 20 до 200 ° С при высокой температуре около 200 ° С при высокой температуре около 200 ° С и при давлении связанных материалов Металл: Общие промышленные. машиностроение для соединения листов, резервуаров, рамок труб, ступиц вала и т.д.
Fнм = b1 + b1S + b2S2,
где S - толщина свариваемых деталей (или катет шва для соединений с угловыми швами); b0, b1, b2 - коэффициенты уравнения.
Для каждого типа сварного соединения коэффициенты индивидуальны. Чтобы рассчитать требуемую площадь, достаточно найти соответствующую формулу и подставить в нее значения толщины металла S (или катет шва). Этим полиноминальные модели выгодно отличаются от приводимых в литературе общих формул для расчета площадей.
В качестве примера приведены две формулы для расчета площади Fнм в соединении С17 - одну из ОУНВ, другую - полученную статистической обработкой данных:
Fнм = Sb + (S - c)2 tgα + 0,75eg,
Fнм = -9,36 + 3,26S + 0,33S2.
Видно, что для расчетов по первой формуле необходимо для каждой толщины металла брать из ГОСТа еще пять значений конструктивных элементов подготовки кромок и размеров швов, тогда как во втором выражении присутствует только одна переменная - толщина металла S.
Таким образом, в рассмотренных источниках информации есть данные об общих площадях поперечных сечений наплавленного металла для стандартных сварных соединений. К сожалению, ОУНВ были изданы более 20 лет тому назад, с тех пор не пересматривались и не переиздавались, поэтому в настоящее время они малодоступны для широкого круга специалистов.
Еще большую проблему создает неопределенность рекомендаций о расчетных значениях площадей F1 и Fп для первых и последующих проходов (см. таблицы 1 и 2).
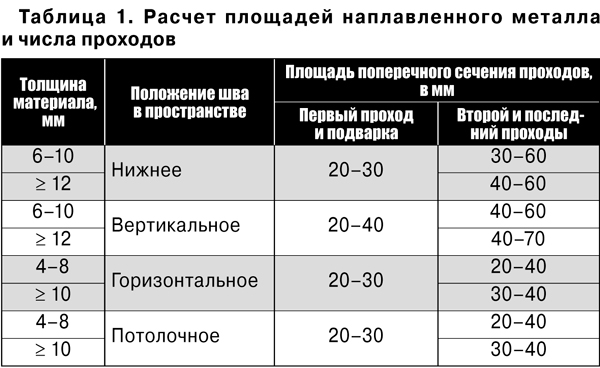